Root Cause Analysis (RCA) is not just a structured method of problem-solving; it's a vital component of organisational leadership. The goal of RCA is to fully understand what caused an issue, allowing for effective corrective actions.
One of the first steps in a successful RCA is identifying performance or opportunity gaps within an organisation. These gaps reflect ways in which an organisation falls short or fails to deliver on its capabilities. RCA helps in pinpointing these gaps, thereby allowing for more targeted solutions.
This article will take you through the benefits of RCA and the three basic types of root causes behind workplace incidents. We’ll then explore the two popular methodologies for RCA and how you can use the RCA methodology to identify them.
Finally, we’ll share tools and best practices to help you implement a robust RCA framework so you can develop a comprehensive problem-solving process for safety and risk management in your organisation.
Read on to discover how RCA can revolutionise your approach to problem-solving and risk management.
The benefits of Root Cause Analysis (RCA)
Without a structured RCA framework for resolving incidents, organisations risk implementing superficial quick fixes that may address some of the symptoms but not the core problems.
An effective RCA methodology helps an organisation's Health & Safety (H&S) team to identify the root causes of a reported incident in the workplace, which is essential to assign effective preventive or corrective actions. Implementing this framework have many benefits:
- Save time, money, and resources because they can identify and invest in the right preventive and corrective actions.
- Prevent the incident from recurring because they can correct the factors causing the issues.
- Prevent more damage or injury caused by a recurring incident.
- Prevent more downtime caused by a recurring incident.
- Boost productivity because they don’t have to revisit the same incident and spend extra time trying to solve the underlying issues.
The three basic types of root cause
There are three fundamental types of root causes:
- Environmental root cause
These are causes related to external factors such as moisture levels, weather, or geography. - Individual root cause
These are causes related to an individual’s behaviour, personal choices, ability, or circumstance. - Organisational root cause
These are causes involving internal organisational structure or processes.
The two popular RCA frameworks
A study by Baylor University Medical Center Proceedings identified two popular RCA frameworks. We will cover each one with an example.
#1: The "5 Whys" Method
This is perhaps the most popular RCA technique because of its simplicity. The method is to ask why something happened at least five times. Here’s an example of how it works.
Incident: A construction worker fell and broke his arm.
- “Ask Why” #1: Why did he fall?
Answer: He tripped on a wire - “Ask Why” #2: Why was the wire on the ground?
Answer: It was an extension wire needed to supply power to a tool on the other side. - “Ask Why” #3: Why was the wire pulled across a thoroughfare?
Answer: There was no power socket on the other side.
- “Ask Why” #4: Why is there only one power socket in that area?
Answer: There aren’t enough portable generators on the site. - “Ask Why” #5: Why aren’t enough portable generators on the site?
Answer: The application requesting the budget to rent a few more portable generators is pending approval.
Using this RCA technique, we’ve identified the actual root cause to be an organisational root cause. The solution for the organisation is to improve the process of approving budgets.
Speeding up the process of approving budgets doesn’t just help prevent future similar incidents. It may also bring the added benefit of improving productivity when construction workers can quickly get what they need to perform their tasks.
Without using this RCA technique, one could have soon concluded that it was solely an environmental or individual root cause. Any corrective actions in these areas are likely to be ineffective or short-term.
#2: Causal Tree
A causal tree is used to evaluate other possible causes that contributed to the incident. This can help organisations identify other possible preventive or corrective actions.
Here’s an example of how a causal tree could look like for the same incident example above:
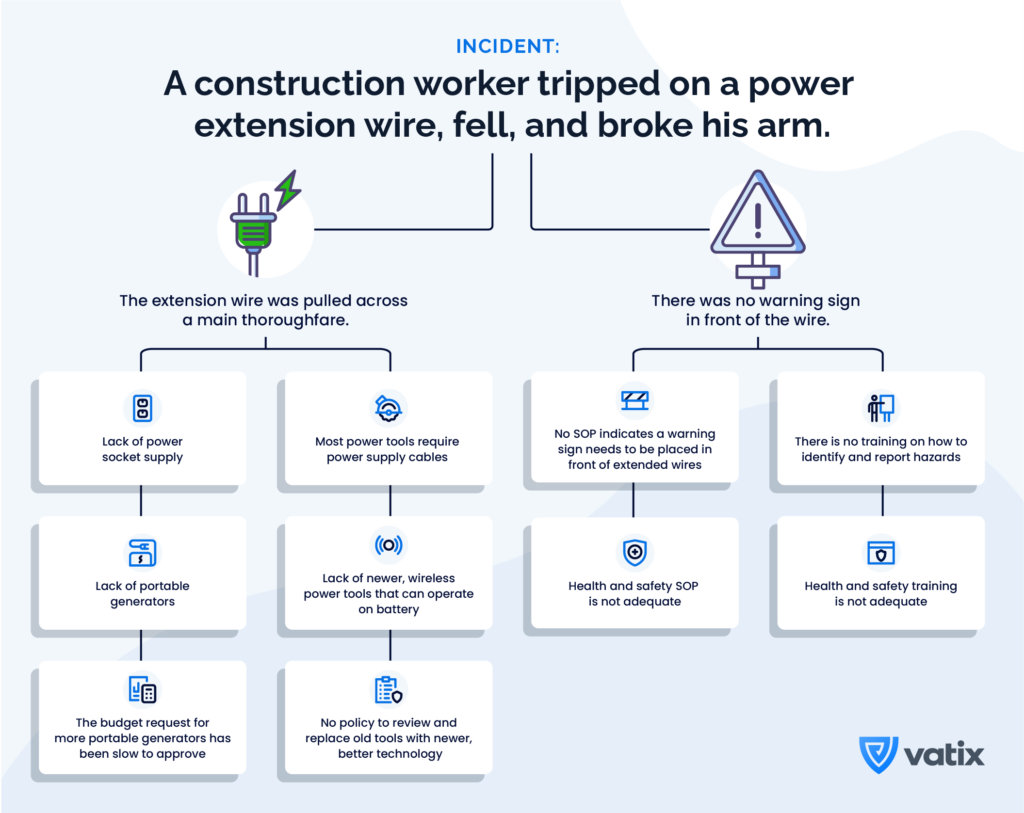
Organisations can explore other possible root causes that need addressing using a causal tree. This RCA methodology is beneficial for identifying root causes across environmental, individual, and organisational categories.
