In dynamic workplaces, developing and implementing a corrective action plan is essential. Far from just responding to incidents and audits, it's a strategic approach to enhance employee protection, reduce operational costs, and boost productivity.
This guide delves into the crucial steps necessary to design and execute an impactful corrective action plan, emphasising the importance of learning from incidents and adapting processes to prevent their recurrence.
Explore with us the key elements of corrective action, as we pave the way for a safer, more efficient workplace environment.
Understanding Corrective Action
When it comes to upholding workplace safety, employers are ethically and legally responsible for enforcing two types of actions: corrective and preventive actions. While they are similar, there is a distinct difference.
Corrective action is reactive, addressing identified problems in incidents that have already occurred. It involves identifying the root cause of a problem and taking steps to fix it, thus preventing its recurrence. In contrast, preventive action is proactive, aiming to minimise and eliminate potential anticipated incidents before they occur.
Corrective and preventive action is vital for maintaining a safe and compliant workplace, ensuring both the well-being of employees and the smooth operation of business processes.
In this article, we will focus on the former type—corrective action. According to the ISO 45001, a global standard for the management of occupational health and safety, corrective action is defined as:
- an action to eliminate the cause(s) of nonconformity or an incident and to prevent recurrence; and
- an action to eliminate a detected nonconformity.
It is important to take note that incidents can still happen in the absence of nonconformities. Therefore, conducting regular risk assessments and implementing a robust hazard reporting program are critical components of a comprehensive health and safety strategy.
Legal Foundations of Corrective Action
The Management of Health and Safety at Work Regulations 1999, specifically Regulation 5, puts employers under the obligation to conduct “effective planning, organisation, control, monitoring and review of the preventive and protective measures.”
Corrective action procedures form a critical component of the “preventive and protective measures” mentioned in Regulation 5. For businesses, implementing these measures helps to ensure compliance with legal standards while fostering a culture of safety and continual improvement.
The Importance of Corrective Action: 5 Benefits You Need to Know
There are numerous reasons why it is beneficial for organisations to take corrective action. Here, we list the top five benefits of corrective action you need to know.
1. Protection of Employees
The primary goal of corrective action is to prevent the recurrence of other incidents. Doing so plays a crucial role in protecting employees from potential harm or serious injuries.
Implementing these measures effectively ensures a safer working environment, significantly reducing the likelihood of future incidents and underlining the organisation's commitment to employee well-being.
2. Cost-Saving and Economic Benefits
Incorporating corrective actions significantly contributes to cost-effective operations by minimising incidents that lead to property loss or damage.
Beyond the direct savings, these actions also prevent serious injuries and work-related ill health, which can have cost-saving benefits for individuals, employers, and the government.
According to the HSE's Health and Safety at Work Summary Statistics for Great Britain 2023, workplace injury and new cases of work-related ill health in 2021/2022 resulted in considerable costs, including:
- £12.2 billion in costs borne by individuals
- £3.9 billion in costs borne by employers
- £4.6 billion in costs borne by the government
These figures emphasise the cost-effective nature of corrective actions and the financial benefits of a safer workplace.
