Labs are dynamic environments with a variety of hazards that demand constant vigilance and adherence to safety protocols.
Preventing lab incidents and accidents begins with understanding their root causes. By pinpointing these lab hazards and applying effective control measures, the risk of injury and contamination can be significantly reduced.
In this guide, we will highlight common laboratory hazards and provide risk control measures to ensure a safer working environment for everyone involved.
1. Chemical Hazards
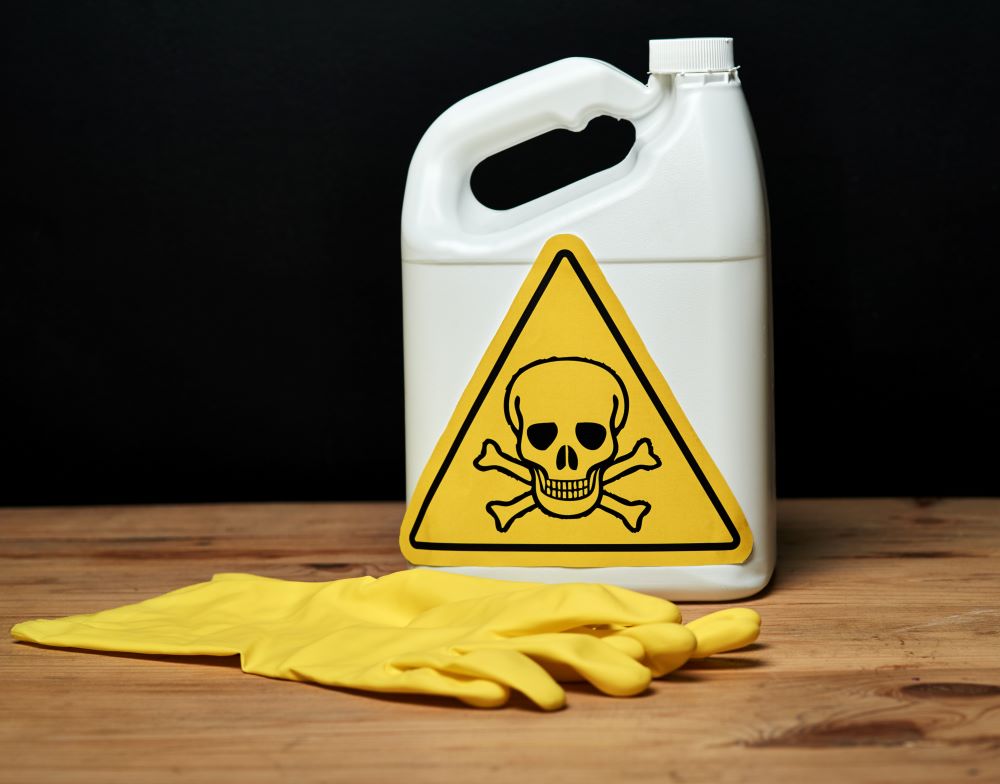
Chemical hazards are among the most common hazards in laboratory settings. They arise from exposure to hazardous substances that can pose health risks such as toxicity, corrosivity, flammability, and reactivity.
These hazards vary in severity. While some chemicals may cause mild irritation or temporary discomfort, others can lead to severe health issues, long-term damage, or even fatalities.
Chemical exposure can affect the body through inhalation, ingestion, skin contact, or injection, leading to acute or chronic health issues.
Maintaining a safe lab environment necessitates a clear understanding of chemical safety, including the proper handling and storage of laboratory chemicals.
Preventive Measures
- Proper Storage: Store dangerous chemicals in designated areas with appropriate containers and labels. Separate incompatible chemicals to avoid reactions.
- Safe Handling: Use personal protective equipment (PPE) like gloves and goggles, and follow standardised procedures to minimise spill risks.
- Training and Awareness: Regularly train lab personnel on chemical safety, spill response, and the use of Material Safety Data Sheets (SDS). Awareness of chemical hazards is key to prevention.
- Maintenance and Housekeeping: Keep work areas clean and organised. Regularly inspect containers and equipment for wear or damage, and promptly clean up small spills.
