Warehouses are in a tough spot. They have to keep up with the demands of customers, clients, and eCommerce without any breaks. Many warehouses operate 24/7 to keep up with demand.
The challenges of multiple shifts and continuous workflow with little to no downtime can create pressure and the tendency to take risky shortcuts.
This is where it’s important to have a robust warehouse safety policy and system in place and an open corporate culture that upholds it.
In this article, we will explore why it’s important to make warehouse safety a priority, the most common risks warehouse employees face, and the steps you can take to make sure your warehouses uphold a first-class safety culture.
Why is it Important to Make Warehouse Safety a Priority?
Many work-related accidents happen within the storage and warehousing industry every year, with thousands of RIDDOR reportable incidents recorded annually.
Past HSE reports have also stated that close to 20% of warehouse accidents were classified as major injuries such as fractures and amputations.
With such high risks, warehouse safety needs to be prioritised in every company. A robust warehouse safety system should be able to:
- Identify the risks and hazards for each type of work and workspace.
- Equip employees with the knowledge and equipment to stay safe.
- Alert other team members that a co-worker needs help or is in distress.
- Report incidents, near misses, and hazards in real-time.
- Implement corrective and preventive actions quickly and efficiently.
The Most Common Types of Hazards in Warehouses
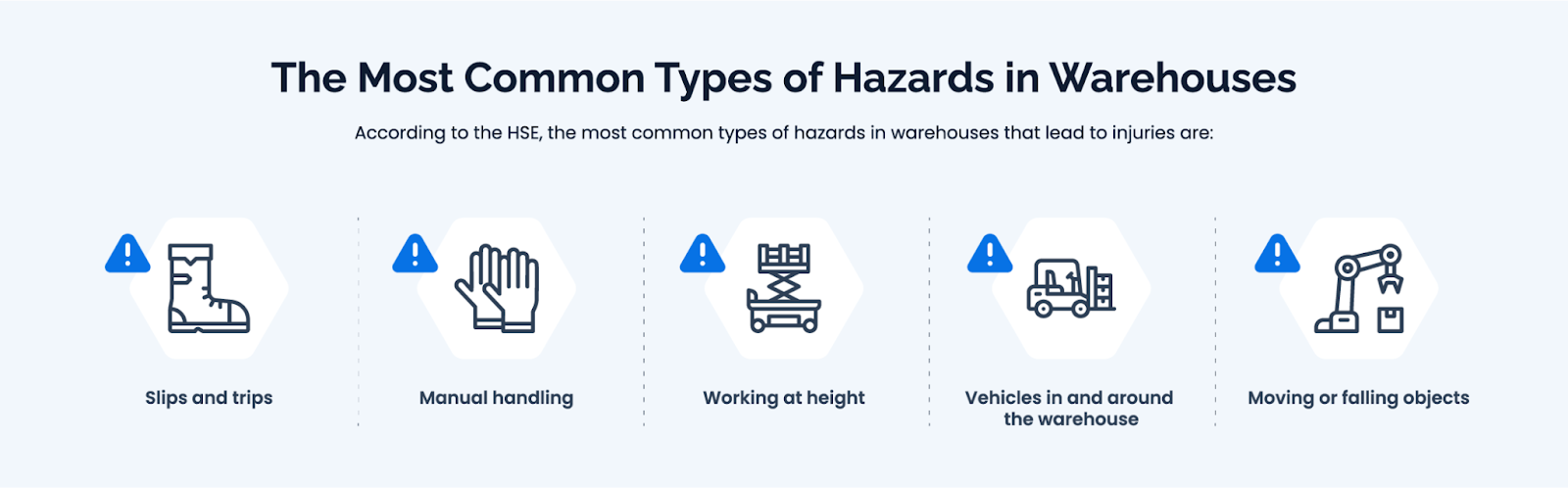
According to the HSE, the most common types of hazards in warehouses that lead to injuries are:
- Slips and trips
Warehouses are full of hazards that can lead to slips and trips. These include, but are not limited to, unpaved floors, low ceilings, sharp corners, exposed wires, and protruding objects or equipment. - Manual handling
Lifting and moving by hand can lead to many injuries, with bad backs reported as the most common injury. Other types of injuries that can occur as a result of manual handling can range from cuts, burns, and abrasions to more serious nerve damage or injuries to limbs. - Working at height
HSE defines working at height as any type of activity that:- Requires working on a ladder or a flat roof.