3. Boost in Productivity
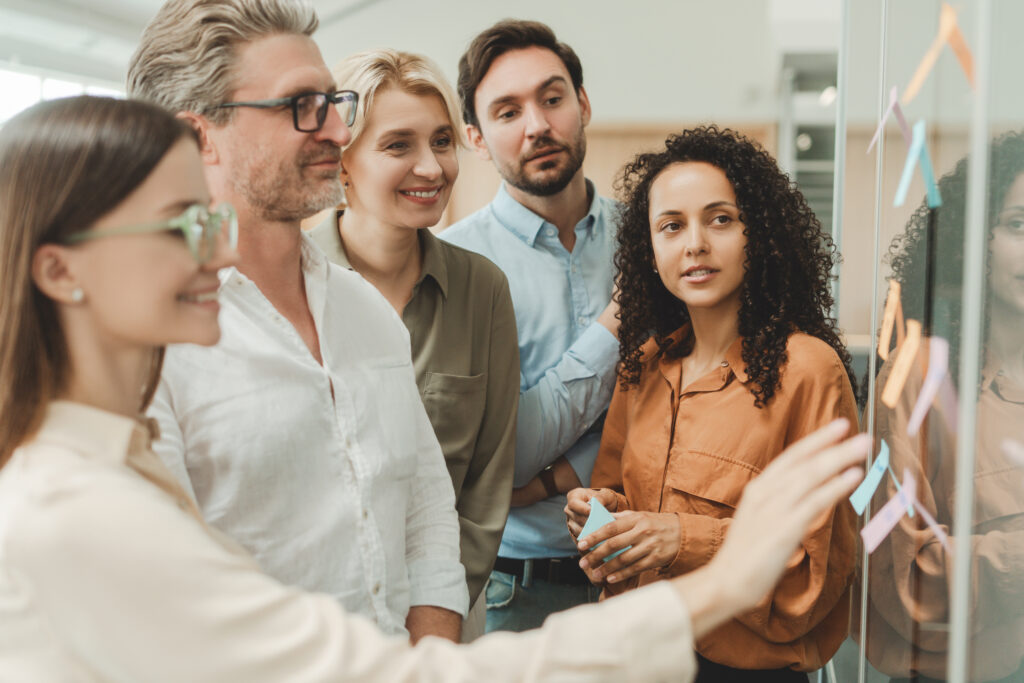
A safe working environment is every employee’s right. Beyond the legal obligation, demonstrating care for safety through corrective actions communicates to employees that their well-being is a top priority. This fosters a sense of security and value among the workforce, which in turn can elevate morale and enhance productivity.
Supporting this, a study by the Australian government revealed that investing in workplace health and safety leads to “higher productivity levels as a result of improved morale, motivation, commitment and/or engagement.”
4. Legal Protection
Diligent implementation and documentation of corrective actions can serve as a protective shield for your company against potential litigation.
In the event of a legal investigation following an incident, these records of corrective actions can be pivotal. They provide tangible evidence that your company has adhered to its legal responsibilities as outlined in the Management of Health and Safety at Work Regulations 1999.
Additionally, these records illustrate your company’s dedication to maintaining and improving health and safety standards in the workplace, a factor that can be influential in legal proceedings.
5. Facilitate Insurance Claims
Effective corrective actions play a crucial role in facilitating the insurance claim process following an incident.
By providing detailed and accurate information through these actions, insurers receive the essential data needed to assess and process claims efficiently.
Different Types of Corrective Action
Having explored the numerous benefits of corrective action, let's delve further into the various types of corrective actions, along with practical examples.
1. Corrective Action to Reduce the Risk of Incidents
Once you have identified what caused the incident, the first type of corrective action you can take is to reduce the risk of incidents by addressing the direct cause.
