Workplace injuries are a significant concern for businesses and employees alike, impacting productivity and well-being.
Recognising the hazards in your workplace is crucial for fostering a safer work environment, complying with dangerous occurrences regulations, and minimising the risk of harm to employees.
In this article, we will explore 8 of the most common causes of workplace injuries and provide practical tips on how to avoid them.
1. Repetitive Strains and Overexertion
Repetitive strain injury (RSI) occurs when repetitive motions or overuse of certain muscles and tendons lead to pain and damage.
Common examples of RSI include carpal tunnel syndrome, tendonitis, and bursitis. These injuries typically affect the hands, wrists, elbows, shoulders, and neck, causing discomfort and potentially long-term damage if not addressed.
RSI is often caused by performing continuous or repeated tasks that require repetitive motions or maintaining awkward or static postures for prolonged periods. Common activities that can lead to RSI include typing on a keyboard, using a mouse, and performing assembly line work.
Overexertion, on the other hand, happens when individuals push their bodies beyond their physical limits, often resulting in muscle strains, back injuries, and other musculoskeletal disorders.
Strategies to prevent these injuries include:
- Leveraging ergonomic workplace adjustments and ensuring that employees are trained and equipped with safety gear such as harnesses and back braces.
- Encouraging employees to take regular breaks to stretch and move around, as well as rotating tasks among employees to prevent any one person from performing the same repeated activity for extended periods.
2. Falls From Height
Falls from height are a common workplace accident, and can result in serious injuries such as fractures, head trauma, and even fatalities.
These accidents are common in industries like construction, maintenance, and warehousing, where employees often work on ladders, scaffolding, roofs, and elevated platforms.
The Health and Safety Executive (HSE) sets out critical guidelines for employers that require their staff to work at heights. This includes the requirement to perform a risk assessment and provide necessary equipment such as harnesses and safety nets to protect workers from falls.
Employers can also reduce the risk of these accidents by implementing the following measures:
- Installing sturdy handrails on stairs and guardrails on elevated platforms, which provide additional support and prevent falls. Encouraging the use of appropriate footwear with non-slip soles can also help maintain traction.
- Conducting regular inspections of work areas, equipment, scaffolding, and safety system to identify and address any potential hazards.
By prioritising safety in the planning stages, the risks associated with working at height can be significantly reduced, safeguarding employees against one of the most hazardous workplace scenarios.
3. Handling, Lifting, and Carrying
Handling, lifting, and carrying injuries are common in workplaces where employees frequently move heavy or awkward objects.
These injuries can result in strains, sprains, back injuries, and even more severe musculoskeletal disorders.
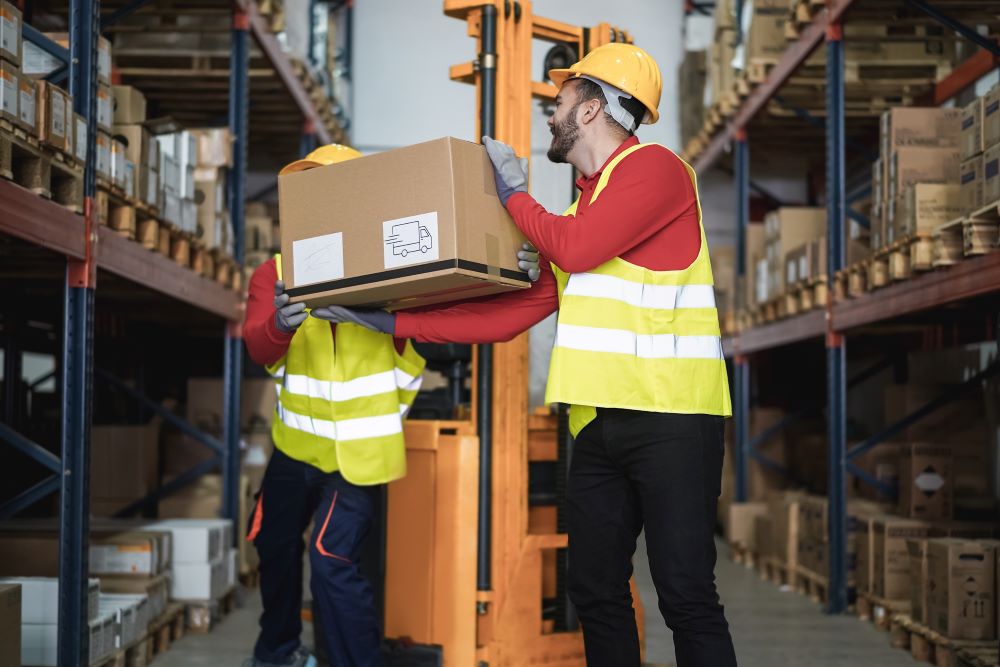
To prevent these types of workplace accidents, it's essential to implement the following measures:
- Train employees on proper lifting techniques. Emphasise bending at the knees, keeping the back straight, and using leg muscles to lift rather than the back. Avoid twisting or bending while lifting.
