The construction industry has long had to contend with delays and challenges.
For those working in the industry, addressing these challenges begins with optimising construction workflows through innovative solutions like construction workflow technology.
In this article, we’ll delve into the root causes of construction delays and explore how embracing the latest construction technology can mitigate these issues.
Specifically, we’ll focus on how project management, mobile inspection, and incident reporting tools can improve productivity and minimise inefficiencies across six key construction workflows.
We’ll also explore the concept of the Golden Thread and its role in enhancing transparency and improving construction workflows.
Construction Technology: The Solution to the Productivity Crisis in Construction
The construction industry is a $12 trillion giant that has historically been slow to adopt digital innovation. However, with the increasing demand for efficiency, sustainability, and productivity, the industry has evolved over time, seeking new methods to enhance its processes.
Technological advancements have propelled construction forward, benefiting both the industry and society at large. Innovative technologies have equipped the construction sector with more effective ways to complete projects.
The State of the Construction Industry
Technology in the construction industry has lagged behind other sectors, contributing to significant productivity challenges.
McKinsey & Company highlights the low productivity gains of the construction industry compared to other sectors. While rising material costs are often blamed, a deeper issue lies in the gap between project complexity and the technology of building. As construction projects become more intricate, outdated workflows and tools fail to keep pace.
This is where construction workflow technology plays a transformative role, bridging the gap and addressing inefficiencies head-on. Modern technologies such as automated construction equipment, BIM, drones, and digital tools significantly enhance the efficiency and effectiveness of construction projects.
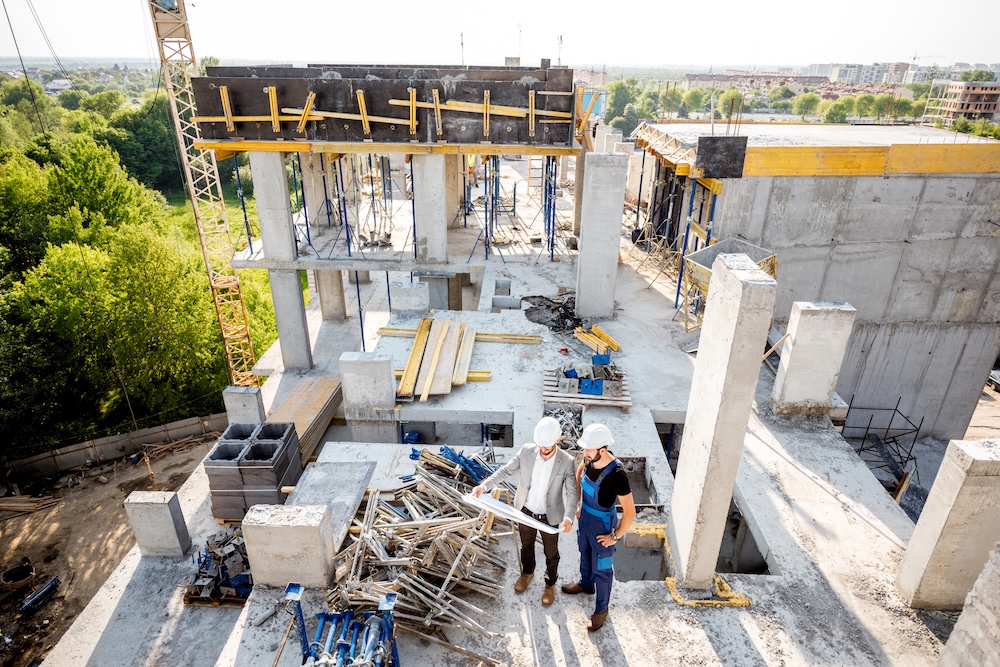
Challenges and Opportunities in Construction Technology
The construction industry faces several challenges that hinder productivity and efficiency. Outdated workflows, fragmented communication, and resistance to change are significant barriers.
However, these challenges also present opportunities for growth and improvement through the adoption of advanced technology.
One of the primary challenges is the reliance on traditional methods that are no longer sufficient for managing complex construction projects. These outdated workflows can lead to miscommunication, delays, and increased costs.
Additionally, the industry’s resistance to change and the slow adoption of new technologies further exacerbate these issues.
Despite these challenges, the opportunities for improvement are immense.
By embracing construction technologies such as project management platforms, mobile inspection software, and real-time data analytics, construction companies can streamline their processes, reduce errors, and improve overall project outcomes.
These technologies enable better communication, more accurate data management, and proactive resource allocation, ultimately leading to increased productivity and profitability.
Emerging Trends in Construction
On top of the gradual adoption of technology, the construction industry is also witnessing a wave of emerging trends that are transforming how projects are planned, executed, and managed. Among these trends, modular construction, virtual reality, augmented reality, artificial intelligence, and 3D printing stand out as game-changers.
