A near miss, also known as a close call, is a workplace incident that almost resulted in an injury, fatality, or property damage — but didn't.
Some employers and employees view near-misses as too minor and inconsequential to report as a health and safety issue.
Many people feel this way because they do not fully understand how reporting near-misses can improve workplace safety. Others may feel afraid they will be blamed for a near miss, while a few may simply be confused about what kind of near misses need to be reported.
This article will break the confusion surrounding near misses, explore the importance of reporting near misses, and go through a checklist of how to report them.
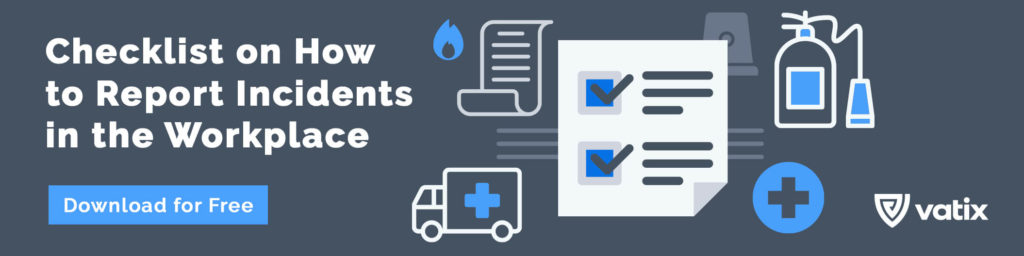
What is a near miss? Near miss definition and legal obligations
The HSE defines a near miss as “an event not causing harm, but has the potential to cause injury or ill health”. The term ‘near miss’ also includes ‘dangerous occurrences’ as defined in the Reporting of Injuries, Diseases and Dangerous Occurrences Regulations 2013 (RIDDOR).
Every organisation’s incident reporting procedure should cover four types of incidents: unexpected events, near misses, adverse events, and awareness events. Organisations are also legally obliged to report near misses under RIDDOR to the local authorities.
The relationship between near misses and accidents
Hindsight, as they say, is 20/20. It’s easy to look back and analyse what happened after things have gone wrong. While a post-analysis is necessary to deliver valuable insights, it can never reverse an accident, injury, or fatality.
What if you could use foresight to prevent things from going wrong in the first place? What if you could identify and avoid the red flags before they become accidents? This is the premise and objective of reporting near misses.
The Accident Triangle theory, which has been described as a cornerstone of 20th-century workplace health and safety philosophy, states that there are 300 near misses for every serious accident. HSE’s evaluation follows a similar pattern, with roughly 90 near misses estimated for every accident.
Critics of the Accident Triangle theory proclaim the numbers’ inaccuracy, especially because of variability across different industries. However, for the purposes of reporting near misses, the ratio accuracy of the Accident Triangle is insignificant.
What matters is the simple principle behind the Accident Triangle theory: reduce the number of near misses, and you’ll reduce the number of incidents that cause injury, fatality, or damage.
Benefits of reporting near misses
Since the same factors that lead to a near miss can lead to an accident, monitoring near misses can help you take proactive action to:
- Identify systemic health and safety issues
- Identify patterns in when or how things go wrong
- Improve workplace health and safety
- Improve health and safety training
- Improve equipment and property maintenance
- Remove, reduce, or mitigate risks and hazards
- Encourage employees to comply with health and safety policies
- Enhance the safety culture
- Develop more effective health and safety policies
- Reduce the number of workplace incidents
- Save time and money for the organisation
We can see many of these benefits in action with the following case study.
[table id=6 /]
The difference between reporting a near miss and reporting a hazard
A near miss and a hazard are similar in the sense that both did not end up in an injury or damage. It’s easy to get confused between the two. How do you know if you should be reporting a near miss or reporting a hazard?
Here is a decision tree flowchart that can help you.
