Safety inspections allow employees to proactively spot and report any hazards or non-conformance that can lead to an incident.
Identifying these hazards early provides the opportunity to take due precaution as well as corrective or preventive actions.
How do you make sure you have an effective safety inspection system in your workplace? This article will provide you with the complete guideline from A to Z.
We will start with an overview of what safety inspections are, the laws regulating them, who are responsible for them, the different types of safety inspections, and how often they need to be conducted.
Then, we will dive into more detail with the best practices to design and conduct a comprehensive safety inspection as well as how to maximise the impact of safety inspections.
What is a safety inspection and what is its purpose?
A safety inspection is a documented checklist or procedure to identify potential hazards that can lead to incidents. Every type of safety inspection within a company should name who is responsible to complete the inspection and follow up on a submitted inspection report.
The purpose of safety inspections is to rectify hazards or non-conformance to ensure a safe working place that meets all legal health and safety requirements.
Safety inspections should not be confused with health and safety audits of a safety management system or third-party audits for specific accreditation. These audits are usually conducted by health and safety specialists from a third party, such as those from the Health and Safety Executive (HSE) or a local authority.
Third-party audits have a slightly different objective: to determine the quality and effectiveness of a company’s overall safety and health management system.
What are the laws regulating safety inspections in the UK?
The Management of Health and Safety at Work Regulations requires all UK employers to regularly monitor and review preventive and protective measures.
To ensure these measures are in place for full compliance with this legal requirement, companies need to conduct regular health and safety inspections.
It’s important to record all workplace safety inspections because they become evidence of legal compliance if a third-party needs to conduct an audit trail of your overall safety and health management system.
Who is responsible for safety inspections within an organisation?
Different parties within a company are responsible for various aspects of safety inspections. Here is an overview.
- Senior Management
Those in senior management positions, such as heads of departments, are responsible to:- Ensure procedures are in place to keep all employees, contractors, vendors, volunteers, clients, and customers safe within the company’s premises.
- Monitor reports from managers to make sure workplace safety inspections are conducted regularly for all activities and areas within their responsibility.
- Make sure that safety inspections are conducted to a standard that meets legal compliance.
- Assign safety inspections of different activities and areas to relevant managers under their department.
- Provide the necessary systems for documenting safety inspections and keeping its records.
- Managers:
Managers are responsible to:- Determine the frequency for every type of safety inspection assigned within their areas of responsibility.
- Assign safety inspections to competent employees under their responsibility.
- Train employees on how to properly conduct the safety inspections assigned to them.
- Train employees on how to take corrective action within their scope of skills and responsibility.
- Train employees on the chain of command of who to report to (and how to reach them) if they need help to urgently rectify a hazard or non-conformance.
- Coordinate any joint safety inspections within their area.
- Ensure submitted safety inspections meet all requirements.
- Follow up and investigate any incomplete safety inspections with the person responsible.
- Determine and delegate any preventive and corrective actions to mitigate the hazards identified in a safety inspection.
- Provide copies of the safety inspection report to any other managers for action whenever relevant.
- Follow up on all preventive and corrective actions.
- Provide senior management with relevant reports for monitoring.
- Employees:
Employees who have been assigned to conduct safety inspections are responsible to:- Conduct safety inspections according to the instructed frequency.
- Complete all items within the safety inspection checklist.
- Conduct the safety inspection with due diligence and care.
- Report any hazard or non-conformance that they see.
- Inform any nearby colleagues of any hazard or non-conformance spotted which could affect their safety so others can take precautions while waiting for preventive or corrective actions to be determined and implemented.
- Provide managers with any feedback on how to improve safety inspections.
- Be aware of any hazard trends so they know which areas or procedures require heightened awareness to spot hazards or precaution to stay safe.
What types of safety inspections are there?
The HSE has listed four types of inspections in the workplace. They are:
- Safety tours
This is a general inspection of a workplace area, such as a warehouse or retail outlet. Examples of checklist items for this type of safety inspection can include:
-Checking if employees are using safety equipment.
- Looking out for any dangerous behaviour.
- Monitoring safety systems.
Safety tours are usually conducted by management or senior management as part of their commitment to workplace safety. It also provides managers and senior managers with up-to-date knowledge of workplace day-to-day activities, as well as an opportunity for them to connect directly with employees to improve team relations.
- Safety sampling
The HSE defines safety sampling as the “systematic sampling of particular dangerous activities, processes or areas.”