Another advantage of using the causal tree framework is that it allows organisations to implement short-term solutions to prevent incidents while they take more time to find answers to more prominent issues.
For example, the construction company can implement the short-term solution of placing warning signs in front of extended wires on the ground. Meanwhile, the organisation will look into solving the other root causes identified, such as improving the budget approval process and hazard reporting training.
Common Mistakes to Avoid in Root Cause Analysis
Root Cause Analysis (RCA) can be highly effective in addressing workplace safety issues when done correctly.
However, there are some common mistakes that organisations make when conducting RCA.
Mistake #1: Jumping to conclusions
One of the most common mistakes is jumping to conclusions without thoroughly examining the available information. This often leads to implementing quick fixes that do not address the root cause of the problem.
Tip: Ensure that you take the time to gather all relevant information and systematically work through the RCA process to identify the underlying cause.
Mistake #2: Focusing only on individual errors
Another mistake is solely blaming individuals for incidents without considering the broader organisational context. This can lead to a culture of blame and an unwillingness to report incidents in the future.
Tip: While it is essential to consider individual factors, also examine organisational root causes and environmental factors that may have contributed to the incident. This will help to create a more comprehensive understanding of the issue and lead to more effective solutions.
Mistake #3: Neglecting to involve the right people
One common mistake organisations make is neglecting to involve the right people in the RCA process. A successful RCA requires input from various stakeholders, including employees directly involved in the incident, supervisors, and management. Collaborative analysis helps in collecting a variety of viewpoints and promotes a sense of collective accountability for workplace safety.
Tip: Involving all pertinent stakeholders in the RCA process is crucial, as it aids in collecting a variety of viewpoints and promotes a sense of collective accountability for workplace safety.
Mistake #4: Inadequate documentation
Poor documentation of the RCA process and its outcomes can lead to a lack of accountability and hinder the implementation of corrective actions.
Tip: Document every step of the RCA process, including the incident description, investigation, root cause identification, and proposed corrective actions. This will help ensure that all stakeholders are aware of their responsibilities and can track the progress of the implemented solutions.
Mistake #5: Failing to follow up on corrective actions
Implementing corrective actions is only one part of the RCA process. Organisations sometimes fail to follow up on these actions, which can lead to a recurrence of the incident or issue.
Tip: Establish a system to monitor the progress of corrective actions and evaluate their effectiveness. Regularly review the implemented solutions and make any necessary adjustments to ensure that the root cause is fully addressed and the risk of recurrence is minimised.
How to implement a robust RCA framework
To enhance workplace safety, it is crucial to establish a strong RCA framework within your organisation.
These are the following steps to implement such a framework:
- Train the H&S team on how to use the different types of RCA frameworks.
- Make it easy for employees to report incidents and other events like near misses.
- Update the new employee training, health and safety training, and SOP guides on submitting incident reports and conducting RCA.
- Conduct regular health and safety training sessions.
- Creating an action plan: outline the steps to be taken, the stakeholders involved, and the timeline for implementation
The importance of high-quality incident and hazard reports
The effectiveness of any Root Cause Analysis (RCA) relies heavily on the input data's accuracy and quality. Therefore, it is imperative to have a reliable incident reporting system in place to ensure the provision of high-quality input data.
Here are the characteristics of a high-quality incident report:
- Records the incident's time, date, and location.
- Is honest, clear, and concise.
- Provides accurate information that doesn’t leave out important facts.
- Provide as much context as possible.
- It is written in a first-person, objective observation of what happened, not what they think might have happened.
To write an accurate incident report, employees should be encouraged to start writing the report as soon as possible.
