Quality control inspections are an important process in every organisation. The objective of quality control inspections is to prevent any defects, identify areas of improvement, and ensure the product meets the company’s standards and any other legal regulations.
The importance of quality control inspections isn’t limited to products. It can also apply to a service that a company offers. While quality control inspections for services may be more subjective without a physical object to inspect, the process remains the same.
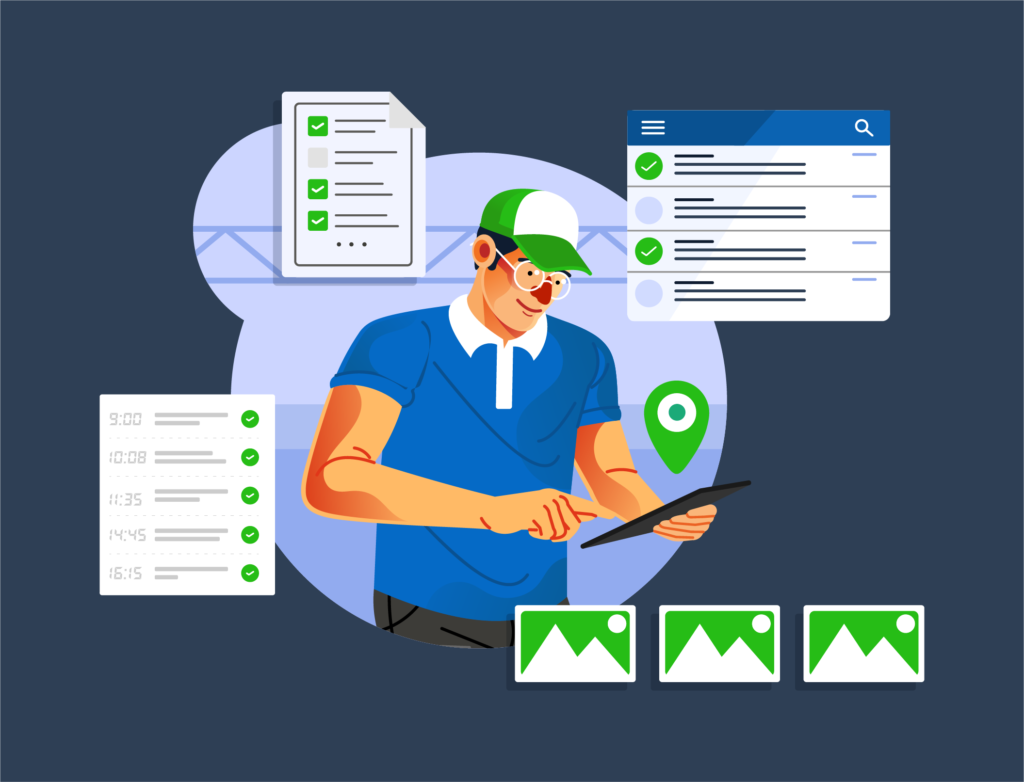
All quality control inspections, whether for a product or a service, will follow a checklist to meet the company’s standards and regulatory compliance. With many aspects of quality control to measure and assess, the process can be very tedious and stressful for employees.
This article will start with an overview of a Quality Management System (QMS), its four main processes, objectives, and the four types of QMS. Then, we’ll compare the pros and cons of three quality control methods needed to achieve QMS compliance so you’re informed to choose the best one that meets your organisation’s needs.
QMS: Overview and the 4 types of quality control inspections
A Quality Management System (QMS) is a set of processes to ensure the quality of goods and services meets the standards an organisation wants to achieve.
A QMS typically consists of a specific set of documents, processes, procedures, and responsibilities to achieve high quality. Quality control inspections comprise a major aspect of the processes within a QMS.
Typically, there are four types of quality control inspection processes:
- Control charts
Control charts are a method introduced by Dr Walter A. Shewhard. The method controls and monitors process variation and determines if the process is stable.
Example:
A quality control inspector weighs one random product sample in a manufacturing line every hour. He weighs the product and inputs the data into the control chart. The resulting data will show if the manufacturing line produces products consistently within the weight requirements. - Process control
Process control is used to ensure predictable quality and performance by maintaining and monitoring processes' assets. The objective is to minimise the variation of output from these processes.
Example:
A part of the process control activities of an oil and gas company could include regularly checking their machinery for variables such as:- Vibration
- Temperature
- Fluid levels
- Fluid flow
- Pressure
- Connectors
- Acceptance sampling
This type of quality control inspection involves taking a batch or sample of products or observing a service at a specified time. Then, measuring the sample against specified perimeters.
The quality of the sample is assumed to represent the quality of the entire product or service. The sampling results determine if the product or service meets the overall required standard and is accepted for production or execution.
Example:
At a food manufacturing site, random samples of potato chip bags waiting to be shipped are taken for acceptance sampling. Predetermined tests to measure the quality of this sample may include:- Checking the packaging for tears or holes
- Weighing the contents
- Taste testing
- Chemical testing for food safety
- Chemical testing for allergens
- Process protocol
Process protocol is different from process control because it focuses on the continual improvement of processes to improve quality. Using a mapping methodology, a process protocol creates evaluative indicators for each step to identify areas of improvement.
Example:
A factory supervisor maps out all the machinery inspections her team is responsible for. She looks at the past month’s control chart data to determine high variation points.
By comparing it with data from acceptance sampling, she can look for correlation patterns between machine variation and product quality variation. She then evaluates how to improve the inspection process and maintenance to reduce the machine output variation and improve product quality.