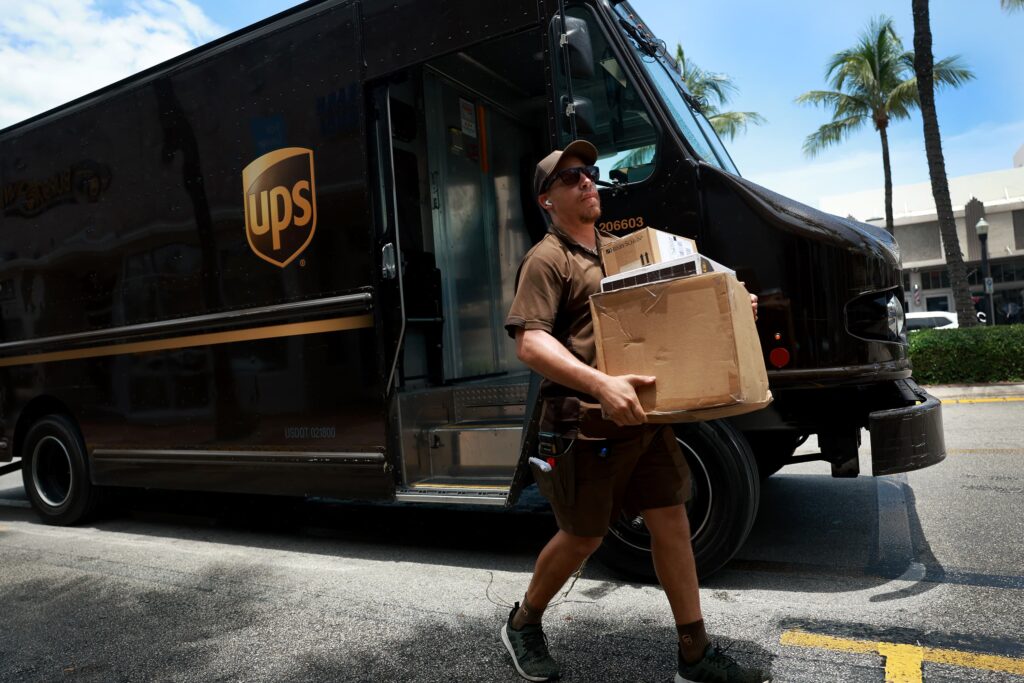
[table id=7 /]
2. Corrective Action to Improve Processes
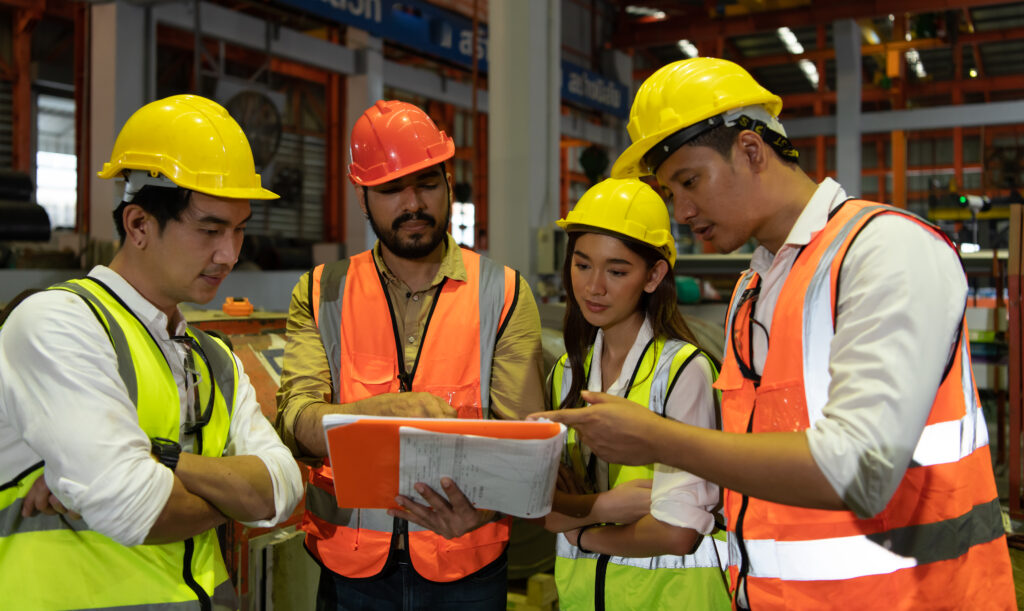
In situations where it's not feasible to eliminate the direct causes of incidents, such as adverse weather conditions like icy roads or low visibility, the focus shifts to improving processes. This type of corrective action becomes relevant when potential improvements are identified during internal audits and inspections.
Process enhancements can span various areas, ranging from refining communication processes to improving lone worker and remote team monitoring.