An example of safety sampling is taking a sample of the chemicals or gasses that employees work with or are exposed to, then conducting a lab analysis on the samples.
In this example, the assessment is to ensure that the chemicals or gasses are within safe levels, or that the safety equipment employees use when exposed to these chemicals or gasses can adequately protect them from the levels detected.
- Safety surveys
Safety surveys are general inspections of specific dangerous activities, processes or areas. It is similar to a safety tour, but focuses on high-risk workplace environments or processes. Examples of typical areas to conduct safety surveys include a mining site, drilling rig, and a laboratory that screens for infectious diseases. - Incident inspections
Also known as emergency inspections, incident inspections are conducted after an incident caused a fatality, an injury, ill health, damage to property, or a near miss. These inspections are performed to identify the root cause so it can be mitigated to prevent similar incidents from happening again in the future.
How often do safety inspections need to be conducted?
Safety inspections can be categorised into three broad groups of frequency: routine inspections, planned inspections and emergency inspections.
- Routine inspections are conducted on a regular time basis, such as daily, weekly, or monthly. They can also be conducted based on a trigger, such as inspecting heavy machinery before starting a shift.
- Planned inspections include investigating specific matters that require a certain timeframe. These inspections don’t have a blanket routine frequency because it depends on the particular matter.
For example, a specific piece of equipment may need its parts tested for safety every six months. At the same time, the UK government recommends private-sector employers to offer their onsite workforce a minimum of two lateral flow tests for COVID-19 every week.
- Emergency or incident inspections, as mentioned in the previous section, are only required after an incident with no routine or planning involved. Emergency inspections can also apply to hazards before incidents happen. For example, inspecting nearby machinery to identify the source of a water puddle spotted on a factory floor.
Next, how do you determine the frequency of routine and planned inspections? Deciding its frequency largely depends on the level of risk involved in:
- The type of activity
Activities that are high-risk to employees when conducting them require more frequent safety inspections. One example of a high-risk activity is driving transportation trucks. The industry best practice is for drivers to conduct vehicle safety inspections before starting every shift.
Low-risk activities such as working in an office environment will still require safety inspections, such as inspecting the fire escape system, heating, or air-conditioning system. These, however, do not need to be conducted every day and can sufficiently be undertaken at least every six months. - The type of environment
An activity itself may not be high-risk, but it could be conducted in a high-risk environment. For example, the activity of serving food, by itself, is not considered a high-risk task.
However, if you are serving food to patients in a hospital with COVID-19 patients, you will need to take extra precautions. These precautions include the usual safety practices such as safety gear and regular sanitising of their hands. They also include routine and planned safety inspections such as monitoring the temperature of servers at least once a day and conducting regular COVID-19 tests.
Safety Inspection Framework
A safety inspection should include a quick overview of the area and an in-depth look at specific areas of concern. While different types of safety inspections will have different checklists, the general idea of any safety inspection is to methodically go through every item or part of the process that can cause an incident.
Here is a 10-step recommended framework that can help you put together comprehensive safety inspections in your workplace.
- Conduct a risk assessment. This will help you determine the risks in the workplace that require monitoring.
- List down the risks that require monitoring with safety inspections.
- Grade each risk using the risk analysis matrix. Refer to this risk management framework for further details on how to use a risk analysis matrix.
- Determine the frequency of each safety inspection according to its graded risk value.
- Determine the checklist of items to assess during the safety inspection and monitor all potential risks.
- Check industry best practices to guide you when drafting this checklist.
- Consult with specialists to ensure you don’t miss out on anything important.
- Using the final checklist, create the safety inspection forms for your employees to use.
- Train your employees on how to conduct and document each safety inspection they are responsible for.
- Review your safety inspection processes regularly and conduct surveys with your employees to receive any feedback that can contribute to improvements.