Modular construction involves prefabricating building components off-site and assembling them on-site. This method reduces construction time, minimises waste, and lowers transportation and storage costs.
Virtual reality (VR) and augmented reality (AR) are revolutionising project planning and design by allowing construction professionals to visualise projects in immersive environments, identify potential issues early, and make informed decisions.
Artificial intelligence (AI) is enhancing project management by optimising resource allocation, predicting project timelines, and identifying potential risks.
AI-powered tools can analyse vast amounts of project data to provide actionable insights, improving efficiency and reducing delays.
3D printing is another innovative construction technology that enables the creation of complex building components with precision and speed, reducing material waste and labour costs.
These emerging trends are not only improving productivity but also enhancing the quality and sustainability of construction projects.
Sustainable Construction and Green Building
Sustainability is more than just an emerging trend; it is becoming a cornerstone of the construction industry, driven by the need to reduce environmental impact and comply with stricter regulations.
Green building practices focus on using sustainable materials, energy-efficient designs, and environmentally friendly construction methods.
Technological advancements are playing a crucial role in promoting sustainable construction. For instance, AI and data analytics can optimise energy consumption and resource allocation, ensuring that projects are both cost-effective and environmentally responsible.
Modular construction and 3D printing also contribute to sustainability by reducing waste and minimising the carbon footprint of construction sites.
Moreover, the integration of renewable energy sources, such as solar panels and wind turbines, into building designs is becoming more common. These sustainable practices not only benefit the environment but also enhance the long-term value and performance of buildings.
By adopting green building practices and leveraging advanced technology, the construction industry can achieve its sustainability goals while delivering high-quality, efficient, and cost-effective projects.
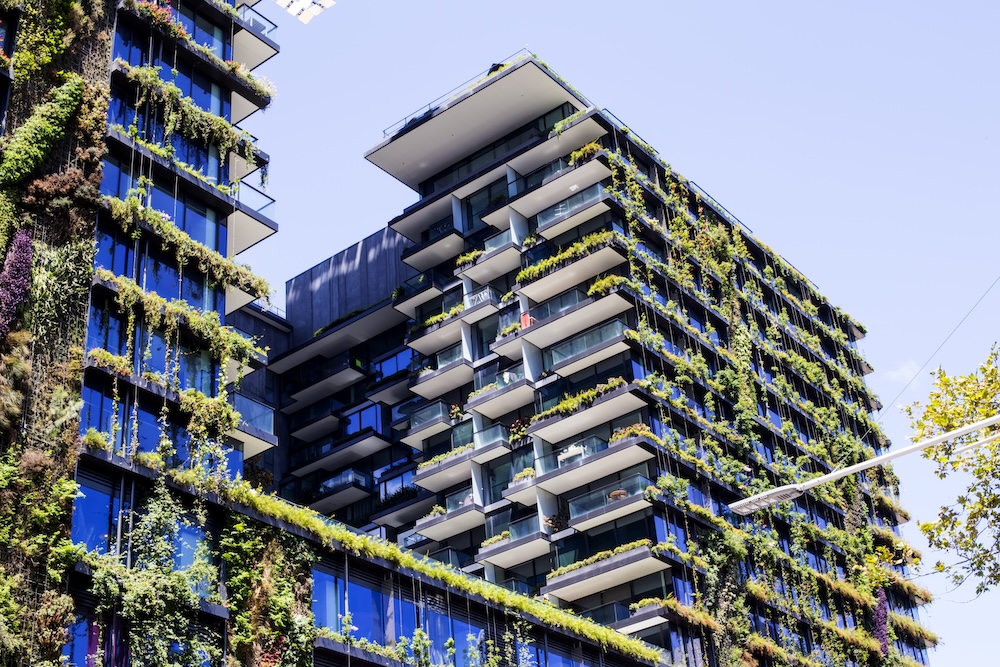
Understanding the Golden Thread
The Golden Thread is a concept emphasising the importance of maintaining an accurate, accessible, and transparent record of all building information throughout a project’s lifecycle.
Introduced in response to safety concerns in the construction industry, the Golden Thread ensures that stakeholders have access to reliable information for decision-making and compliance.
Construction workflow technology supports the Golden Thread by centralising project data, enabling real-time updates, and ensuring that all team members work with the most current and accurate information. This transparency and accountability are crucial for improving project outcomes and maintaining compliance with safety regulations.
Why Invest in Construction Workflow Technology for Construction Projects?
A 2018 report by PlanGrid and FMI Corporation found that poor communication and outdated processes result in significant inefficiencies:
- Construction workers lose nearly two days each week resolving preventable issues.
- Almost 50% of rework stems from miscommunication or inadequate project information.
- A mid-sized construction company loses an estimated £1.6 billion annually to inefficiencies.