[table id=8 /]
3. Corrective Action to Train Staff
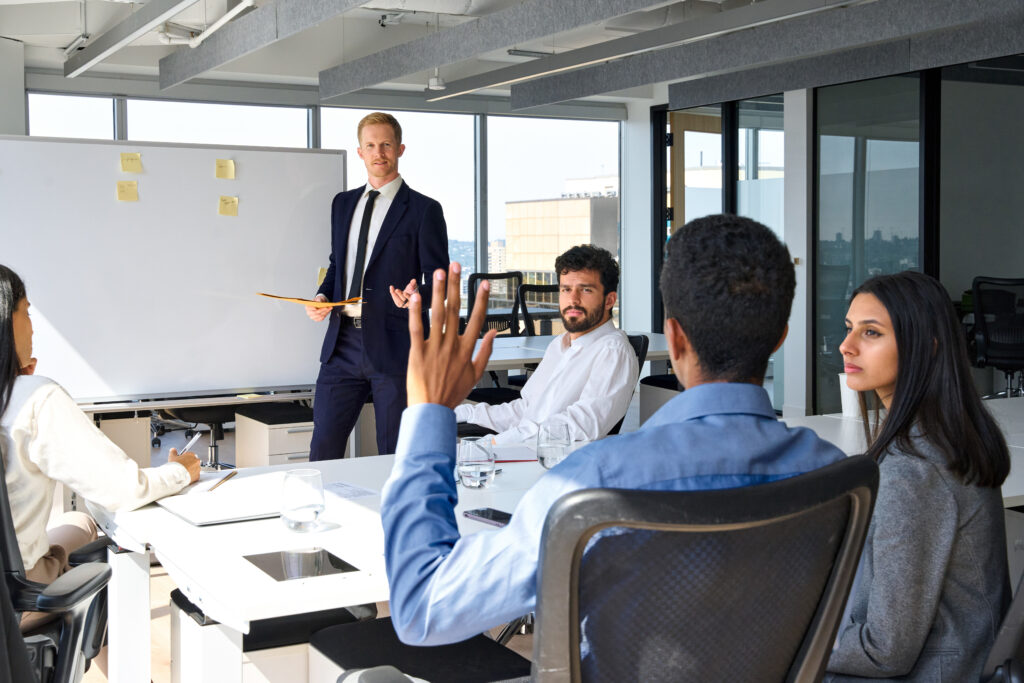
Often, addressing an incident effectively involves a combination of different corrective actions. For example, in the case studies of UPS and Pullin Shearing mentioned earlier, an essential component of their corrective strategies would include training their drivers and shearers, respectively.
Staff training encompasses more than just familiarising employees with health and safety protocols and the importance of avoiding nonconformity. It extends to enhancing the overall skill set of the workforce, equipping them to respond adeptly to emergencies and to apply critical thinking to prevent incidents.
This approach to training reinforces safety procedures while empowering employees with the competence and confidence needed to handle challenging situations effectively.
4. Corrective Action to Raise Awareness
A key aspect of corrective action is to elevate awareness about workplace hazards. This can be effectively achieved through various means, such as hazard warnings and constant reminders.
Even with well-trained employees who understand their work environment's risks, visual cues like warning signs are essential to maintain vigilance.
