Near misses are a goldmine of insight when it comes to improving workplace safety.
Yet, they often get overlooked. The reality is that near misses should be taken as seriously as actual accidents – because they highlight risks that could lead to real harm.
Let’s dive into what a near miss is, why reporting them is essential, the challenges employees face when reporting, and how to make near miss reporting a seamless part of your organisation’s safety culture.
What is a Near Miss?
According to the Health and Safety Executive (HSE), a near miss is "an event not causing harm, but has the potential to cause injury or ill health".
Under the Reporting of Injuries, Diseases and Dangerous Occurrences Regulations 2013 (RIDDOR), near misses are classified as "dangerous occurrences" – events that could have resulted in an accident but narrowly missed causing harm.
Legal Obligations for Reporting Near Misses
Even though near misses may not cause immediate harm, they must still be reported and addressed.
In the UK, organisations are legally required to report certain types of near misses under RIDDOR. These include incidents involving:
- Lifting equipment
- Pressure systems
- Overhead electric lines
- Electrical incidents causing explosion or fire
- Explosions
- Biological agents
- Radiation generators and radiography
- Breathing apparatus
- Diving operations
- Collapsed scaffolding
- Train collisions
- Wells
- Pipelines or pipeline works
Failing to report these near misses could lead to serious accidents in the future and potential legal repercussions for the organisation.
How Many Near Misses Go Unreported?
Despite the legal requirement, many near misses still go unreported. A survey by Accident Advice Helpline UK sheds light on this issue. When asked if they would report workplace hazards, a worrying 1 in 6 employees admitted they wouldn’t.
This lack of reporting means that serious risks are left unaddressed, increasing the chances of future accidents.
The Importance of Near Miss Reporting
Unreported near misses can lead to preventable workplace accidents. Consider these statistics from the HSE Summary for Great Britain 2021:
- Slips, trips, and falls account for 33% of non-fatal workplace injuries.
- 10% of non-fatal injuries are caused by being struck by a moving object.
- Falls from height cause 8% of non-fatal injuries.
A separate HSE report (2020/2021) identified the leading causes of fatal injuries:
- Falls from height – 35%
- Struck by a moving vehicle – 25%
- Struck by a moving object – 17%
- Trapped by something collapsing/overturning – 14%
- Contact with moving machinery – 14%
If near misses are ignored, these numbers will only continue to rise.
Why Don’t Employees Report Near Misses?
According to the same Accident Advice Helpline UK survey, employees gave the following reasons for not reporting hazards or near misses:
- 29% said they didn’t have the time.
- 24% felt the hazard didn’t affect them.
- 23% said it wasn’t their responsibility.
- 23% didn’t know who to report a hazard to.
- 13.2% worried about getting in trouble.
- 7.5% were told not to report the issue.
These findings highlight three key barriers to reporting:
- Employees don’t see near misses as serious.
- Employees fear retaliation or punishment.
- The reporting process is too complicated.
To improve near miss reporting, organisations need to make it a priority, a safe process, and an easy task.
How to Improve Near Miss Reporting in Your Organisation
1. Make Near Miss Reporting a Priority
Employees need to understand that near misses are not trivial matters. A strong safety culture starts with education and awareness.
Here’s how to make near miss training more effective:
- Explain the Heinrich Triangle, which states that for every 300 risky behaviours, 29 result in a minor incident or near miss, and 1 leads to a serious accident.
- Use real-life case studies to demonstrate the impact of hazard reporting.
- Document and communicate the reporting process clearly so employees know what to do and who to report to.
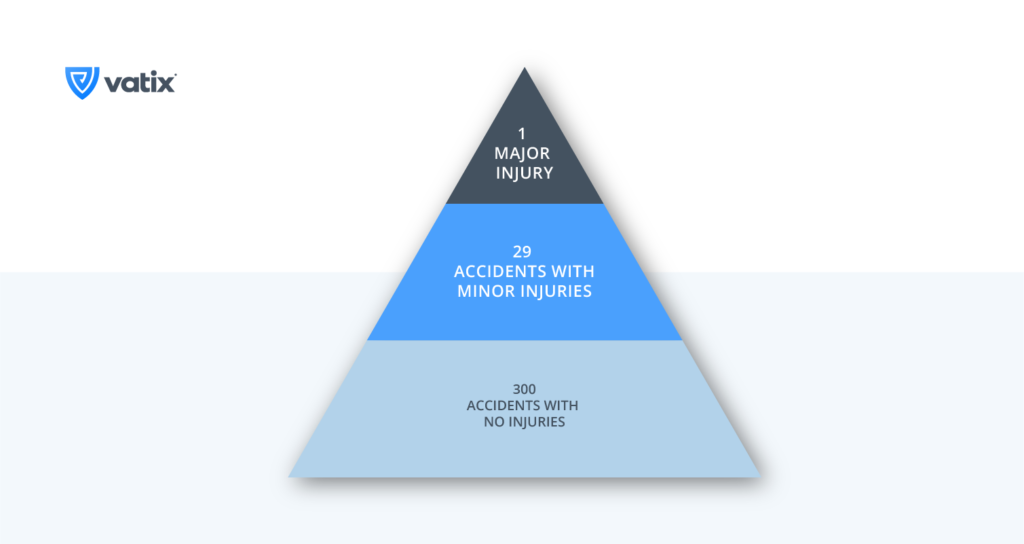
2. Make It Safe to Report Near Misses
A culture of fear discourages reporting. Employees need to feel confident that reporting a near miss won’t lead to punishment or blame.
