When seconds and inches are the only things preventing an accident, you’ve witnessed an example of near miss.
These incidents are crucial for identifying potential hazards and improving workplace safety.
Here, we'll examine clear, actionable examples that demonstrate how a workplace accident was narrowly avoided.
You’ll gain insights into potential risks and the importance of reporting and addressing them promptly.
What is a Near Miss?
A near miss is an event that could have resulted in harm, illness, or significant property damage with only slight changes in circumstances.
What separates a near miss from an accident is the fortunate lack of serious consequences.
Each scenario offers a valuable lesson, revealing potential dangers and underscoring the need for stronger safety protocols.
List of Near Miss Examples
A major reason why near misses go unreported is that employees often don't recognise them. Here are some real-life examples of near misses across various industries.
Slips, Trips, and Falls
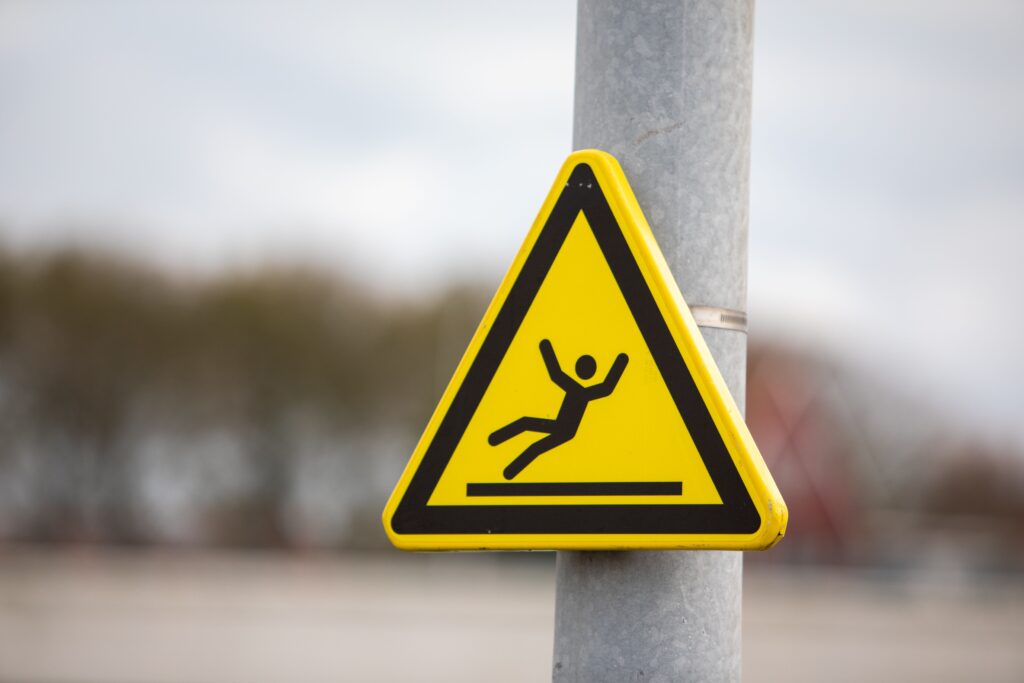
- An employee nearly slips on a recently mopped floor that was not marked with a wet floor sign.
- A worker trips over a small pile of boxes left in a walkway but manages to catch themselves on a nearby table.
- Loose carpeting on an office floor causes an employee to stumble, narrowly avoiding a fall.
- A spill in the cafeteria is quickly cleaned up before anyone slips, thanks to an alert coworker.
- During night shift, an employee almost falls into an uncovered manhole in the parking area, which was poorly lit.
- A stairwell light burns out, and an employee misses a step but grabs the handrail just in time to prevent a fall.
- An employee almost slips on ice at a building entrance.