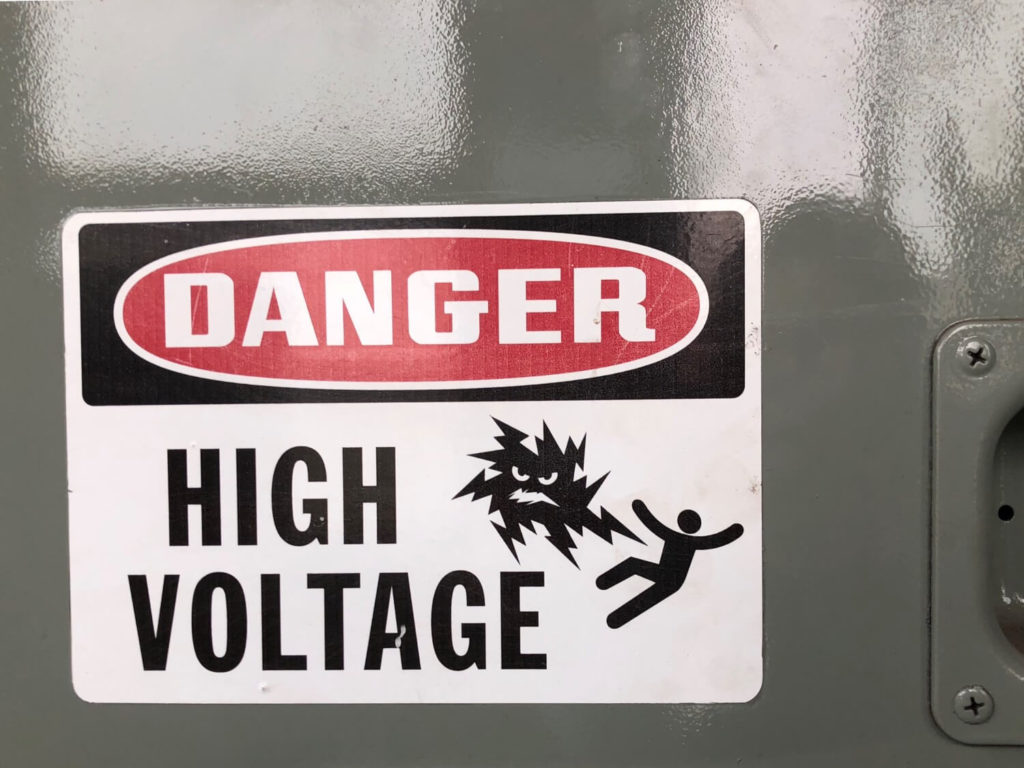
These signs are particularly vital in protecting lone or remote workers. For instance, displaying a CCTV warning sign can act as a deterrent, potentially discouraging acts of violence or robbery by instilling the fear of identification and consequent legal action.
Beyond physical signs, other methods to reinforce safety awareness include distributing company newsletters or brochures that consistently educate and remind employees about health and safety best practices. This ongoing engagement with safety information helps in embedding a culture of awareness and precaution, contributing significantly to a safer workplace.
5. Corrective Action to Replace or Repair Equipment and Assets
While regular maintenance of equipment and assets should be part of every health and safety policy, sometimes it still takes a tragic incident to reveal overlooked issues.
When faulty equipment or assets are identified as the direct cause of an incident, it's imperative to take immediate corrective measures. These measures may include halting the use of the problematic equipment or assets until they are either repaired or replaced.
[table id=9 /]
Corrective Action Procedure: A Step-by-Step Guide
Understanding the various types of corrective action is crucial, but equally important is mastering the systematic process of identifying and implementing the most appropriate corrective action for a given situation.
This section provides a detailed guide to executing corrective actions effectively.
Step 1: Root Cause Analysis
Investigate, identify, and verify the root cause. Even if the underlying cause seems obvious, it’s important to undergo thorough root cause analysis to investigate every possible angle with vigilance. A comprehensive root cause analysis sets the trajectory for subsequent steps and solutions.