The benefits of an effective QMS
An effective QMS is an essential part of every organisation as it can help them to:
- Improve customer satisfaction
Organisations that consistently produce high-quality goods and services that customers have more satisfied and loyal customers. - Boost employee productivity
By having streamlined systems and processes to uphold quality, employees are less likely to be unproductive due to confusion or lack of direction. - Decrease wasted resources
When production lines produce more high-quality goods that meet the required standards, fewer resources will go to waste. - Minimise insurance premiums and legal fees
When an organisation maintains equipment and high-quality goods, it is considered lower risk for breakdowns and product recalls. Being a lower risk means better premiums and fewer legal fees. - Minimise product liability claims
A product liability claim is a claim for damages or injuries caused by unsafe or faulty products. High-quality control minimises the chances of design or manufacturing defects that can cause damage or injury. - Minimise product recalls
Product recalls is removing a line of products from the market that are defective or unsafe. Large recalls can a nightmare to manage as it doesn’t create an impact on profit, but there will also be remediation costs, legal expenses, rework processes, and repair any reputational damage.
- Protect their reputation
An organisation that can minimise product liability claims and product recalls through effective quality control improves its reputation in the market. A better reputation helps gain new customers and improve customer loyalty. - Save time and money in the long run
According to a report from Harvard Business School, one of the costliest product recalls in history was Johnson & Johnson, which had to recall 31 million bottles of Tylenol capsules. It cost the company $100 million in 1982, which is approximately equivalent to $260 million today after accounting for inflation.
Investing in systems and processes that create an effective QMS helps companies avoid problems such as product recall, reputational damage, and so on. This saves time and money for companies in the long run.
The 4 most internationally recognised types of QMS
Internationally recognised QMS standards offer companies credibility and give consumers confidence that a company’s goods and services are safe, reliable, and of good quality.
Having international standards also offers governments the ability to establish better regulations.
There are four popular QMS international standards that are sought after for their diligence and high-quality standards set by leading experts. Each type has different applications for different industries.
- ISO 9001
ISO 9001:2015 is a leading global standard that many businesses strive to achieve when designing their QMS.
The standard provides companies with certain performance indicators to achieve for quality, including documentation, resources, descriptions for sequences and actions, and a way to measure, monitor, analyse and evaluate quality control inspections.
- Six Sigma
The Six Sigma QMS focuses on process improvement and was introduced in 1986 by an American engineer working at Motorola. As a QMS that seeks to identify and remove the causes of defects, Six Sigma is ideal for the manufacturing industry or factories that churn high-volume production.
Since Six Sigma focuses on the process, it doesn’t focus much on ensuring the company meets the quality standards in the way ISO 9001 does.
However, it is an excellent complement to ISO 9001, thanks to its performance indicators covering various targets in the production line, such as reducing pollution or increasing customer satisfaction. - CMMI
Capability Maturity Model Integration is a QMS focused on improving processes, training, and appraisal programs as well as optimising developmental processes. It is well suited for companies wanting to decrease software, product, and service development risks.
CMMI defines maturity stages from Level 0 to Level 5, whereby higher levels mean a company is more capable of developing and producing quality products and services. - AS9100
Specifically designed for the aerospace industry and released in October 1999, the AS9100 QMS system has specific performance indicators for safe aerospace product manufacturing. Additional provisions to AS9100 include guidelines for military aviation.
The performance indicators of AS9100 include product safety, counterfeit parts prevention, greater emphasis on risk management, focus on eliminating recurring corrective actions, and processes to measure and monitor requirements conformance and delivery performance of aerospace products.
Comparison of quality control inspection methods to meet QMS standards
A common factor across the different types of internationally recognised QMS is the ability to measure, monitor, evaluate, analyse, and document key performance indicators. Inspection methods play a key role in compliance with international standards.
The three most common methods of conducting quality control inspections are manual, spreadsheets, and mobile software. Each has different pros and cons, as seen in the comparison chart below.
- Manual inspections
A paper-and-pen inspection system where employees go through printed copies of quality control checklists with a pen. - Spreadsheet inspection
A digital inspection system using spreadsheet software, like Excel. Employees go through quality control checklists on a spreadsheet using a computer or a mobile device. - Audits and inspections software
Software specifically developed for inspections, such as Workflows. Employees complete quality control checklists through a mobile app.
Comparison of the three most common quality control inspection methods:
BenefitsManual inspectionSpreadsheet inspectionMobile inspection softwareLow resistance✅✅❌Low to medium cost✅✅❌Little to no training✅✅❌Doesn’t need an internet connection✅❌❌Reduces paperwork❌✅✅Secure data with a low risk of data loss, data breach, or tampering❌✅✅Easy to access from anywhere❌✅✅Control accessibility with access and passwords❌✅✅Low risk of incomplete inspections❌❌✅Easy to attach photos❌❌✅Transparent audit trail❌❌✅Automated report creation❌❌✅Easy to format❌❌✅Mobile-friendly❌❌✅Real-time visibility❌❌✅
Choosing the right quality inspection system
Choosing the right quality inspection system is important because the consequences of poor quality control can jeopardise a company’s success.
Given the benefits of efficiency, productivity, and improved product quality with a mobile inspection software, this option is certainly worth the initial investments for companies that want a more streamlined and efficient way to achieve internationally recognised QMS standards.
To learn more about how you can make the transition to mobile inspection software as seamless and cost-efficient as possible, contact us.