Is there a connection between workplace safety culture and company profits? In short — yes.
According to research by the Centre of Safety Research, Leiden University, fostering an effective safety culture is a worthwhile endeavour — both in terms of lives and in terms of profits.
This article will cover the key elements of an employee-led safety culture, how it’s different to a top-down safety culture approach, and how, when executed correctly, it can increase employee engagement, productivity, and profit for an organisation.
Finally, you’ll get examples of a real-life employee-led safety culture case study, plus practical steps to create an engaging workplace safety culture that benefits everyone.
Defining safety culture
Let’s first define what “safety culture” means. The research by Leiden University describes culture as “the ways of thinking, behaving, and believing that members of a social unit have in common.”
Safety culture in an organisation is thus the alignment of attitudes and behaviour to take safety seriously.
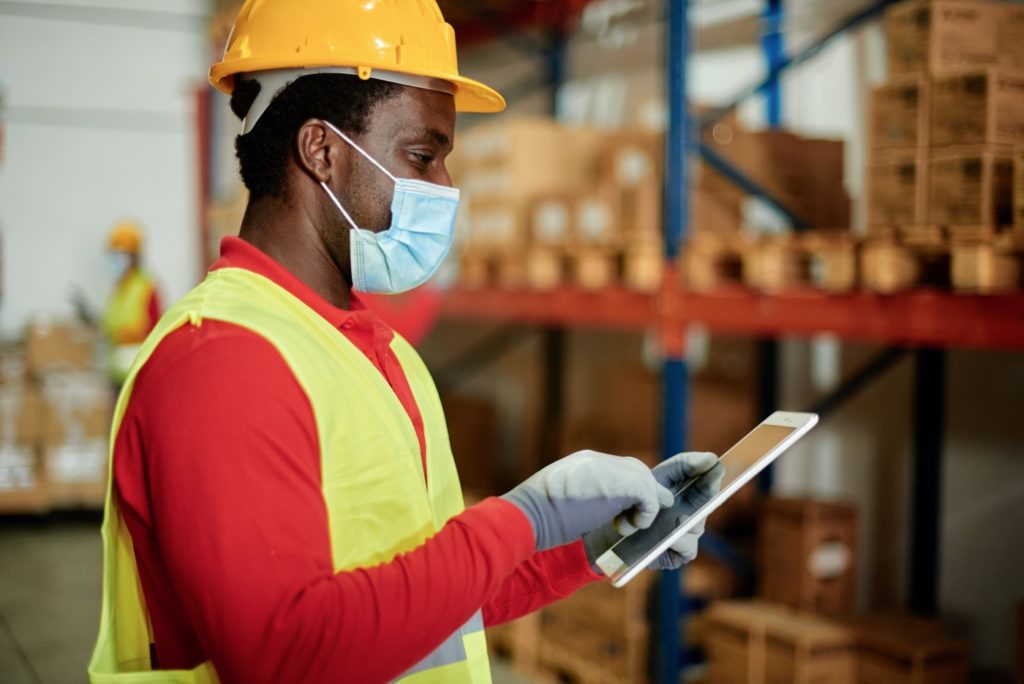
Organisations can build their safety cultures in one of two ways: employee-led or management-led.
What is an employee-led safety culture?
An employee-led safety culture is where employees:
- Take ownership of their safety
Organisations support employees with the training and resources they need to take ownership of their safety. - Recognise their role in safety
Employees recognise that they play a key role in improving workplace safety. This mindset translates to behaviours such as reporting hazards and incidents to management. - Get involved with risk assessments
The management consults employees for risk assessments and values their expertise and opinion to improve workplace safety. - Take responsibility for others
Employees also take responsibility for the safety of their team members.
What is a management-led safety culture?
On the other side of the coin is the management-led approach to safety.
A management-led safety culture is a top-down approach where management is mainly responsible for safety while employees take a more passive role.
Many might assume that by making the management responsible for safety, employees would become more productive because they don’t have additional safety responsibilities.
However, the opposite is true. When management leads a safety culture, employees are more likely to disengage from health and safety, leading to more accidents and lower productivity.
On the other hand, an employee-led safety culture acknowledges that frontline staff are better equipped to perceive risks and ideate solutions to prevent those risks from becoming a severe incident.
Top-down approach to safety — more harm than good?
In an evidence-based presentation by Mike Wilcock, Head of Operations South East for the Health and Safety Executive, it was reported that less than half of the organisations in the UK operate with an employee-led culture. A vast majority still use a management-led safety culture.
Mike Willcock’s presentation further reveals that over 60% of organisations in the UK operate with a management-led approach.
Meanwhile, according to HSE statistics, just under 700,000 non-fatal workplace injuries in the UK were reported in one year. That same year, the HSE issued £35.8 million in fines in the UK with an average cost of £110,000.
This evidence suggests that a management-led approach to safety doesn’t effectively engage employees to comply with safety processes, which can lead to more incidents. Furthermore, it may even nurture a culture of fear and blame around safety.
For example, many organisations are too focused on a ‘zero accidents’ goal due to the management-led safety culture.
Under the pressure of a “zero accidents” goal, health and safety professionals create complex risk assessments and policies. Frontline workers, sensing this pressure, are scared to report near-misses to already stressed health and safety managers.
Ultimately, instead of creating a healthy safety culture where everyone is engaged with safety processes and compliance, these organisations have created a culture of stress, fear, and blame around safety.
In this environment, employees are more likely to avoid reporting near misses or hazards out of the fear that they will be blamed or reprimanded. When near misses or hazards are unreported, it becomes an accident just waiting to happen.
Raising our safety standards to go beyond physical security
Another downside to the management-led, zero accident approach to safety is that it limits the definition of safety and silos it to purely injuries and fatalities.