- Provide mechanical aids such as hand trucks, trolleys, and forklifts to assist with moving heavy items. Ensure employees are trained on how to use these aids safely and effectively.
- Provide appropriate PPE such as gloves with good grip, back braces, or lifting belts when necessary. Ensure that employees use PPE correctly.
- Encourage employees to assess the weight and size of loads before lifting. If a load is too heavy or awkward to lift alone, employees should seek assistance or use a mechanical aid.
- Encourage employees to take regular breaks, especially during tasks that involve repetitive lifting or carrying. This helps to reduce muscle fatigue and the risk of injury.
4. Slips and Trips
Slips and trips are among the leading causes of workplace injury. These incidents can happen anywhere and are capable of inflicting various injuries, from minor bruises to debilitating fractures.
These incidents are often the result of deceptively simple hazards: an unmarked spill, an uncovered cable, inadequate lighting, or cluttered work areas.
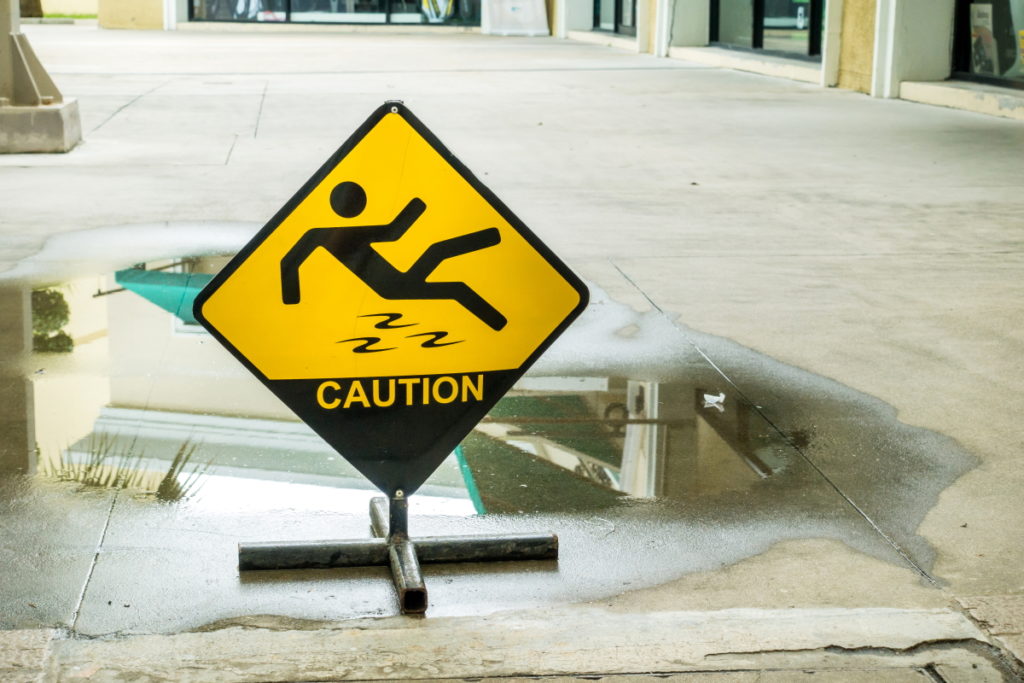
To prevent these workplace accidents, it is essential to:
- Maintain clean and dry floors, promptly clean up spills and use clear warning signs to indicate wet areas. Ensuring walkways are well-lit, free of clutter, and items are stored properly can help prevent tripping hazards.
- Conduct regular maintenance and inspections are essential to identify and address hazards like loose flooring and uneven surfaces.
- Use a personal safety device or app with fall detection to add an additional layer of protection. These technologies can detect when someone has fallen and automatically trigger an SOS alarm, ensuring that help is quickly on the way. These alarms especially beneficial for workers who are alone or in isolated areas, as it ensures they can receive prompt assistance even if they are unable to request help themselves.
5. Impact Injuries
Impact injuries are common workplace accidents that occur when an individual is struck by a moving or stationary object, causing a sudden force or blow to the body.
These injuries can range from minor bruises and contusions to severe trauma such as fractures, concussions, and internal injuries. Impact injuries are common in environments where heavy machinery, tools, or moving objects are used.
Preventing this type of accident at work requires a proactive approach, including the implementation of safety protocols, training, and the use of protective equipment:
- Ensure that employees wear appropriate personal protective equipment (PPE) such as hard hats, safety goggles, steel-toed boots, and gloves. Employers should also provide comprehensive training on the proper use of equipment, awareness of potential hazards, and safe work practices.
- Maintain a secure work environment through regular inspections and maintenance of equipment.