2. Fire Hazards
Fire hazards in laboratories are risks associated with the presence of flammable or combustible materials, ignition sources, and oxygen, which together can lead to fires or explosions.
Common fire hazards include flammable liquids, gases, combustible dust, and electrical equipment. Properly labelling and cataloguing these materials can help identify potential safety risks.
Fire hazards can result in devastating incidents such as laboratory fires, explosions, and severe burns to personnel. These events can cause extensive property damage, loss of experimental data, and, in severe cases, fatalities. Smoke inhalation and exposure to toxic fumes during a fire can also lead to respiratory issues and other health complications.
Preventive Measures
- Proper Storage: Storing flammable materials correctly is crucial in minimising fire hazards. Use approved safety containers, keep materials in designated flammable storage cabinets, and segregate flammables from incompatible substances to prevent dangerous reactions.
- Safe Handling Techniques: Avoid open flames, ensure proper ventilation, and always wear appropriate PPE such as flame-resistant lab coats, gloves, and safety goggles, to protect against accidental fires.
3. Inhalation of Toxic Gases
The inhalation of toxic gases poses severe health hazards in the laboratory environment.
It is a significant hazard in labs, as many experiments and procedures involve substances that can release harmful vapours.
These gases can include solvents, reagents, and byproducts of chemical reactions. Exposure to toxic gases can lead to immediate health effects such as dizziness, headaches, respiratory distress, and in severe cases, loss of consciousness or death. Chronic exposure can result in long-term health issues like respiratory diseases, neurological damage, and cancer.
Toxic gases can be released due to improper handling of chemicals, accidental spills, inadequate ventilation, or equipment malfunctions. Even small amounts of certain gases can be hazardous, making it crucial to recognise and control these risks.
Given the acute and chronic health effects these gases can cause, implementing appropriate control measures to protect lab workers is of utmost importance.
Preventive Measures
Implementing the following risk control measures can significantly reduce the risk of inhaling toxic gases in the laboratory:
- Proper Ventilation: Ensure that laboratories are equipped with adequate ventilation systems, such as fume hoods and exhaust fans, to remove toxic gases from the work area.
- Gas Detection Systems: Install gas detection systems to monitor the presence of toxic gases and provide early warnings to lab personnel.
- Use of PPE: Require lab workers to use appropriate PPE, such as respirators, masks, and protective clothing, to minimise exposure to harmful gases.
- Chemical Storage and Handling: Store chemicals that can release toxic gases in well-ventilated areas and handle them according to safety guidelines to prevent accidental releases.
4. Heat Burns
Heat burns are a common hazard in laboratories, where high temperatures are frequently used in various procedures and experiments.
Sources of heat burns include Bunsen burners, hot plates, autoclaves, and other heating equipment. Direct contact with hot surfaces, splashes of hot liquids, or exposure to open flames can cause serious injuries.
Heat burns can range from minor first-degree burns, which affect only the outer layer of the skin, to severe third-degree burns, which can damage deeper tissues.
These injuries can result in pain, blisters, and even permanent scarring. In severe cases, heat burns can lead to infections and other complications.
Preventive Measures
- Proper Training: Ensure that all lab personnel receive thorough training on the safe use of heat-generating equipment. This includes understanding the operating procedures and potential hazards associated with each piece of equipment.
- Protective Equipment: Always wear appropriate PPE, such as heat-resistant gloves, lab coats, and safety goggles, to protect against burns.
- Equipment Maintenance: Regularly inspect and maintain laboratory equipment to ensure it is in good working condition. Faulty equipment can increase the risk of accidents and burns.
- Clear Signage: Use clear signage to indicate areas where hot equipment is in use. This helps to remind lab personnel to exercise caution and avoid accidental contact.