This narrow definition doesn’t account for near-misses. It doesn’t account for a lone staff member feeling uncomfortable or intimidated by a member of the public.
Positive safety culture is more than physical security. It’s also about mental well-being and feeling safe in the workplace.
An employee-led safety culture will consult staff on how to make them feel safer. By raising the standards of how we define safety to go beyond physical security and include employees' mental and emotional wellbeing, employees are more likely to become engaged with safety processes and other aspects of their work.
As a result, organisations can avoid the hidden cost of disengagement. Numerous studies have shown employee disengagement is a prevalent issue that hurts an organisation's bottom line:
- Employee disengagement is a serious health and safety concern (Successful Culture International)
- Only a third of employees are positively engaged with their business (Gallup)
- Disengaged staff members are 73% more likely to leave their job (Guidespark) leading to a high turnover
- The costs of losing an employee can range from 1.5–2.0x the employee’s annual salary (Forbes)
- When employee engagement is increased by 10%, organisations can expect an annual increased profit yield of just under £2000 per staff member (Guidespark)
How can we raise our safety standards? A Case Study of Alcoa
In October 1987, Paul O’Neill, the newly appointed CEO of Alcoa, stood in front of a room full of investors in a Manhattan ballroom and said, “I’m here to talk about worker safety.”
The audience was baffled. Instead of talking about profit, taxes, or new markets, O’Neill outlined a vision of becoming the safest company in America.
Before the meeting was over, investors were running for a phone and ordering clients to sell their stock. They predicted this would be the end of Alcoa, but they were wrong.
Under O’Neill’s leadership, the annual net income increased five times, and its market capitalisation rose by $27 billion.
By identifying safety as a critical lever, O’Neill nurtured a culture of excellence that affected every aspect of working life. More importantly, O’Neill took on a unique, never-before-seen approach to employee safety:
- He encouraged employees to contact him with their ideas.
- He created a feedback loop for staff to suggest how to improve their safety culture.
- He listened to ideas staff had about improvements they could make across the business.
As the feedback loop strengthened, staff productivity and happiness rose, resulting in higher profits for Alcoa.
In short, O’Neill was a trailblazing pioneer of the employee-led safety culture and proved that focussing on safety creates results.
Leveraging the social exchange theory
When asked how he knew that his unique approach would be successful when almost every investor thought it was doomed to fail, Paul O’Neill said:
“I went to basics. Everyone deserves to leave work as safely as they arrive, right? You shouldn’t be scared that feeding your family will kill you.”
Whether he knew it or not, O’Neill had leveraged the social exchange theory that suggests every human interaction is based on an exchange.
The idea of employee engagement sits within this same theory.
If a company looks after their team by creating an environment that encourages best practices, employees will repay that investment by working harder and going the extra mile.
There is numerous pieces of evidence to back this theory. One of them is a study done with over 6,000 truck drivers, where researchers found:
- The safer employees felt, the more engaged they were with the organisation.
- Companies that made employees feel safer had less turnover than companies that don't highly prioritise the safety climate.
Considering that the average turnover cost is just over £30,000 per staff member, it's obvious that retaining staff saves you time and money.
People are more likely to stay with a company when people feel valued. One of the simplest and most cost-effective ways to do that is to ensure that they feel safe at work.
How to create an engaging workplace safety culture
The benefits of an employee-led safety culture are clear, but how do we implement it?
It begins by doing what Alcoa did: changing the narrative and moving away from a top-down, management-led safety approach.
There must be systems and processes in place that creates a feedback loop between frontline employees and higher management, which allows employees to take ownership of safety and feedback ideas to improve safety continuously.
Here are a few practical suggestions on how to implement an employee-led safety culture.
- Empower employees with the right tools
At Alcoa, staff could report their safety concerns through a direct line to the CEO. Many may find this extreme, complex, and difficult to keep track of.
Thankfully, technology makes it easier for you to create streamlined feedback loops without needing a direct line to the top.
Through mobile reporting tools, staff can easily report near-misses or hazards from their smartphone without the hassle of filling out and submitting forms to their manager.
When the process is simplified, more near misses and hazards will be reported. In turn, more corrective actions can be taken. When staff sees the positive outcomes in action, they will become more engaged.
Digital technology can also help you increase engagement by streamlining routine work processes. Mobile inspections similarly eliminate cumbersome pen-and-paper inspections that take a long time to process.
Instead, staff can digitally log the problems they find during inspections. Managers will be alerted as soon as it is logged and can quickly assign corrective actions.
This approach reduces the time it takes to solve a problem, but more importantly, it involves the employee with the solution and creates engagement.
- Create the right narrative
Investing in systems and equipment is essential, but it won’t work if your staff won’t cooperate. By leveraging the social exchange theory, you can create the right mindset that aligns employee attitudes with safety. When their attitudes are aligned, their behaviour will follow.
Ensure you communicate to staff why mobile reporting tools and mobile inspections are an investment for them. If you don’t communicate this, they won’t see why they should engage and may even grudgingly feel like this is just one more thing to do.
When staff understand how the technology you’ve invested in will keep them safer or make their work easier and more efficient, they will feel valued. Staff who feel valued will reciprocate through their work to give you value in return.
Shift to an Employee-Led Safety Culture
To sum up, an employee-led safety culture can positively impact every aspect of working life. Safety is not siloed; it is more than red tape.
The power of an employee-led safety culture is to create staff engagement that improves safety standards, increases health and wellbeing in the office, and creates a positive ripple effect on other areas of the business.
If you’re looking to improve the safety culture in your organisation, talk to us to learn more about how our solutions can help improve workplace safety and productivity in your organisation.