- Has the risk of falling through a fragile surface.
- Has the risk of falling into an opening on a floor or hole in the ground.
- Vehicles in and around the warehouse
Traffic control in warehouses can become a nightmare with multiple moving vehicles and foot traffic. The most common accidents involving vehicles include being hit by a vehicle or falling off a vehicle.
- Moving or falling objects
Warehouses tend to have multiple platforms for storage, making the risks associated with moving or falling objects very high. Awareness of the risk is important so that employees and visitors can take appropriate precautions.
Identifying the Risks Workers Face In The Warehouse
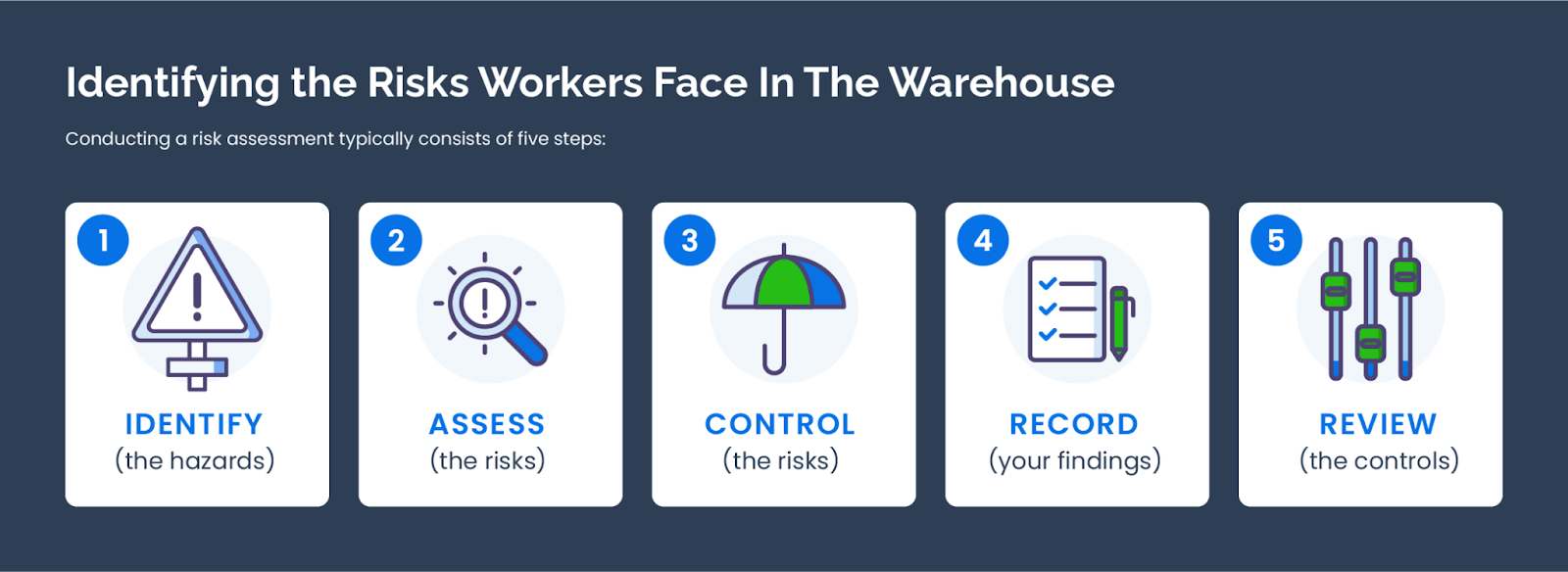
The hazards mentioned in the previous section are the most common hazards found in warehouses. It is not, however, a comprehensive list.