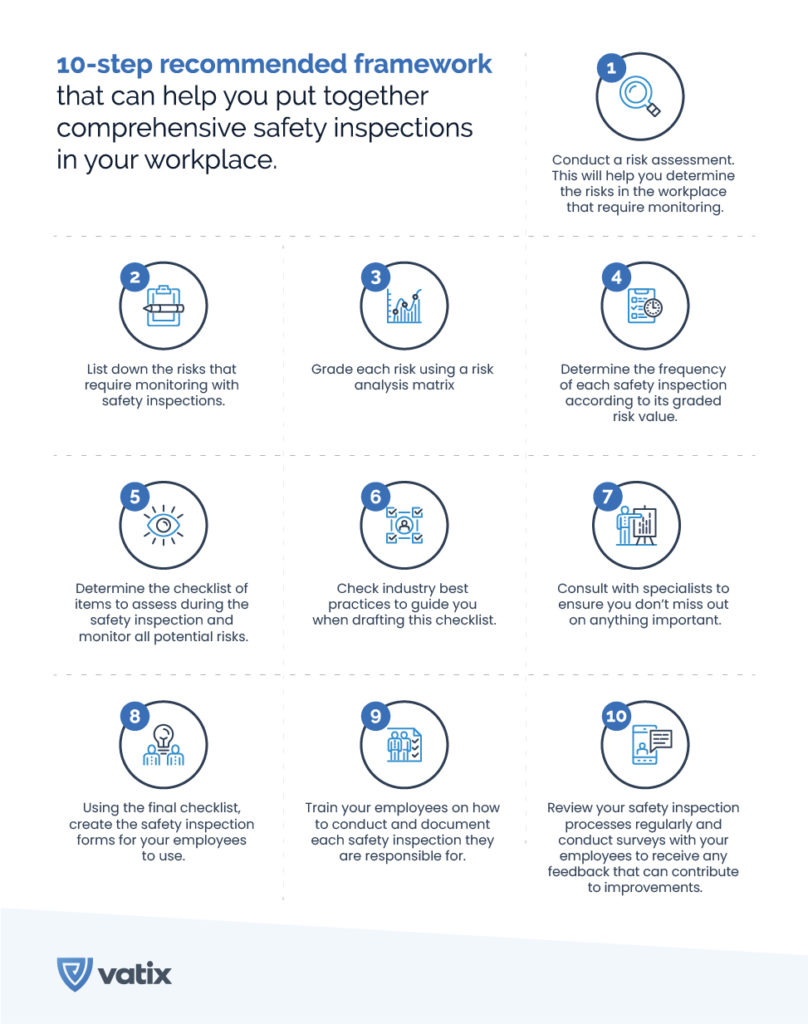
Best Practices to Conduct Safety Inspections
Now that you have determined the safety inspections your organisation needs, what’s the best way to conduct them? The HSE recommends these guidelines to conduct safety inspections efficiently and effectively.
- Plan a programme of inspections
Schedule all planned safety inspections so those responsible can block them off in their calendars or work schedule. You do not want safety inspections to be carried out in haste because the people responsible for them have too much on their plate. - Agree on the number of representatives or employees
Determine how many people need to be involved in any formal safety inspection, whether it’s a routine, planned, or incident inspection. Doing this in advance avoids confusion on who is responsible. - Coordinate inspections
If more than one representative or employee is involved with a safety inspection, coordinate the inspections to avoid unnecessary duplication or avoid missed safety inspections because - Inspect together
Managers can, from time to time, conduct safety inspections with appointed employees. It can help managers better understand the current situation of the workplace as well as help enhance the manager-employee relationship. - Consult specialists
Consult an internal or external safety officer or specialist advisers for technical advice on any issues that come up during inspections. - Break down tasks
It might not be possible to conduct all safety inspections in a single session for larger workplaces. Break down the tasks into practical chunks so your employees are not stretched out too thin when conducting safety inspections.
Best Practices to Document and Follow Up on Safety Inspections
What happens after a safety inspection has been completed? Here are some best practices on how to document and follow up on safety inspections.
Documenting:
- Review all safety inspections and ensure they are adequately completed.
- Ideally, you should be streamlining your safety inspection processes and documentation with digital solutions like Workflows. However, if you still use physical safety inspection forms, make sure you have a filing system that can help you find a specific inspection form should you need it at a later date.
- Ensure the files are accessible to those responsible. Keep in mind that your documentation acts as legal evidence of compliance.
Following Up:
- Flag safety inspections that are incomplete or have hazards or non-conformities that require preventive or corrective actions.
- Investigate the identified hazard or non-conformities onsite if required.
- Compile a list of necessary actions required to rectify the problem.
- Consult a specialist whenever necessary to determine the necessary actions.
- Ensure every action item is assigned to a person with a resolution date (i.e. deadline).
- Connect with the people you’ve assigned each action task, to ensure they have what they need to resolve the issue by the resolution date.