- Secure storage areas to prevent objects from falling and use clear signage and floor markings to indicate hazardous areas.
6. Exposure to Hazardous Substances
Exposure to hazardous substances is a significant risk in many workplaces, particularly in industries such as manufacturing, construction, and laboratories.
Hazardous substances can include chemicals, dust, fumes, vapours, and biological agents that can cause acute or chronic health issues, ranging from skin irritation and respiratory problems to more severe conditions like chemical burns and cancer.
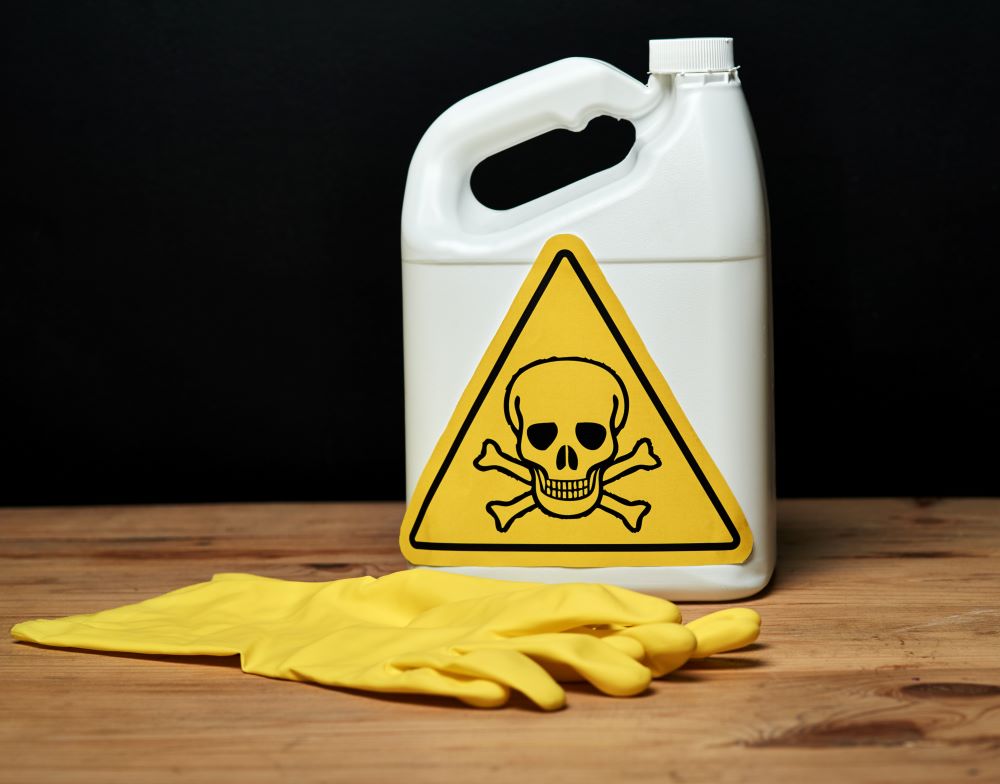
Preventing these hazards involves a combination of measures on the hierarchy of control, including engineering controls, administrative measures, and personal protective equipment (PPE):
- Improving ventilation is a primary engineering control; this can be achieved by installing proper exhaust systems to reduce the concentration of airborne hazardous substances. Using local exhaust ventilation (LEV) systems can capture emissions at the source, preventing them from spreading throughout the workplace.
- Administrative measures include regularly monitoring air quality, implementing strict protocols for handling and storing hazardous substances and ensuring thorough cleaning and maintenance of workspaces to reduce dust and biological hazards.
- All hazardous substances must be clearly labelled with appropriate warning signs and stored in designated areas. Use proper containers and storage methods to prevent leaks and spills.
- Provide employees with the necessary PPE, such as gloves, masks, respirators, and protective clothing, especially in environments where exposure levels cannot be adequately controlled by other means. Ensure that PPE is used correctly and consistently.
Training employees on the risks associated with hazardous substances and the correct use of PPE and safety equipment is essential to ensure compliance and safety.
By combining these preventive strategies, workplaces can significantly reduce the risk of exposure to hazardous substances, protecting the health and safety of employees and ensuring a safe working environment.
7. Burns
Burn injuries in the workplace can arise from various sources: contact with fire or hot surfaces, electrical currents, or corrosive chemical substances. These injuries are most common in kitchens, manufacturing plants, laboratories, construction sites, and any environment where employees handle hot surfaces, chemicals, or electrical equipment.
Burns can occur unexpectedly, with common causes including faulty gas lines, improper storage of combustible materials, or careless handling of open flames. The aftermath of such accidents can be severe, with the potential for respiratory damage, varying degrees of burns, and long-term scarring.