Here’s how to encourage a reporting-friendly culture:
- Reinforce the company’s commitment to workplace safety.
- Train managers and supervisors to handle reports professionally and without blame.
- Foster an employee-led safety culture, where workers take ownership of reporting hazards and near misses.
3. Make Near Miss Reporting Easy
Traditional near miss reporting is time-consuming and bureaucratic. Paper forms, lengthy filing processes, and multiple approval layers create friction, discouraging employees from reporting.
Let’s be honest – if reporting a near miss is a hassle, employees might not bother.
What If Reporting a Near Miss Was as Easy as Updating Social Media?
Imagine if reporting a near miss was as easy as pulling out a mobile phone and writing a status update or uploading a photo on social media?
With a near miss reporting system like Incidents, this is possible.
Here’s a glimpse into how easy it is for your organisation to capture near miss data with our near miss reporting system:
- Select “Near Miss” from the dropdown menu and briefly describe the near miss.
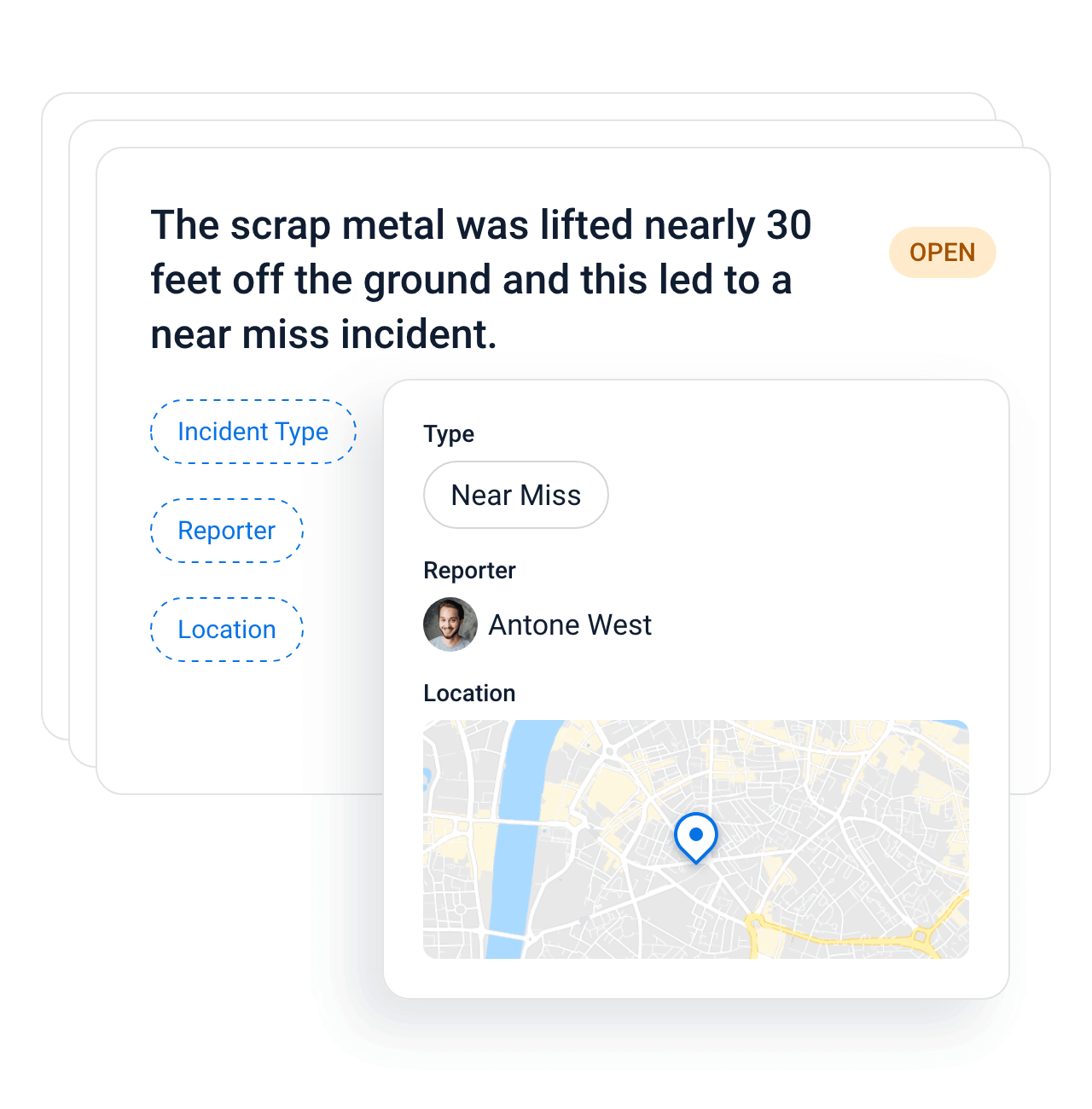
- GPS will automatically record the location.