5. Cuts and Lacerations from Glassware
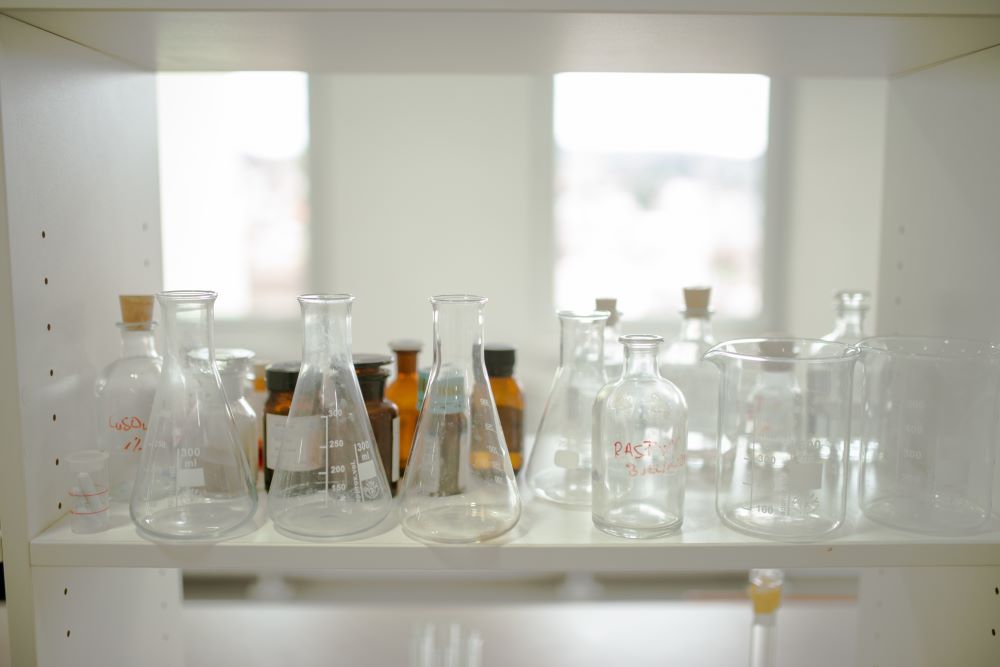
Glassware is essential in laboratories but poses risks of cuts and lacerations, particularly when it breaks.
These injuries can occur due to mishandling, accidental breakage, or improper cleaning techniques. Cuts can range from minor nicks to deep lacerations that require medical attention and can lead to infection or other complications.
Broken glass not only poses a direct risk of injury but can also contaminate experiments and create additional hazards if it comes into contact with hazardous chemicals.
Preventive Measures
- Proper Handling: Handle glassware with care, using both hands and ensuring a firm grip. Use appropriate lubrication when inserting or removing glass tubing.
- Protective Equipment: Wear cut-resistant gloves and safety goggles to protect against injuries.
- Inspection and Maintenance: Regularly check glassware for cracks or chips and discard damaged items. Use plastic or rubber-coated alternatives when possible.
- Safe Disposal: Dispose of broken glassware in designated sharps containers, not regular trash bins.
6. Eye Injuries
Eye injuries are a significant hazard in laboratories, where chemicals, biological materials, and physical debris can pose serious risks to vision.
Common causes of eye injuries include splashes of hazardous liquids, exposure to harmful vapours, flying particles from broken glass or equipment, and accidental contact with contaminated hands or equipment.
These injuries can lead to immediate pain, impaired vision, and long-term damage, potentially resulting in permanent vision loss.
Preventive Measures
- Use PPE: Wear safety goggles or face shields when handling chemicals to protect against splashes.
- Proper Handling: Use careful techniques and tools designed to minimise spills and splashes when working with chemicals.
- Engineering Controls: Utilise fume hoods and splash guards to provide barriers between chemicals and personnel.
7. Electrical Hazards
Electrical hazards in laboratories pose significant risks due to the reliance on various electrically powered equipment and instruments.
These hazards can arise from faulty wiring, damaged equipment, improper use of electrical devices, and exposure to water or other conductive materials. Electrical hazards can lead to shocks, burns, fires, and even electrocution.
Preventing these hazards requires regular risk assessments and proper maintenance of electrical equipment.
Preventive Measures
- Risk Assessments: Regularly inspect wiring, equipment, and lab setups to identify potential hazards.