To minimise the risk of burns, preventive measures are of utmost importance. Here are some key strategies:
- Establish and enforce safety protocols for handling hot surfaces, chemicals, and electrical equipment. Ensure all employees are aware of and follow these guidelines.
- Regularly inspect and maintain equipment and work areas to ensure that they are free of hazards that could cause burns, such as exposed wiring, faulty machinery, or chemical spills.
- Provide and mandate the use of appropriate PPE such as heat-resistant gloves, aprons, face shields, and safety goggles to protect against thermal and chemical burns.
- Ensure that all employees are provided with and properly trained in handling and storing hazardous materials, using PPE, and emergency response procedures.
Proper first-aid training for employees and easy access to first-aid supplies can significantly improve the outcome of burn incidents. Additionally, all burn incidents should be reported and investigated to prevent future occurrences and improve workplace safety.
These measures can significantly reduce the risk of burn incidents and aid in the swift and effective treatment of such injuries.
8. Vehicle Accidents
Vehicle accidents in the workplace involve any incidents where employees are injured while operating or riding in motor vehicles, including cars, trucks, forklifts, and other mobile equipment.
These accidents can result in a range of injuries from minor bruises and whiplash to severe trauma or fatalities.
These accidents can occur due to various factors including driver error, poor vehicle maintenance, adverse weather conditions, and inadequate training. Common causes include distracted driving, speeding, fatigue, improper use of equipment, and lack of adherence to safety protocols. In industrial settings, accidents can also occur due to collisions with other vehicles or objects, or when vehicles overturn.
Prevention begins with meticulous risk assessments, guaranteeing safety-centric transport activities, including:
- Establishing loading and unloading procedures.
- Proper training and refresher courses for vehicle operators, including training on how to handle adverse weather conditions and ensure that vehicles are equipped to handle such conditions.
- Regular maintenance and inspections of vehicles and equipment to ensure they are in safe working condition.
- Addressing driver fatigue by implementing policies that limit the number of hours an employee can drive without a break.
First Response: Immediate Steps Post-Accident
The period immediately following an accident is critical and can significantly impact the outcome for the injured individual.
Having a clear and practised response plan is critical to providing immediate care and mitigating the severity of the injuries sustained, while also ensuring all details are properly documented for any potential workplace injury claim.
Acquiring first aid and seeking professional medical care as promptly as possible are essential first steps post-accident.
Reporting the incident on the company's preferred incident reporting system ensures that the accident is documented accurately and legal obligations are met. This is crucial for any potential compensation claim.
Download our free Essential Guide to Health & Safety Incident Reporting for a detailed step-by-step checklist for how to respond to and report an accident at work.
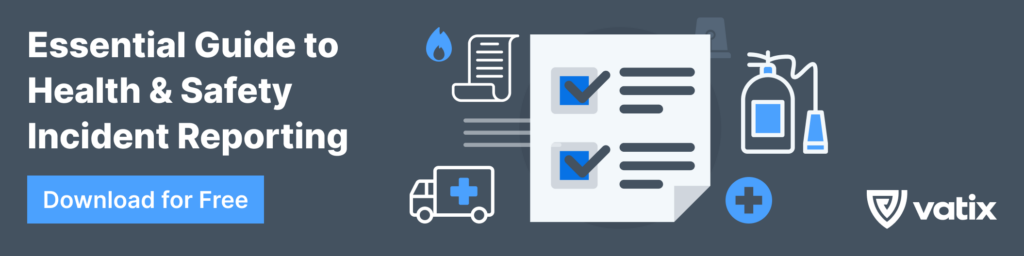
Reporting a Workplace Accident
In the broader framework of occupational health and safety, reporting workplace injuries and incidents is a vital step.
Prompt and accurate reporting facilitates improvements in safety protocols and prevents future incidents. Documentation, including photographs of the injury and the cause, along with witness contact details, should be meticulously collected to support any subsequent investigations.
Vatix’s incident reporting software simplifies the reporting process, enabling easy reporting of incidents via mobile or web app and the assignment and monitoring of follow-up corrective actions to prevent future incidents.
Organisations can leverage this platform to identify trends, track KPIs, and generate detailed reports with a tailored analytics dashboard, helping to identify workplace hazards and implement effective safety strategies.
Summary
The impact of workplace accidents goes beyond immediate physical harm, encompassing significant financial losses, operational disruptions, potential accident liabilities, and legal fees. That's why having effective prevention strategies is crucial to safeguarding employee well-being and maintaining smooth, cost-efficient operations.
Creating a proactive and safety-first culture involves encouraging the use of hazard and incident reporting systems, conducting in-depth safety measure training, and enforcing strict adherence to health and safety regulations. By embedding these practices into the fabric of the workplace, employers can significantly reduce the incidence of workplace injuries and the legal costs associated with them.
To discover how our solutions can protect your employees and enable them to report workplace incidents, get in touch with our sales team here.