
Maintaining equipment such as vehicles, tools, machinery, and digital devices is vital for profitability.
When companies stay on top of keeping these assets in optimal condition, they can minimise incidents that disrupt their operational processes, reduce the costs of replacing assets, and accelerate toward their business goals.
This article will explore what an asset maintenance system is, who needs it, the three different types of asset maintenance, and a few essential tips that can help organisations streamline asset maintenance.
What is an asset maintenance system, and why is it important?
An asset maintenance system keeps track of scheduled inspections and upkeep of assets, from equipment to properties.
The system gives visibility to the maintenance team of any reported issues so they can quickly correct them before the problems worsen.
The fundamental goal of an asset maintenance system is to ensure an organisation:
- Stays on track with scheduled maintenance
- Prevents warranties from becoming void due to missed maintenance
- Keeps assets in optimal condition
- Minimises downtime caused by faulty equipment
- Minimises delays or faults caused by inefficient or underperforming equipment
- Maximises the productivity and quality of work that these equipment produce
- Maximises the value of those assets
Who needs an asset maintenance system?
Any company with assets will need an asset maintenance system to achieve the critical goals of asset maintenance.
Asset-intensive industries that typically have many assets to upkeep will need a large-scale asset management system. For example:
- Construction companies with multiple moveable and fixed assets
- Factories with various equipment, tools, and accessories.
- Small businesses and companies involved in agriculture or fishing.
- Businesses in the oil & gas or power & energy sectors.
- Companies involved with water & wastewater management.
Companies outside these industries often still need asset maintenance systems to keep their equipment in tip-top condition, maximise productivity, and ensure smooth operations. Examples of these types of businesses include:
- Real estate, franchise owners, or warehouses that require regular property inspections.
- F&B, delivery, or car rental businesses that engage in fleet management for their daily operations.
- Data centre operators that rely on servers and equipment for their business.
Three types of asset maintenance
There are three types of asset maintenance that a company needs to track for all their assets:
1. Scheduled or Planned Maintenance
Scheduled maintenance is a routine check-up and maintenance of assets such as equipment, machinery, and vehicles.
The recommended maintenance schedule usually depends on the specific requirements of the asset according to the manufacturer.
For example, a vehicle may have the following recommended schedule for maintenance:
- Every 3,000 miles or 3 months:
- Fluid levels for power steering, wipers, and automatic transmission
- Air filter
- Engine oil
- Belts and hoses
- Headlights and inside car lights
- Fuel filter
- Tyre and treads
- Every 6,000 miles or 6 months:
- Cables
- Car battery health
- Chassis lubrication
- Change windshield wipers
- Every 12,000 miles or 12 months:
- Brake fluid and ABS system
- Coolant and transmission fluid levels
- Steering alignment
- Suspension
Staying on top of planned maintenance for each asset can help reduce maintenance expenses, prolong asset life, and prevent voiding manufacturer warranty on parts and equipment.
2. Corrective maintenance
Corrective maintenance is performed whenever a routine inspection identifies an issue. Routine inspections are performed more regularly than scheduled maintenance so they can identify any issue before the problem gets worse.
Routine inspections tend not to dive in as deep as scheduled maintenance. For example, a vehicle inspection report that drivers complete before starting their shift may look like this:
- Tyre pressure
- Tyres tread depth
- Lights
- Horn
- Windshield wipers
- Leaks
- Engine noises
- Steering
- Brakes
- Transmission
Although these regular inspections do not go as deep as scheduled maintenance, they ensure the asset is safe to operate before the worker uses it.
In addition to ensuring safety, routine inspections help identify any issues early so that corrective maintenance can be done as soon as possible without waiting for the next planned maintenance.
By conducting corrective maintenance as soon as any issues are identified, organisations can reduce downtime caused by faulty assets, enhance asset life, and improve quality and productivity.
3. Breakdown or Emergency Maintenance
As the name suggests, the last type of maintenance only happens when an asset has broken down. This emergency maintenance is typically costly as it often interrupts daily operations and negatively impacts business productivity.
Emergency maintenance may sometimes be needed when accidents or natural disasters that can’t be prevented happen.
However, many breakdowns or emergency maintenance can be prevented. Here are a few proactive steps that can help reduce disruptive accidents and breakdowns:
- Train your staff to conduct regular inspections for the assets they use.
- Implement a robust incident and near miss reporting system to reduce the chances of incidents that can harm employees or damage assets.
- Optimise workplace safety with an employee-led safety culture.
How to streamline and reduce the time spent on asset maintenance
By streamlining your asset maintenance, you will save time to boost productivity. You’ll also give your equipment the best chance to run efficiently for the most extended lifespan possible to increase profitability.