- Equipment Maintenance: Regularly check and replace damaged cords, plugs, and devices to prevent accidents.
- Proper Usage: Train personnel in the correct use of electrical equipment. Avoid overloading circuits and using extension cords as permanent solutions.
- Ground Fault Circuit Interrupters (GFCIs): Install GFCIs in areas near water sources to prevent electrical shocks by cutting off power during ground faults.
8. Slips, Trips, and Falls
Slips, trips, and falls are frequent physical hazards in laboratories, often resulting from wet floors, uneven surfaces, cluttered workspaces, or poorly maintained walkways.
These incidents can cause injuries ranging from minor bruises and sprains to serious fractures or head injuries, impacting the safety and productivity of laboratory personnel.
These risks can be controlled through preventive measures and proper housekeeping.
Preventive Measures
- Housekeeping: Keep workspaces clean and organised. Promptly clean and dry floors, and address spills immediately. Remove clutter from walkways.
- Lighting: Ensure all areas are well-lit to help personnel see potential hazards clearly.
- Non-Slip Flooring: Install non-slip mats in wet-prone areas to reduce slipping risks.
- Signage: Use clear signs to indicate wet floors, uneven surfaces, or other hazards.
9. Biological Hazards
Biological hazards in laboratories arise from exposure to infectious agents such as bacteria, viruses, fungi, and other microorganisms.
These hazards can pose significant health risks, leading to infections, allergic reactions, or toxic effects. Laboratory personnel working with biological materials, including clinical samples, cultures, and genetically modified organisms, are particularly at risk.
Protecting laboratory workers requires strict adherence to biosafety guidelines and preventive measures.
Preventive Measures
- Training: Regularly train all personnel in biosafety practices and the risks associated with biological hazards.
- Containment: Use designated containment areas, like biosafety cabinets, to prevent the spread of infectious materials.
- Disinfection: Regularly disinfect work surfaces and equipment to reduce contamination risks.
10. Ergonomic Hazards
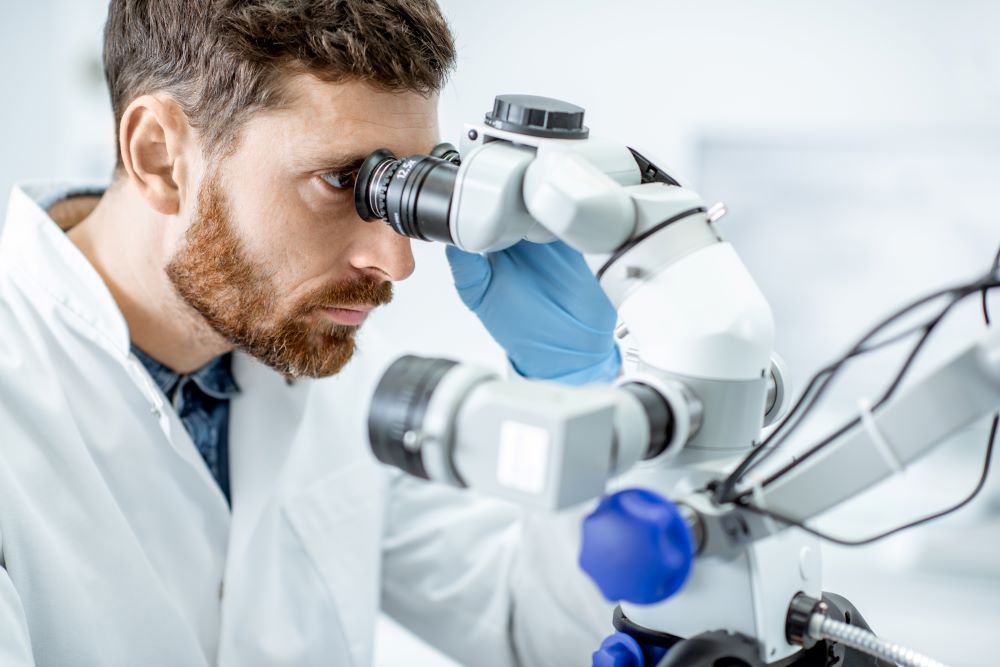
Ergonomic hazards in laboratories can lead to musculoskeletal disorders and other health issues resulting from repetitive tasks, poor posture, and improper workstation setups.
