Working at height remains one of the leading causes of workplace injuries and fatalities, and many businesses still aren’t doing enough to protect their workers from the risks they face on a day to day basis.
The Health and Safety Executive (HSE) published their annual fatality statistics in July 2025. The report showed that falls from a height were the most common cause of fatal injuries with 35 deaths in 2024/2025. This represented over a quarter of all worker deaths so is an area that needs significant attention.
The Work at Height Regulations 2005 sets out the critical guidelines for businesses that require their staff to carry out duties from above ground level, helping to limit the number of injuries and fatalities stemming from accidents involving falls.
Following these guidelines isn’t just a matter of adhering to HSE guidelines, but also protecting at-risk workers from the hazards they come up against every day. Employers are liable should any incident occur at work, so it’s essential that organisations are aware of the rules and regulations surrounding working at height.
In this article, we will cover what employers need to know about the regulations surrounding working at height, risk assessments and other related policies.
Conduct a working at height risk assessment
The nature of dangers faced by employees working at height may seem evident at first glance, but there are many particulars that employers can’t afford to miss.
For example, preventing nasty falls from high up is essential, but employers also need to consider risks such as:
- Potential causes of a fall such as fragile roofs and roof lights
- Adverse weather conditions
- The nature of the surface on which the worker would fall, including holes in the ground, fragile surfaces, or other dangerous materials
- Unsecured hazards on another level, which could fall and injure the worker
This is why businesses need to conduct a thorough working at height risk assessment as soon as possible, whether it’s for the first time or in the form of an update.
Before employees are asked to work in risky, high-up positions, you should consider whether this is strictly necessary to complete the task in question. If it is, then supervisors must ensure that the correct equipment is on hand at all times. This includes things that get and keep workers where they need to be, such as ladders and scaffolding.
A practical risk assessment will identify the principal risks faced by staff, how they can be mitigated, the tools and equipment needed to do this, and the resulting policy.
Get savvy on working at height regulations
In order to mitigate or eliminate the hazards of working at height, all equipment used on the job needs to be checked regularly to ensure it is as safe as possible.
This should ideally be done every time before use, and never less frequently than every seven days. This is to ensure nothing needs repairing or replacing before work begins. If equipment comes from a third-party company, then it should include a record of when the last inspection was performed.
You should also make sure that there is nothing that could injure someone from unexpected places, such as debris falling from a higher surface. To avoid this, all objects should be secured safely so that they cannot fall by accident. Extreme caution should be taken when conditions such as windy weather arise.
Remember - the safest thing to do is avoid working at height at all.
Everyone involved in working at height needs to be ‘competent’ enough to do so. Competent in this context means someone who is equipped with the skills, training and experience required to perform their tasks in the safest way possible.
This applies to everyone, from the person doing the work to those planning and supervising the job. Your company should already have someone in charge of enforcing health and safety rules.
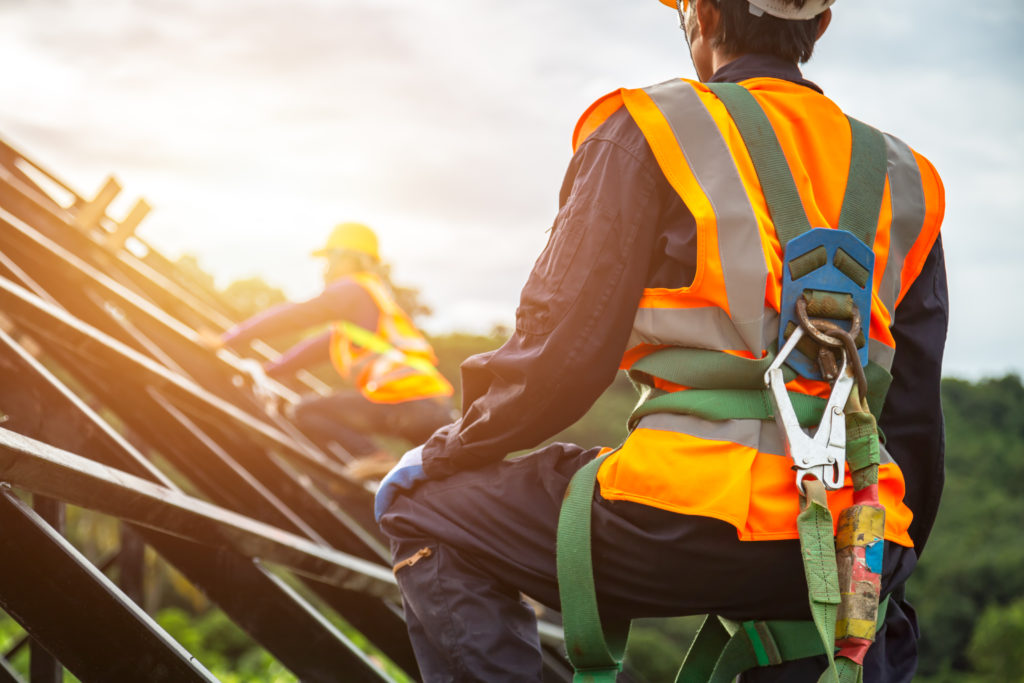
Working at height training
While minimising the need for working at height safety protocols in the first place can be incredibly important, the optimal equipment and working at height training will go a long way towards safeguarding workers from injury when accidents can’t be avoided.
All new and updated rules and policies that come from risk assessments should be communicated clearly to avoid misunderstandings, and some form of safety training should be given to those who will be working at height as part of their roles.
It is the employers’ responsibility to make workers aware of the rules and working at height regulations that have been put in place.
There are several ways to do this, from placing informative posters where they’re most likely to be seen to handing out leaflets to relevant staff.
Collective and personal protection
As for getting the right tools in place, these are generally split into two categories - collective protection and personal protection.
As the name suggests, collective protection is about enlisting equipment and other safety measures that keep the entire team safe, such as guard rails, ladders, or performing the initial risk assessment.
Personal protection, meanwhile, is anything that applies to at-risk or lone workers on an individual level, such as harnesses or personal safety devices.
Lone worker alarms, for example, allow employees and organisations to have peace of mind when it comes to potential incidents. Coming equipped with a dedicated SOS button that the user can push should they become injured or find themselves in a dangerous situation, many also have a Man Down sensor included.
These sensors automatically detect when the wearer has fallen, letting the chosen contact or monitoring centre know if the alert is not manually switched off. This can be potentially life-saving for employees who fall from a high surface.
Working at height is one of the most dangerous jobs in the lone worker space, coming in fourth place for the leading causes of accidents in the workplace after slips, trips or falls on the same level, handling, lifting or carrying, and being struck by moving object.
Extra caution must be taken to keep employees as safe as possible while also adhering to the working at height regulations as laid out by the HSE. To do this, organisations must ensure they are as prepared as possible.
How can we help?
Vatix works with a massive range of companies to help them uncover their specific health and safety needs, providing industry-leading lone worker alarms, EHS software and more. This includes those with employees required to work at height.
To find out more, sign up for a demo here.