Thus, it is important to conduct regular risk assessments and dynamic risk assessments in warehouses' complex and high-risk environments.
Risk assessments are a systematic way to determine the dangers that pose a risk to your warehouse workers, managers, or visitors. Conducting a risk assessment typically consists of five steps:
- Identify (the hazards)
- Assess (the risks)
- Control (the risks)
- Record (your findings)
- Review (the controls)
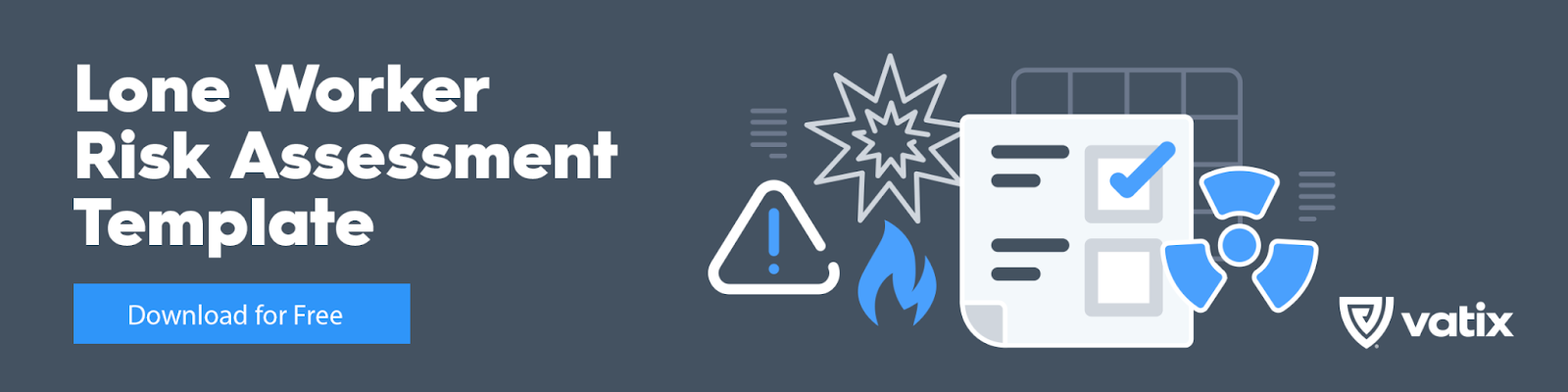
For more details on how to conduct each step, check out our article on the four types of risk management strategies for workplace health and safety.
How To Improve Safety For Your Workers
Once you have identified the risks for your workers according to the type of work they conduct in the warehouse and the risks associated with their workspace environment, the next step is to implement the procedures that will keep them safe. Here are a few key ones.
1. Safety equipment and procedures
Make sure you equip your warehouse managers and employees with the proper safety equipment according to the most common hazards or risks.
You should also have spare safety equipment on hand for visitors to use or to immediately replace any faulty safety equipment.
Some common safety equipment for each of the most common warehouse hazards identified earlier are as follows:
Safety equipment and procedures to prevent slips and trips:
- Slip-resistant footwear.
- Warning signs at high-risk areas.
- Procedures to reduce the slip and trip hazards, such as mopping wet surfaces.
Safety equipment and procedures to reduce injuries from working at height:
- Ensure safety equipment is suitable, stable and strong enough for the job, and is maintained and checked regularly.
- Ensure workers do not stand on FLT forks or forklifts.
- Avoid or minimise working from height whenever possible.
Safety equipment and procedures to reduce injuries from vehicle incidents:
- Enforce one-way traffic routes wherever possible to prevent accidents from oncoming or reversing vehicles.
- Install large traffic mirrors at intersections or heavy traffic areas.
- Create clear and designated pedestrian walkways or routes.
Safety equipment and procedures to reduce injuries from moving or falling objects:
- Safety helmets.
- Warning signs of high-risk areas.
- Ensure boxes on high platforms are securely tied down.