Tasks such as pipetting, microscope work, and prolonged computer use can cause strain and discomfort, impacting productivity and overall well-being.
Preventive Measures
- Proper Workstation Setup: Ensure that workstations are ergonomically designed, with adjustable chairs, workbenches, and computer screens set at appropriate heights to reduce strain.
- Ergonomic Equipment: Use ergonomic tools and equipment, such as pipettes with comfortable grips, adjustable microscopes, and cushioned floor mats, to minimise discomfort during repetitive tasks.
- Regular Breaks: Encourage taking regular breaks to stretch and move around, reducing the risk of repetitive strain injuries.
- Task Rotation: Implement task rotation to prevent prolonged periods of repetitive activities, allowing different muscle groups to be used.
Importance of Reporting Lab Incidents
Incident reporting is a crucial aspect of maintaining laboratory safety. The act of reporting incidents aids in:
- Identifying hazardous situations
- Making adjustments to work practices, policies, or training
- Preventing future incidents
- Improving overall safety protocols
Reports of minor incidents or near misses can help identify trends or procedural lapses that might otherwise go unnoticed. Fostering a culture of reporting where there’s no fear of penalties or job discrimination is crucial for ensuring all incidents are documented and addressed.
Download our free guide for expert tips and detailed checklists to streamline your lab incident reporting process.
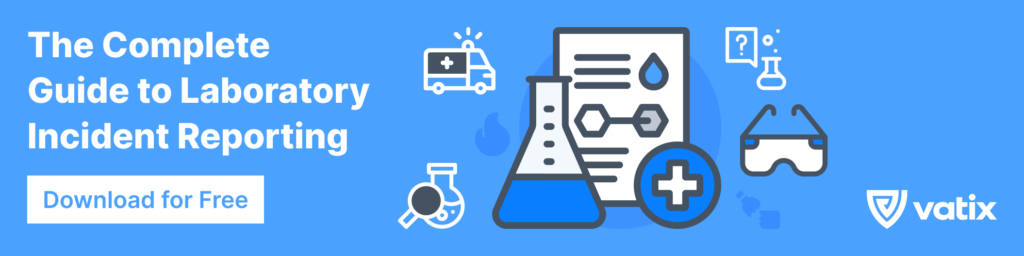
How Can We Help?
Vatix’s incident reporting software streamlines the incident reporting process for laboratory staff with the following key features:
- Real-Time Reporting: Staff can report incidents instantly via web, mobile app, or QR code, ensuring immediate logging of incidents.
- Immediate Notifications: Relevant staff are notified instantly upon report submission, enabling a quicker and more effective response to incidents.
- Corrective Action Assignment and Monitoring: Assign and track corrective actions related to an incident, ensuring issues are promptly addressed and resolved effectively.
- Customisable Report Templates: Tailor incident forms to fit your laboratory's specific requirements, capturing all relevant information accurately. Upload photos and attachments for comprehensive documentation.
- Advanced Analytics Dashboard: Identify trends, track KPIs, and generate detailed reports with a tailored analytics dashboard, allowing for informed decision-making and effective safety strategy implementation.
- Centralised Data Repository: Store all incident data in a single, accessible database for organised analysis and streamlined incident management.
Conclusion
Lab safety is a multifaceted challenge that requires a comprehensive approach to prevent accidents and ensure a safe working environment. By understanding the most common laboratory hazards and implementing preventive measures, we can significantly reduce the risk of incidents occurring.
Incident reporting plays a crucial role in identifying hazardous situations and improving safety protocols. Using an incident reporting software can streamline the reporting process, enhance accountability, and ensure regulatory compliance, ultimately fostering a proactive safety culture.
To learn more about how can Vatix can help streamline your laboratory incident reporting, talk to our sales team here.