Many organisations still use spreadsheets to conduct inspections, and it’s easy to see why.
Most people are already used to spreadsheets, so there’s low resistance. Spreadsheets are also free or relatively inexpensive to use, and they’re flexible and customisable.
However, it’s been almost 40 years since spreadsheets entered the mainstream workplace in the 1980s. Technology has since evolved at neck-breaking speed.
In many cases, spreadsheets are no longer the cutting-edge technology that once boosted office productivity.
Companies operating on legacy systems like spreadsheets could likely lag behind the competition. This raises the question, “Can my company still rely on spreadsheets for inspections?”
This article answers this important question by giving you eight solid reasons to stop using spreadsheets for inspections in the workplace.
What impact do inspections have on your business?
Before we jump into the eight reasons why spreadsheets are the wrong tool to use for inspections, let’s review the impact that inspections have on your business.

As you’re aware, there are several types of inspections. Safety inspections, property inspections, asset maintenance inspections, vehicle inspections, environmental health inspections, quality control inspections, and more.
What do all these inspections have in common? They safeguard your organisation’s most important assets: your people, property, equipment, fleet, and products.
Can you trust spreadsheets to take care of your most important assets? Are you willing to risk the impact that outdated spreadsheets could have on your profits?
Keep these questions in mind as you read through the disadvantages of using spreadsheets to conduct inspections.
8 disadvantages of using spreadsheets for inspections
1. Higher likelihood of sub-par or incomplete inspections
When spreadsheets first hit the mass market, they were made for the desktop computer with a big screen, mouse, and keyboard. They were not designed for small-screened mobile devices, which didn’t exist in the mainstream commercial space then.
However, inspections are not typically conducted in front of a desktop computer.
Instead, your employees are conducting inspections on the factory floor, at construction sites, out in the field, on the road, at different properties, and so on.
In other words, inspections require mobility and hence, mobile-compatible software.
Even though mobile-friendly views of spreadsheets are now available, they are still not optimal for inspections because:
- It’s tedious to scroll through multiple columns and rows of a spreadsheet to find the right field to input data.
- It’s easy to miss questions on a spreadsheet, especially if the template has a long checklist or is across multiple sheets.
- The software would not alert the user if a field was accidentally not filled out.
All these difficulties add up to producing a higher number of sub-par or incomplete inspections.
2. Difficult to format
Spreadsheets are like an open canvas. You have the flexibility to customise a form or inspection template in any way you like, which sounds great at first. However, it can take up a lot of time.
There are no easy drag-and-drop functions. Adjusting the size of the columns and rows can be inconvenient. It is also difficult to navigate the sheets and find specific information as there are no headers or footers.
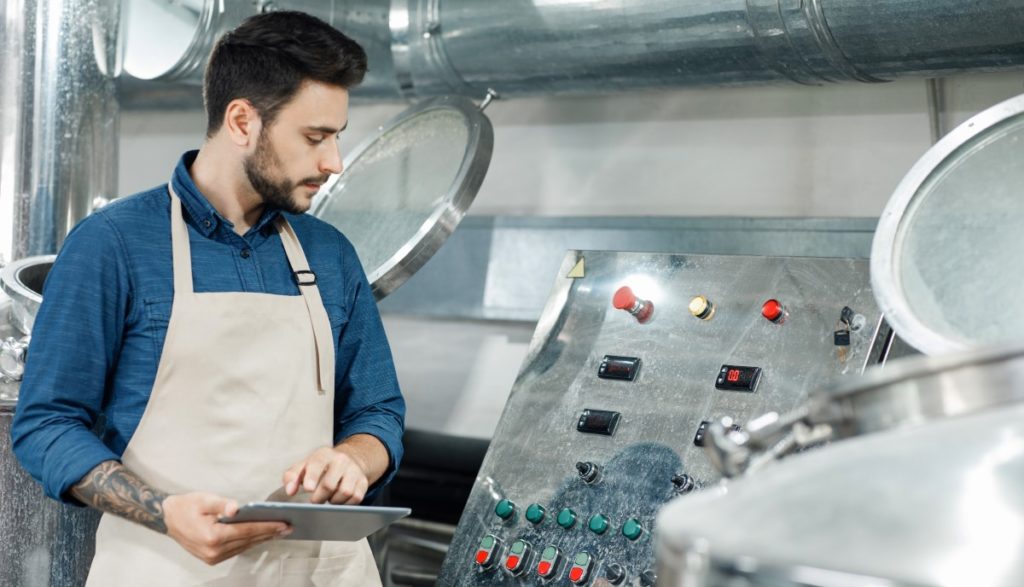
While spreadsheets let you do dropdown menus and conditional formatting, it still takes a bit of technical know-how that not everyone knows how to use.