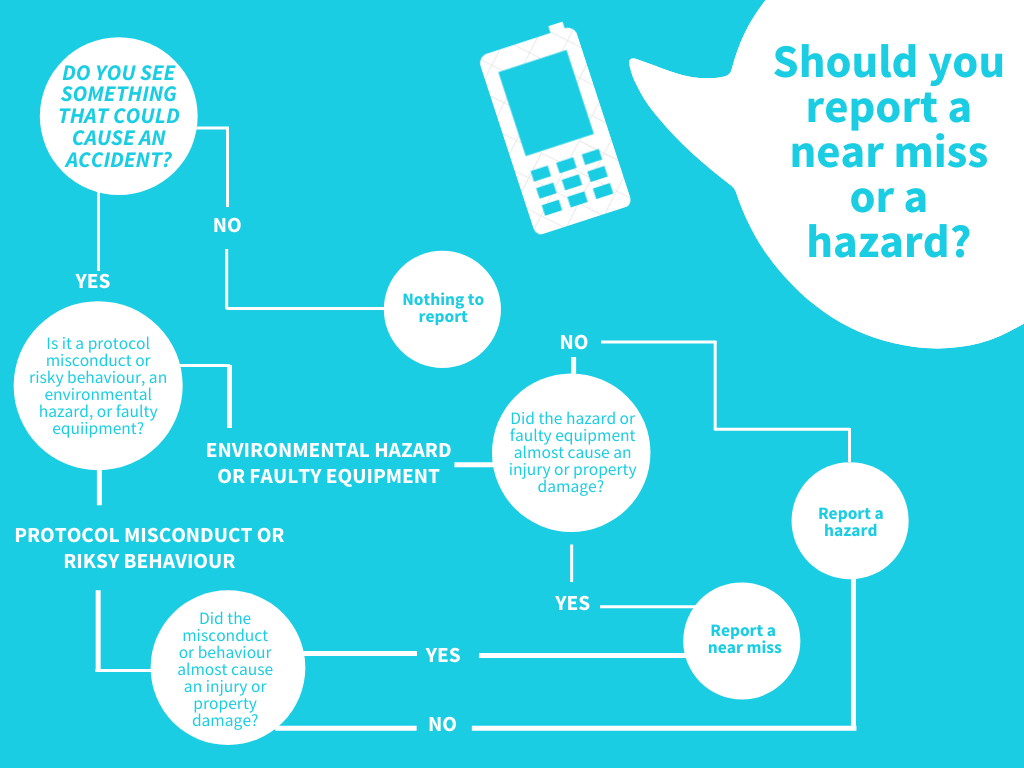
The following examples can help further clarify the difference between a near miss and a hazard.
[table id=4 /]
How to report a near miss
A near miss is an incident that did not lead to injury or damage. Thus, reporting near misses follows the same procedure as reporting any other accident. For guidance on how to effectively report a near miss, follow this quick checklist:
Step 1:
Clear the area & inspect the incident location for immediate risks.
Step 2:
Confirm that the workmate has first aid assistance. For a near miss incident, confirm that there are no injuries.
Step 3:
Report the incident to superiors for further investigation.
Step 4:
Log the incident into the company's preferred incident reporting system.
Step 5:
Have an impartial, responsible, third party investigate the incident.
Step 6:
Evaluate if it is a RIDDOR-reportable incident and report it as such.
Step 7:
Take measures to reduce the possibility of a similar incident occurring.
For more details on each step, download the full checklist guide here. We highly recommend you and your team familiarise yourselves with this checklist so you’ll know what to do when a near miss happens.
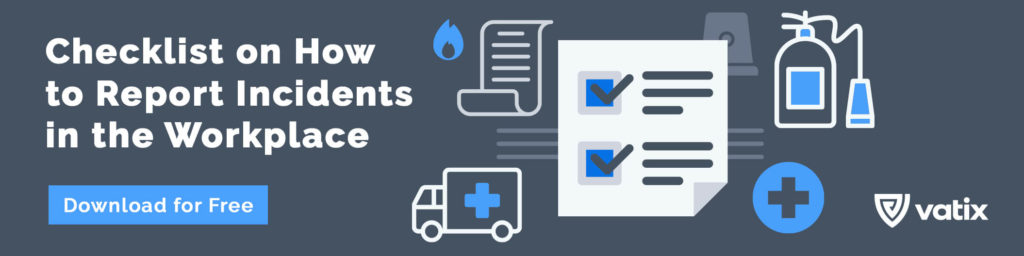
When it comes to Step 4 of this checklist—logging the incident—it’s important to describe any hazards or dangerous behaviour that caused the near miss. Here’s a sample of what an incident report of a near miss could look like.
[table id=5 /]
When writing a near miss incident report, keep these tips in mind:
- Write in a third party voice except when quoting people.
- Stick as closely as possible to stating the facts.
- Avoid writing emotional statements.
- Avoid finding someone to blame and stay focused on the objective of workplace safety.
- Include relevant details but write as concisely as possible.
- Validate the report by getting everyone who was mentioned in the report to sign off to confirm the information is accurate.
How to implement a near miss reporting program
The benefits of reporting near misses are clear. How can you implement a near miss reporting program that your employees will not shy away from?
The solution is to incorporate near miss reporting into your organisation's overall hazard reporting system. For more details on how to do this, read this guideline on the 6 pillars of reporting health and safety issues.
Creating a work culture where employees understand the importance of reporting hazards and near misses — and feel safe to do so without the fear of being blamed or punished — is also important to ensure your near miss reporting program can successfully improve your organisation’s safety and security.