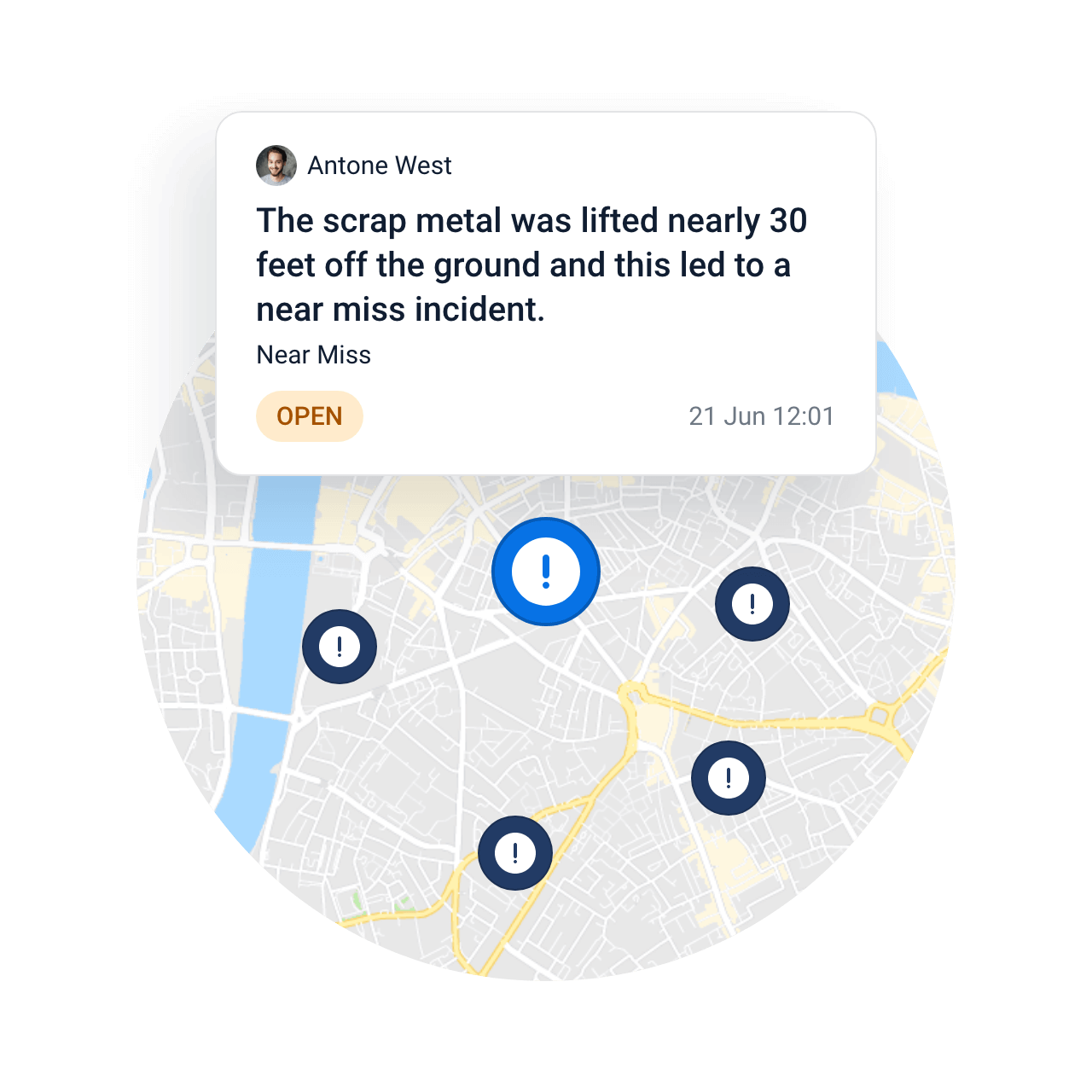
- Upload any relevant photos through the mobile phone’s camera and add any extra context by adding comments.
How to use near miss reporting software to prevent future events
With a near miss reporting app, employees can easily report near misses or hazards.