- Follow up on unresolved action items that have passed the deadline to determine the bottleneck, expedite the resolution, or find a more feasible solution to mitigate the risks.
The Advantages of Digitising Your Safety Inspection Processes
As you can see, there are so many moving parts within the entire safety inspection process. Managing all of this when you’re using a manual, pen-and-paper safety inspection system is time-consuming, laborious, and prone to human error.
Workflows, the inspection and task management system by Vatix, helps you streamline your safety inspection processes by doing all the heavy lifting to boost overall productivity.
Here are some key ways Workflows makes safety inspections easier, more effective, and less stressful.
- It makes it extremely easy for employees to complete safety inspections from any mobile device.
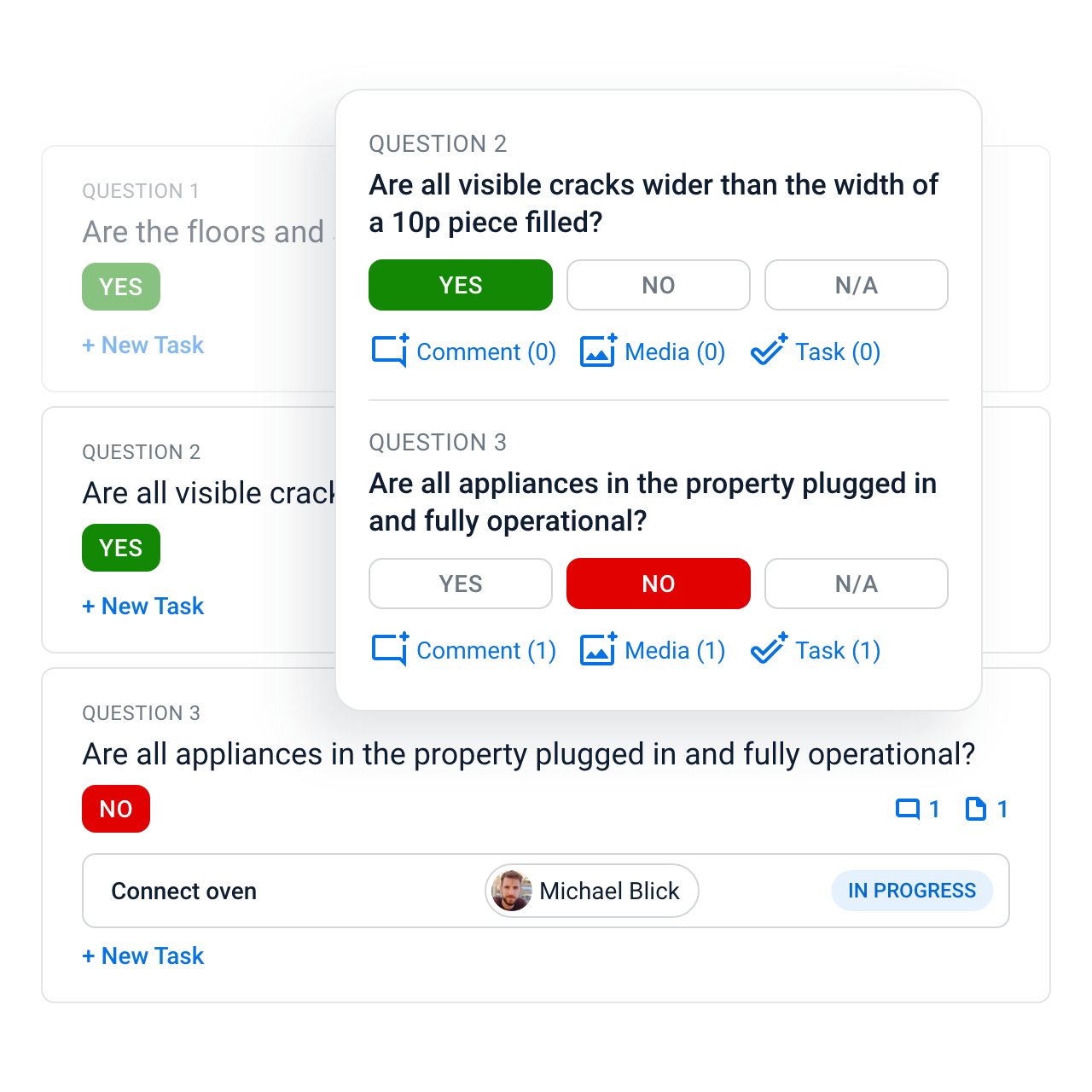
2. Managers can access all submitted inspection reports in real-time. They can overview all the flagged issues from submitted forms and the status of the associated follow-up tasks. This allows for faster resolution of issues and safer workplaces.