Finally, just because you’ve formatted an easy-to-read template on a desktop doesn’t always translate to being easy to read on mobile.
While trying to format an inspection template on mobile would be an almost impossible — and nightmarish — task.
3. Not designed for images
A picture is, as they say, it is worth a thousand words. When it comes to inspections, being able to submit a picture can help resolve an issue quickly.
When there’s a picture in the inspection report, the inspector doesn’t have to spend so much time describing the problem in words (and it also saves the manager’s time from having to read it!)
However, spreadsheets are not designed to support images. They’re primarily designed for formulas and calculations. There isn’t a function to take a photo directly from the spreadsheet. Instead, you’d have to use the navigation menu to insert an image.
Once inserted, it’s very difficult to format the image within a cell. Often, the image can get lost if it is set to “float” above the text as it constantly shifts around whenever new data is added.
4. Unstable when the file gets big
Spreadsheets may be easy to set up at first, but as they grow bigger, it becomes unstable. Manually maintaining spreadsheets as they grow is tedious, which means it will take up a lot of time that could have been spent on things that matter.
Being unstable also makes it unreliable. If your spreadsheet is stored online so multiple team members can access it and fill it out from any location, the overload from multiple users at the same time could make the file unstable.
In the best-case scenario, team members lose a lot of time and have to resubmit an inspection form. In the worst-case scenario, the file crashes and deletes all past data, putting you at risk of non-compliance with the HSE.
5. Difficult to automate report creation
If you spend a lot of time each month maintaining spreadsheets, how much more time do you spend on translating spreadsheet data into inspection reports for higher management, stakeholders, or relevant external parties?
Feeding the reporting cycle on spreadsheets is laboriously long to do manually and not easy to automate either. You’d have to be a spreadsheet whiz with formulas and third-party integration tools to automate report creation from spreadsheets seamlessly.
Let’s not forget the fact that every time your inspection templates need updating, you’d also have to update all your formulas manually — making you less efficient and more likely to work overtime to complete other important tasks on your plate.
6. No audit trail
Not all spreadsheet software has an audit trail function that you can easily turn on or off, which means you don’t have historical data of who added, edited, or deleted data from a spreadsheet.
Not having an audit trail can be problematic for a few reasons:
- Creates a lack of accountability:
An employee could easily say that they did not write or delete something from an inspection report to avoid getting into perceived trouble. - Inaccurate data:
Without accountability, there is a higher potential for inaccurate data, leading to missed problems and other safety hazards.
7. It’s not easy to discuss items on a spreadsheet
When you leave a comment in a spreadsheet, it leaves a small marker in the cell to indicate that the cell has a comment. The comment thread pops up when you hover your cursor over this marker.
The problem is that this small marker is easy to miss on a desktop and even easier to miss on mobile.
While you can tag and assign a comment to someone’s email address to catch their attention, you’ll have to rely on them seeing the email notification, which isn’t guaranteed.
In other words, discussing an issue within an inspection report on spreadsheets is very difficult.
This hampers productivity because it slows down discussing issues, assigning corrective tasks, managing follow-up actions, and resolving issues.
8. Difficult to spot open issues and trends
Most spreadsheet software has search and sort functions, which can be useful in some situations. However, it’s difficult to use to spot open issues and trends.
Since inspection reports are subjective, you can’t guarantee that employees will always use the same word to write about a certain issue.
For example, you may want to run a search to see if there are any outstanding broken pipes. You type “broken pipe” into the search function, and a bunch of results appear. But what if an employee wrote, “pipe not working” instead? You’ll miss that issue.
Using the sort function could be a better option, but creating and maintaining columns with dropdown menus indicating “open” or “closed status” can take a significant amount of time.
Then, you’d have to add the sorting rules you seek — not to mention collating data from multiple sheets to keep track of everything in one place.
When spotting issues on spreadsheets is this difficult, spotting trends are even harder. Not spotting trends could be costly for your company.
For example, not seeing the trend that an employee is always slower than others to complete corrective tasks could lead to inefficiencies.
There’s a more efficient way to conduct inspections
Today, specialised inspection software for mobile platforms makes it much easier to conduct mobile inspections, attach photos for context, assign and close corrective tasks, create inspection reports, identify trends, and more.
With all these disadvantages of using spreadsheets for inspections, it’s not worth putting your most important assets at risk. Talk to sales to learn more about how we can help you conduct inspections and resolve issues more efficiently with Workflows.