By leveraging technology in the construction industry, companies can streamline communication, improve data management, and optimise workflows. Below, we explore how innovations in building construction can enhance six critical workflows in a construction project while aligning with the principles of the Golden Thread.
Now that we have a better understanding of the construction landscape in 2025, we can examine six methods you can implement to optimise your construction workflows.
Six Ways to Optimise Construction Workflows
#1: Optimising Preconstruction Workflow
Preconstruction involves design reviews, construction project planning, and cost estimations. Traditional methods rely on scattered communication across meetings and email chains, often leading to miscommunication and delays.
Construction workflow technology centralises these tasks, enabling all stakeholders to collaborate on a unified platform. Features like real-time design revisions, digital mockups, and centralised budgeting tools ensure smoother planning and more accurate estimations.
By maintaining a clear and accessible record of design iterations and approvals, this technology aligns with the principles of the Golden Thread.
Bottom Line: Centralised communication through project management tools improves planning accuracy and efficiency.
#2: Optimising Resource Management Workflow in Project Management
Market fluctuations and supply chain disruptions can wreak havoc on resource management. Construction technology equips project managers with tools to optimise resource allocation and adjust workflows in response to challenges.
By maintaining a database of alternate suppliers and enabling quick modifications to plans, project managers can minimise the impact of unexpected issues such as material shortages or labour constraints.
The Golden Thread ensures that all changes in resource allocation are documented and accessible, providing a transparent record for future reference.
Bottom Line: Proactive resource management powered by technology in the construction industry reduces delays and cost overruns.
#3: Optimising Warehousing Workflow
Warehousing is integral to keeping construction materials organised and ready for use on the construction site. The latest construction technology, like mobile inspection software, helps project managers efficiently track inventory, streamline delivery schedules, and conduct facility inspections.
Real-time inventory management and integrated auditing systems reduce the likelihood of delays caused by damaged supplies or stockouts.
For example, a platform like Workflows makes it easy for employees to complete audits and inspections using a mobile phone. Managers will then be alerted of any issues in real-time, so you assign corrective tasks and make sure they are followed through.
Bottom Line: Mobile inspection tools and inventory management systems ensure smooth warehousing operations and reduce waste.
#4: Optimising Safety Reporting Workflow
The construction industry faces high costs due to workplace injuries, reaching £0.82 billion in 2022/23 in the UK alone. Transitioning from pen-and-paper systems to digital construction workflow technology improves hazard reporting and safety management.
Utilising mobile technology to streamline hazard and incident reporting systems instead of traditional pen-and-paper reporting methods can help optimise safety reporting workflow by:
- Making it easy for workers to report safety issues on the spot
- Simplifying how workers report safety issues with the ability to take and upload photos of hazards into the mobile reporting system
- Giving safety managers a real-time view of hazards and incidents reported and preventing incidents caused by a delay in corrective actions
- Allowing safety managers to assign and follow up on corrective tasks for faster preventive and corrective action resolution
- Automating reports for safety managers to discover trends and key areas of risk that need to be addressed
Incident reporting software helps construction companies improve their safety reporting workflow by eliminating paper-and-pen safety reporting systems.
Bottom Line: Enhanced safety reporting minimises accidents and reduces time lost to avoidable incidents.
#5: Optimising Quality Control Workflow for Construction Professionals
Manual quality inspections are prone to errors, leading to costly rework. Mobile inspection software simplifies quality control processes by allowing real-time inspections, instant issue reporting, and corrective task management.
Using innovations in building construction, managers can track quality trends, ensure ISO compliance, and minimise rework caused by poor materials or workmanship.
Bottom Line: Streamlined quality control improves construction outcomes and reduces waste.
By using mobile inspection software such as Workflows to improve quality control, managers can minimise the issues that can potentially cause delays and inflated budgets.
#6: Optimising Communications and Data Management Workflow
Miscommunication is a major productivity killer in construction. Workers often waste hours searching for information or clarifying tasks. Construction technology tools like project management platforms centralise data and communication, making it accessible to all team members.
Threaded discussions and unified data storage ensure that workers can quickly find accurate information and resolve issues without delays.
The Golden Thread guarantees that this data remains accessible and transparent throughout the project’s lifecycle.
Bottom Line: Unified communication platforms prevent miscommunication and save valuable time.
Build Better Profits with Advanced Technology in Construction Workflow
By adopting construction workflow technology, companies can:
- Streamline processes to boost productivity
- Reduce errors caused by manual methods
- Improve quality and safety outcomes
- Achieve compliance with international standards
The technology of building is evolving, and embracing the latest construction technology is essential for staying competitive.
Leveraging the Golden Thread principles, construction companies can ensure transparency, accountability, and efficiency in every project phase.
For more information on how Vatix can help your construction company optimise workflows and improve efficiency, talk to our sales team today.