3. Integrated task management lets managers easily assign action items. The platform also keeps a digital trail of edits, follow-ups, actions complete, and discussions in one place.
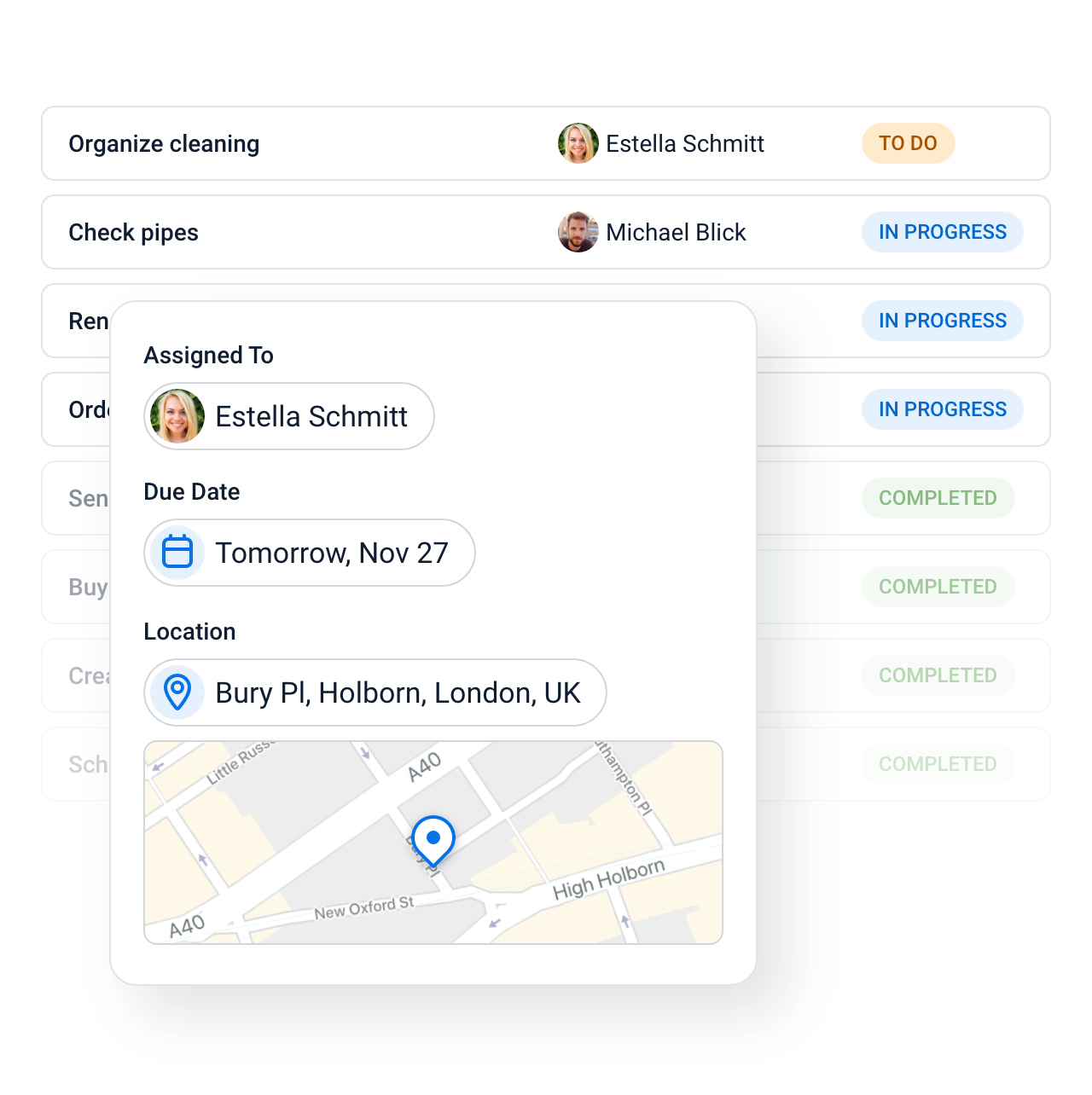
4. It gives you the flexibility to easily update inspection templates and implement them right away. This lets you quickly improve your safety procedures.