Delaying writing the report can lead to inaccurate reports or reports without enough detail because the memory gets fuzzy. Whenever possible or relevant, employees should also attach photos for additional context.
To help you navigate the complexities of incident reporting, we strongly recommend downloading our free checklist and comprehensive guide.
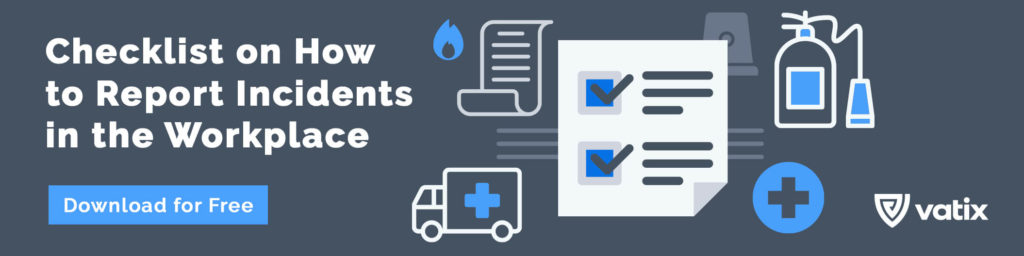
Best practices to improve incident reporting and RCA
One of the best practices to improve the quality of incident reports is digitalising the incident reporting process.
Here’s an example of how Vatix’s incident reporting systems can improve the quality of workplace incident reports and RCA.
- Higher quality incident reports
Our mobile platform makes it easy for employees to report an incident from anywhere without the friction of filling out and submitting a paper form.
Facilitating on-the-spot reporting for employees minimises the likelihood of postponing or neglecting to report incidents or other events.
Faster reporting of incidents also improves the quality of the report. Employees are more likely to record details with better descriptions and upload photos directly from their mobile devices, improving the data needed for an effective RCA.
- Customise incident types to an organisation’s specific needs
Our incident reporting software allows organisations to customise the types of incidents employees can report. These templates eliminate the need to print out, distribute, and file multiple forms.
- Easily customise the incident reporting template to capture relevant information.
With our incident reporting software, organisations can customise the incident reporting forms to ensure employees submit all required and relevant information.
- Real-time reporting and location tracking for faster response
Paper-based incident reporting causes a lot of delays and it can take hours before supervisors or managers can view the incident reports.
With real-time mobile incident reporting, employees can submit incidents on-the-spot and the H&S team will be alerted with a location so they can respond to the incident within minutes. In some cases, faster response time with location tagging can be the difference between life and death.
- Easy to get more context at a glance
Unlike manual paper-and-pen incident reporting forms, employees can easily add photographs to the incident report directly from their mobile. The incident reporting app also logs the location and provides visual maps for additional context at a glance.
Improve workplace health & safety processes
By combining mobile incident reporting with an effective RCA strategy, organisations can respond to incidents faster and more effectively to create a positive safety culture, leading to increased productivity and decreased risk of accidents and injuries.
Download our Root Cause Analysis Checklist to learn more about the key information you should be collecting in your incident reporting software to enhance workplace safety.
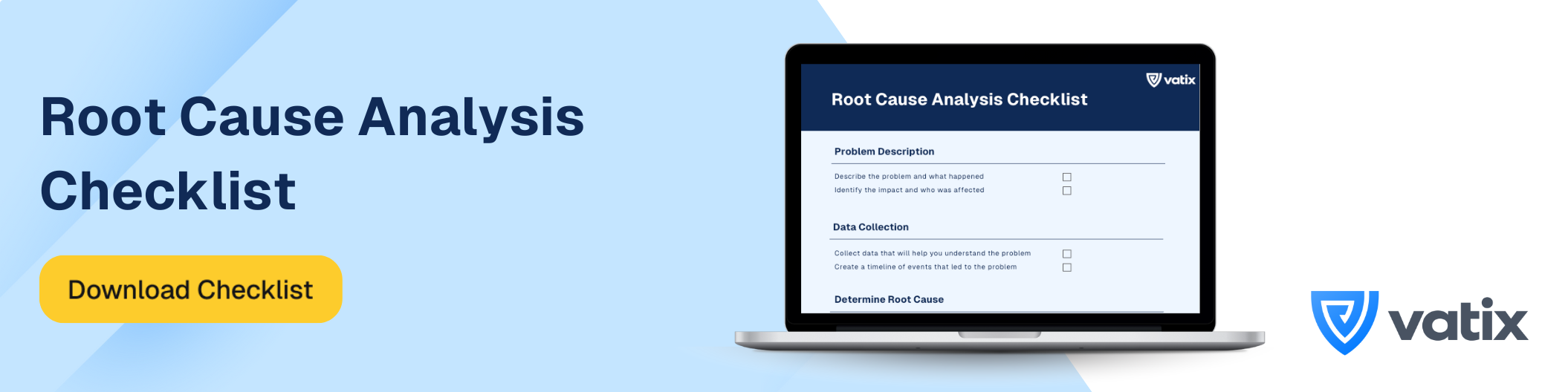