2. Training employees on preventing and responding to incidents
Employees must also be trained on how to take preventive actions like checking their surroundings, being aware of their own physical abilities, and how to properly use personal protective equipment.
You should also ensure that your employees are trained on how to respond to an incident. This can range from knowing what to do in case of fire to being trained in how to report incidents.
3. Having a real-time incident reporting system
Incident reporting is an official recording of the facts related to a hazard, incident, or near miss that happened on the worksite.
Incident reporting is an important aspect of workplace safety because it can help organisations to:
- Prevent more serious accidents
- Improve other health & safety measures in the workplace
- Save time and resources by minimising injuries and downtime
- Protect companies from penalties
- Boost overall employee well-being and productivity
In a warehouse environment, it is essential that employees are able to report hazards, incidents, or near misses as soon as they happen. Real-time incident reporting is critical in a warehouse environment.
Organisations that still rely on pen-and-paper incident reporting systems risk losing precious time to respond to incidents due to delays caused by submitting manual reports.
On the other hand, a mobile incident reporting software will allow employees to report a hazard, incident, or near-miss immediately on their mobile phones.
Once submitted, warehouse managers will receive instant notification of the incident, allowing them to respond immediately or warn other employees to avoid the hazards or danger zones.
4. Equipping high-risk workers with personal alarms
Personal alarms for high-risk workers, such as lone worker safety devices, are becoming an increasingly common safety necessity. Most of these devices include a Man Down alarm, also known as a fall detection alarm.
These alarms are activated by weight or impact, which can detect when a worker has fallen and send out an audible alarm to notify others.
If the worker is okay, they can cancel the alarm within a few seconds. This cancellation will notify the monitoring team that they are okay.
However, if the worker is injured and does not or isn’t able to cancel the alarm, the device will send an alert or call the appointed monitoring team to get help.
The Importance of Safety Inspections to Reduce Incidents & Downtime
Downtime in warehouses can have a significant impact on business. When the warehouse goes down for any reason, a company cannot fulfil its production schedules.
The results of this can be disastrous.
Regular inspections of facilities and equipment to ensure that they are in good working condition is the best way to keep warehouse operations running smoothly.
It is also important to conduct routine safety inspections to prevent incidents that can lead to a loss of manpower, damaged assets, or costly downtime issues.
Having a warehouse safety inspection checklist is necessary to keep incidents at bay.
A warehouse safety inspection checklist is a list of items that are routinely checked at regular intervals, such as before starting or ending a shift, daily, weekly, monthly, or quarterly.