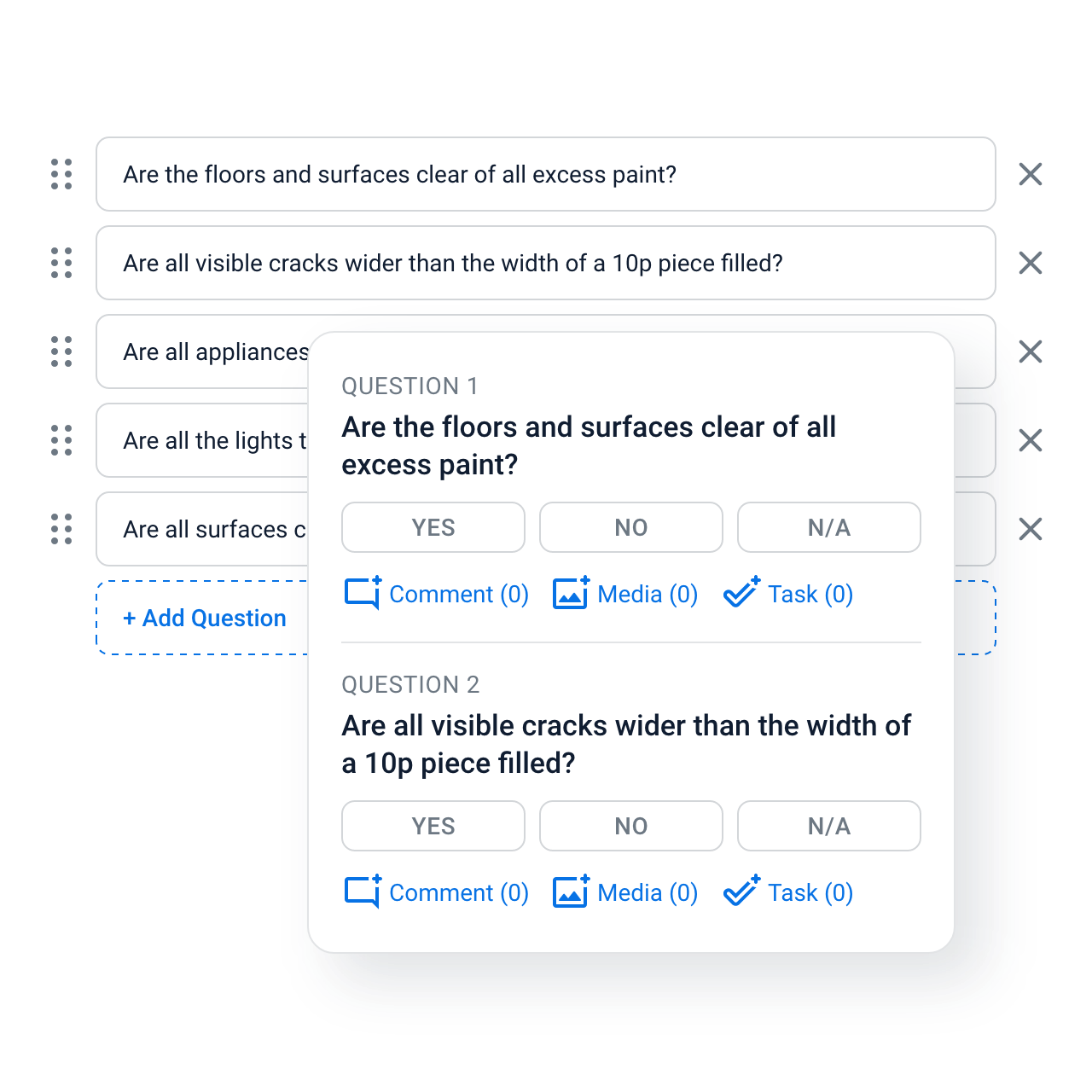
5. It’s no longer a time-consuming or laborious task to search for specific inspection reports or trends based on factors such as location, employee, or time frame.
6. It’s faster to create reports for senior management. You can also easily share inspection reports with any other relevant party.
Streamline Effective Safety Inspections in Your Workplace
If you’re ready to upgrade or switch to a digital safety inspection system, contact us to book a demo of Workflows and discover how it can help you to streamline your safety inspections once and for all.