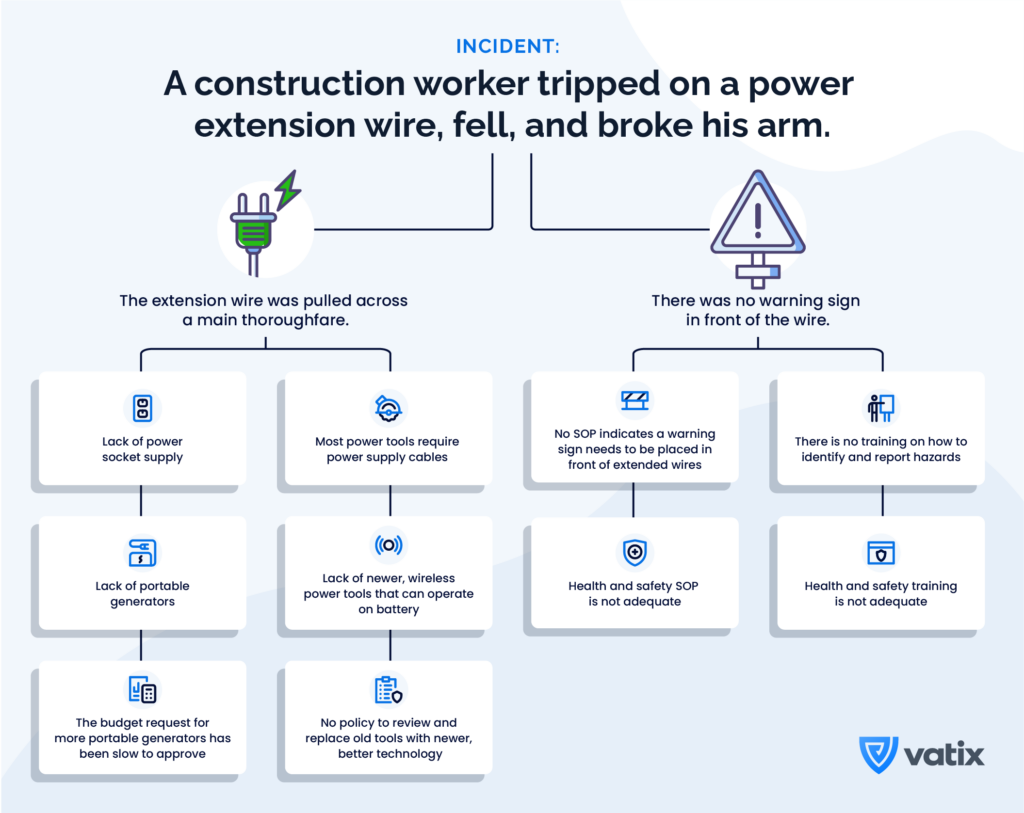
To ensure a thorough investigation, it's advisable to incorporate as many of the following methods as possible, where relevant:
- Conducting interviews with personnel and witnesses involved in the incident
- Engaging in discussions with the manager or supervisor overseeing the area where the incident occurred
- Consulting with third-party experts and seeking inspections by relevant authorities
- Reviewing scientific research related to the incident or the industry
- Analyzing industry reports to understand broader trends and risks
Each of these sources provides valuable insights, contributing to a well-rounded understanding of the incident and guiding the development of effective corrective measures.
Step 2: Discuss and Identify Appropriate Corrective Actions
After completing a thorough root cause analysis, the next critical step involves a collaborative discussion on potential corrective actions.
Engage your team and any relevant authorities to brainstorm and evaluate various corrective measures. The objective here is to assess the feasibility, effectiveness, and implications of each potential action before deciding on the most suitable ones to implement.
Consider the following key questions during the evaluation process to guide your decision-making:
- How effectively will this action minimise the risk of future incidents?
- How quickly can we roll out this corrective action?
- Will this action help us achieve or improve HSE compliance?
- How easily can our team and other stakeholders adopt this corrective action?
- What are the resources and investments required for this action?
- Does this action align with our budgetary plans?
By systematically addressing each of these questions, you can ensure that the chosen corrective actions are not only effective in addressing the identified problems but also practical and sustainable within the context of your organisation's operations and resources.