They can be conducted by managers, supervisors, or employees according to their area of responsibility.
Here are a few examples of items that can typically go on a warehouse safety inspection list:
- Exits are clearly marked and have no obstructions
- Warehouse aisles are clear of obstructions, clutter, electrical cords, or other hazards that can cause slips, trips, and falls
- Pallet racks are not broken or damaged in any way
- Boxes/goods are correctly stacked with the heaviest items at the bottom
- Boxes/goods on shelves higher than 2 metres are secured
- Boxes/goods on shelves are not leaning with the possibility of falling
- Shelving is bolted properly to minimise the risk of falling over
- Loading bays or other areas where employees can fall 4 feet or more is chained or roped off securely
- Warehouse ventilation is in good working order
- Trees or vegetation do not create visual obstructions that could lead to traffic incidents
- Employees use proper lifting techniques
- Appropriate signals or warning signs are visible in high-risk areas
Choosing a Warehouse Safety System that Fits Your Needs
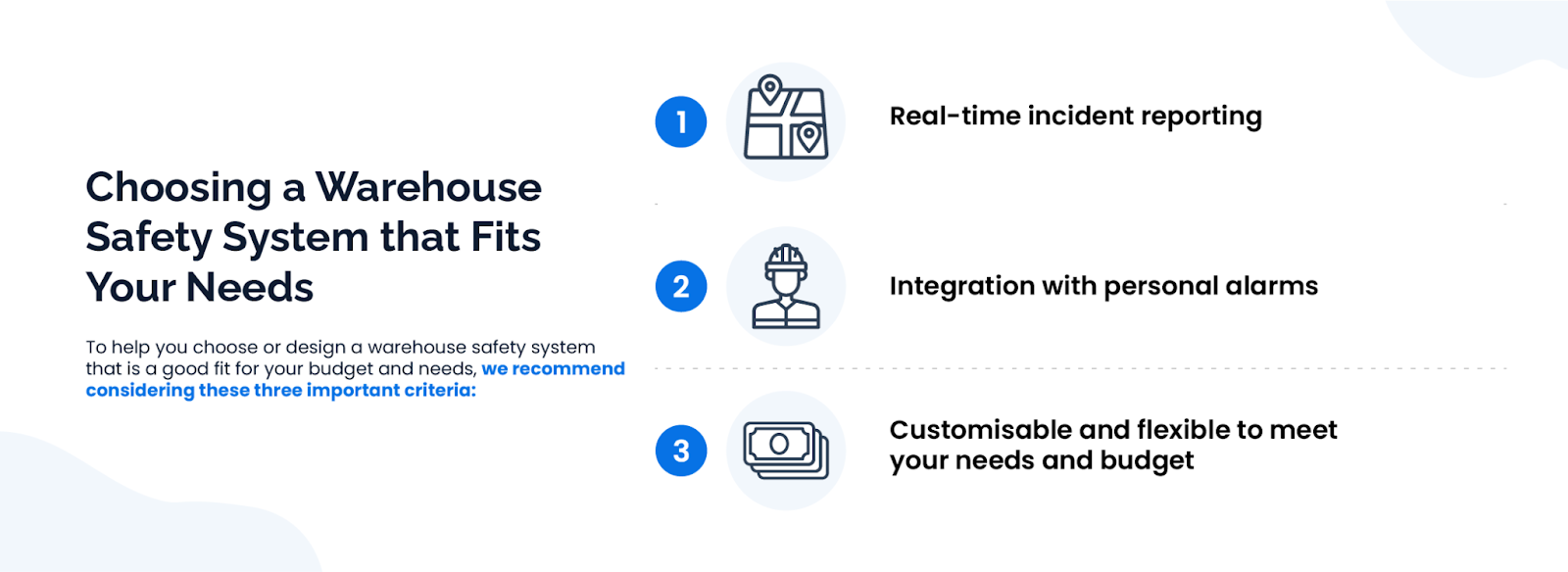
There are many different types of warehouse safety systems that vary in their level of safety and cost. When choosing a safety system that meets your budget, it’s important to not compromise on your safety needs. You also want to make sure you don’t overpay for features you don’t need.
To help you choose or design a warehouse safety system that is a good fit for your budget and needs, we recommend considering these three important criteria:
1. Real-time incident reporting
Since reporting hazards, incidents, or near misses as soon as they happen is critical, it’s important to make real-time incident reporting easy for your employees.
We designed our Incidents platform to be mobile-friendly, so it’s easy for employees to report any hazard, incident, or near miss on the spot.
With a visually intuitive interface, it’s also easy to add additional notes, photos, documents, geolocation, and other media for higher quality reporting with context.
2. Integration with personal alarms
Having personal alarm notifications and data integrated in real-time with your incident reporting on one safety platform allows an organisation to streamline how they manage warehouse safety.
We’ve enabled Protector to seamlessly integrate with our lone worker devices and app, so you don’t need to worry about managing third-party solutions on different platforms.
3. Customisable and flexible to meet your needs and budget
Customisable incident reporting templates allow you to meet your specific safety needs. You also want to keep in mind the ability to easily downsize or scale up according to your business needs, so look out for features like easy-to-transfer app licences and flexible user management of lone working safety devices.
Adopt a First-Class Warehouse Safety Culture
If you’re looking to improve your warehouse safety with a system that can make your warehouse day-to-day operations more efficient, productive, and proactive in safety, click here to talk to sales and discover how Protector can be customised to meet your needs and budget.