Here’s how Incidents makes it easy to follow up on near miss reports to prevent future events.
- Managers and supervisors can view on the platform all the reported near misses and hazards in real-time
- Anyone can alert other employees or supervisors by tagging them on the near miss records to implement corrective actions to prevent incidents swiftly.
- Threaded discussions keep relevant conversations in one place and ensure nothing slips through the cracks.
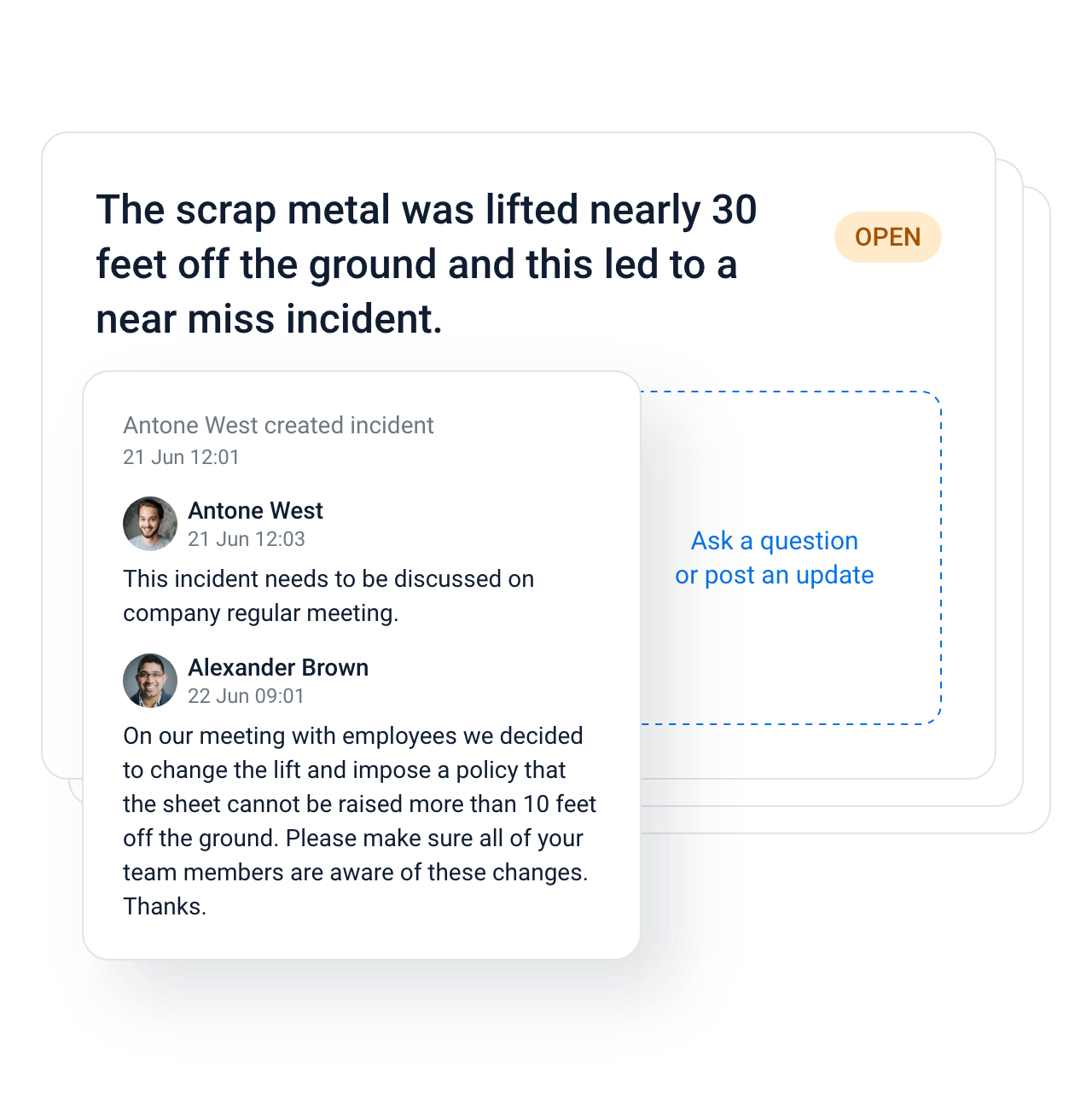
It’s time to take near miss reporting seriously
Removing the friction to report near misses and hazards is integral to building a first-class workplace safety culture.
If your organisation is still operating on physical forms and legacy systems to report near misses, it's time to switch to an incident reporting software. .
By making it a priority for employees to quickly, easily, and safely report near misses and hazards, you're also sending out the message that you care for their safety.
Showing this dedication to improving workplace safety can make employees feel more valued while reducing incidents to even minimise downtime and boost productivity.
Talk to our sales to learn more on how you can get started with Vatix’s near miss reporting software.