Step 3: Design a Corrective Action Plan
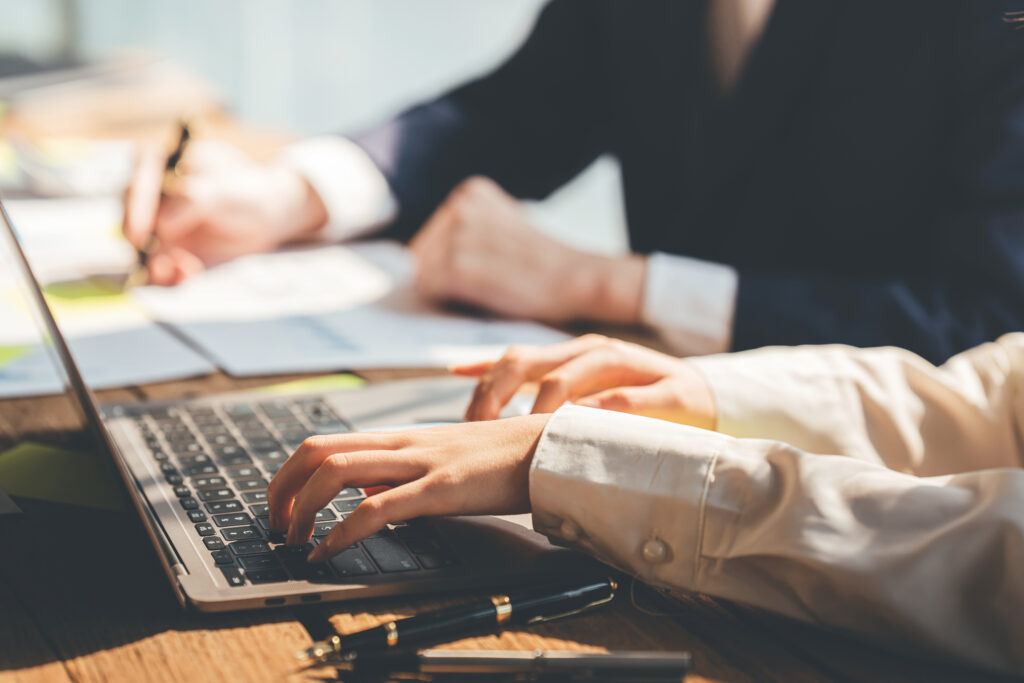
Once you have identified the corrective actions to take, the next step is to design a corrective action plan. This plan serves as a roadmap for implementation and should outline the following components:
- A list of specific tasks necessary to implement corrective actions
- Achievable and realistic deadlines for the tasks
- The individuals or teams responsible for each task
The effectiveness of a corrective action plan hinges on its clarity, feasibility, and the commitment of all involved parties. By meticulously designing this plan, you establish a structured approach that guides your team through the corrective process, enhancing the likelihood of successful and timely implementation.
Step 4: Submit the Correction Action Report
The next step is to create a corrective action report detailing the incident overview, findings from the root cause analysis, the corrective actions chosen, the timeline, and the people responsible for each action.
After compiling the report, it's essential to formally submit it and make it accessible to all involved personnel. This ensures transparency throughout the organisation and facilitates a unified approach towards the implementation and monitoring of the corrective actions.
Step 5: Follow up
Follow up on tasks with the people responsible according to the proposed timeline.
Step 6: Review
Create a schedule to review the effectiveness of the corrective action plan. This could range from weekly to quarterly to annually, depending on the severity of or risks associated with the incident.
How to Implement a Corrective Action Plan in Your Organisation
A corrective action plan can have many complex moving parts. This means many tasks depend on other tasks, making communication and follow-up critical to the success of any corrective action procedure.
All of this can be a lot to manage on top of the regular, daily tasks you’re responsible for in the workplace. Additionally, implementing corrective action plans via manual methods such as emails, SMS, mobile messaging apps, or verbal communication can lead to many things falling through the cracks.
Juggling these responsibilities alongside everyday workplace duties can be challenging, especially when relying on manual methods like emails, SMS, mobile messaging apps, or verbal communication for implementing corrective action plans.
Other than being time-consuming, these manual processes are prone to oversights, causing things to be overlooked or missed, as well as miscommunication and errors. The difficulty in tracking discussions, task progress, and emerging issues can further complicate management.