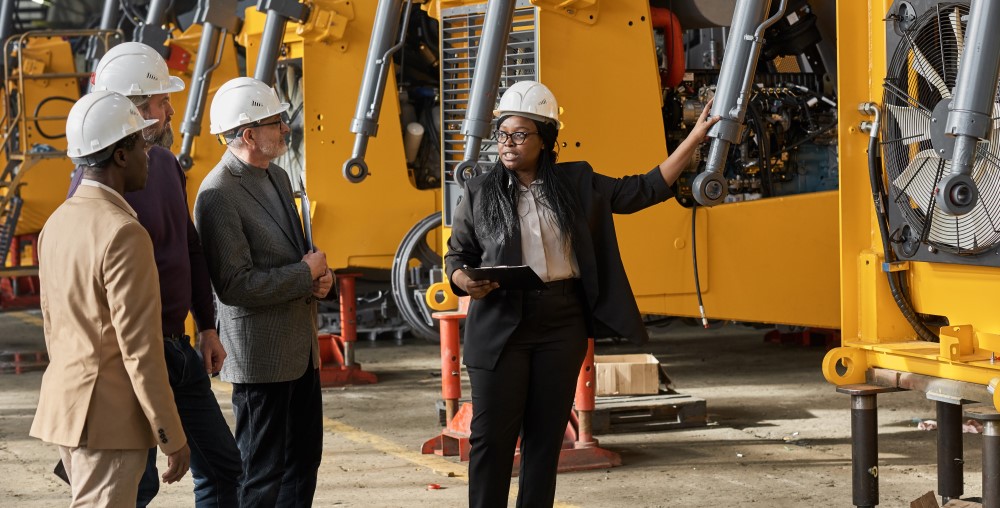
This section will explore some key strategies to streamline your asset maintenance processes.
- Keep a maintenance schedule and history
Since each type of asset will have its unique maintenance schedule, it can quickly become overwhelming for managers to keep track of planned maintenance without a proper system in place.
Implementing a digital inspections and task management software will help organisations stay on top of all their planned maintenance.
A digital system also allows employees to receive reminders or notifications on their mobile phones to conduct regular maintenance.
- Digitise your inspections
If you’re still using pen and paper to conduct your inspections, your asset maintenance process will be very laborious.
Manually conducting inspections, filing the paperwork, and finding the correct paperwork for updates and scheduled maintenance take a lot of time.
When you switch to a mobile inspection software, you instantly streamline your operation by eliminating the time and effort involved with manual inspection systems.
- Have all your processes in one place
By keeping all processes related to asset maintenance in one place, you don’t waste time looking for the necessary information.
For example, someone in charge of corrective maintenance would need access to the associated inspection report and maintenance records.
Keeping all these records in the same place can reduce the time it takes to collate the information that someone needs.
Essential Features of Asset Maintenance Software

If your key objective is to streamline your asset maintenance, here are five essential features you need in an asset maintenance software:
- Online access
Look for a solution that is hosted in the cloud and accessible online. Not only will this replace your filing cabinet system, but it also allows your employees to access the system from any mobile device, so they no longer need to carry around physical forms. - Digitise your inspection forms
By digitalising all your inspection forms into one platform, employees can easily select the inspection template they need to start an inspection.
Digital forms eliminate the hassle of carrying multiple inspection forms, which provides greater flexibility and mobility to conduct inspections quicker and more efficiently.
Look for software that allows you to easily create and edit inspection templates to meet your asset maintenance needs. A bonus is being able to add comments that allow you to have discussions within a report to resolve issues faster.
- Integrate with task management
Does the system allow you to assign a corrective task directly from an inspection report? If the system allows you to do this, then you can seamlessly assign and follow up on any corrective maintenance needed for every inspection report.
A digital filter or search function is an added bonus to help managers view and follow up on outstanding corrective actions that haven’t been implemented yet. - Upload photos and other relevant documents
One of the key advantages of a digital system is the ability to attach photos or other relevant documents to an inspection report.
Make sure the asset maintenance software you choose has these multimedia capabilities to boost the quality of your asset management.
For example, an employee inspecting a piece of equipment can take a photo of a broken part that needs replacing and attach it to the inspection report. The employee saves time by minimising describing the issue while ensuring clear communication and proper context. Thus, it is less likely to purchase the wrong part due to miscommunication.
- Real-time reporting and notification
Accessing information and receiving important notifications in real-time is another advantage of digital asset maintenance systems. Look for solutions that allow individual users to manage their notifications to alert them of issues that need their attention in real-time.
The Future of Asset Maintenance
If you’re looking to replace your filing cabinets with an asset maintenance system that can fit in the palm of your hand, then check out how Workflows can help you streamline the upkeep and maintenance of your valuable assets.
Workflows has been designed with all the essential features to plan, track and manage your asset maintenance from a single centralised platform. To learn more about how Workflows can adapt to your business needs, talk to sales.