A practical solution to enhance efficiency and reduce errors in implementing a corrective action plan is by using a task management platform that everyone involved can access. This will significantly streamline communications, task delegation, issue discussions, and follow-up processes. This approach ensures a more organised and effective implementation.
Our platform allows organisations to create corrective actions and relate them to a particular incident or audit record. Key features of this platform include:
- A centralised hub where all users can conveniently access and view their assigned corrective actions.
- Easy assignment of corrective action tasks and deadlines to team members via web or mobile app.
- Track and monitor the progress of corrective actions across your team.
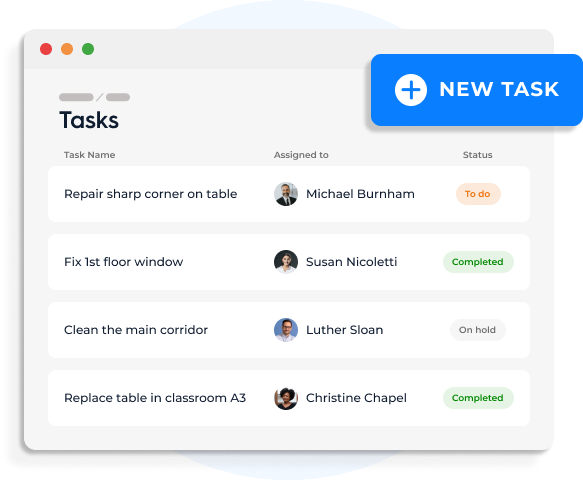
Summary
Taking corrective action after an incident is an employer’s moral and legal responsibility towards their employees and the wider public. Implementing the right corrective actions is a six-part procedure that requires collaboration across various levels of the organisation.
A critical part of keeping a corrective action plan on track is thorough documentation and clear, trackable communication. A task management platform can help you track, organise, and review the progress of your corrective actions.
We've created a Corrective Action Plan Checklist that will help you tailor the information you should be collecting in your task management platform. Download the checklist below to get started.
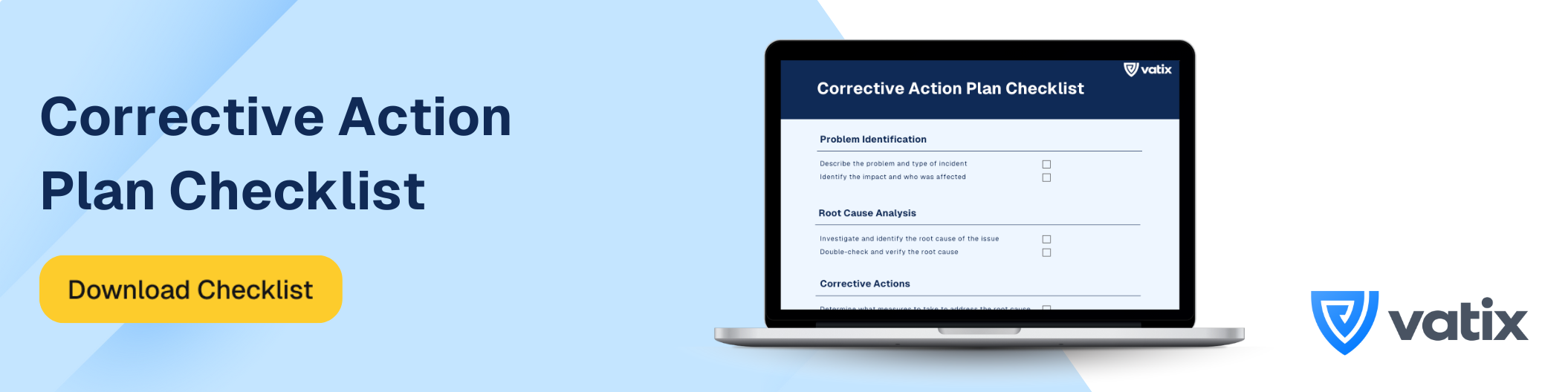