Machinery and Equipment Use
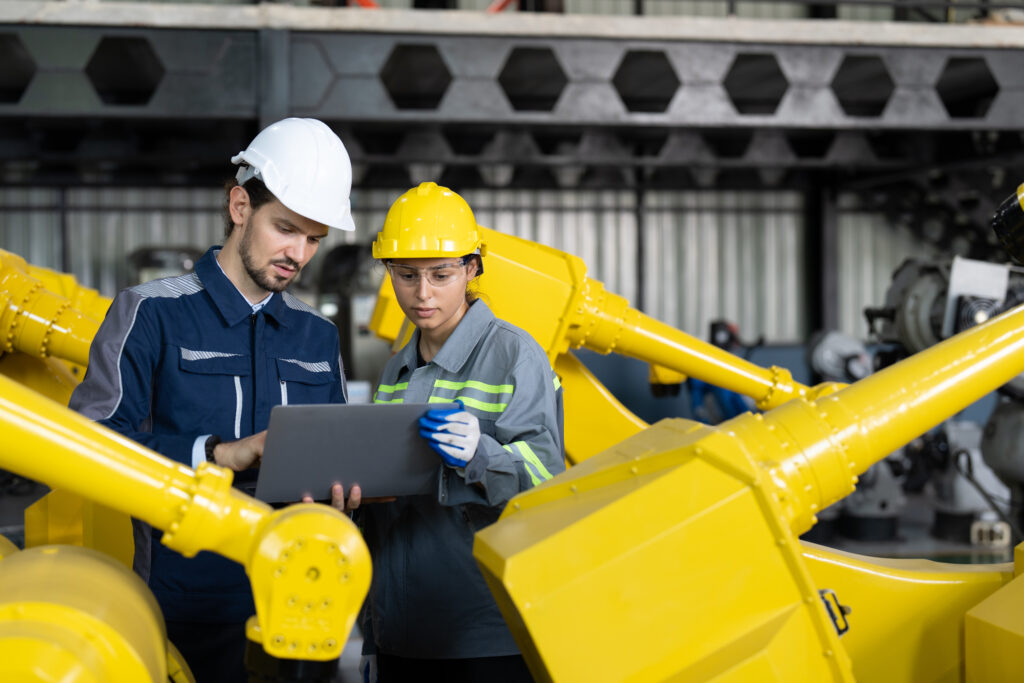
- A guard is found missing on a saw machine just before use, preventing potential injury.
- An electrical tool is found to be faulty during pre-use checks, preventing possible electrocution.
- A press machine nearly activates while a worker's hand is inside, but the safety shutoff is engaged in time.
- A gas leak is detected in a boiler room before it can ignite or cause health issues.
- A conveyor belt starts unexpectedly, but an emergency stop is hit before anyone is caught in the machinery.
- A vehicle's reverse alarm is not functioning, but a spotter prevents an accident with pedestrians.
- A forklift operator notices a hydraulic fluid leak before starting the day's work, preventing potential machinery failure and injury from sudden loss of lift capacity.
Working at Heights
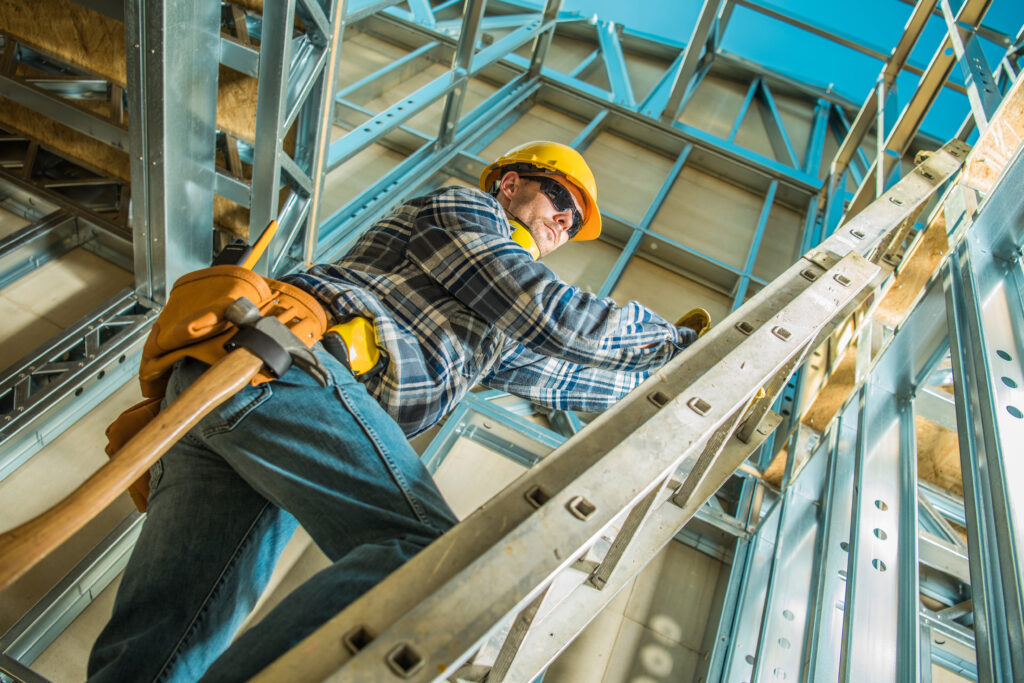
- A scaffolding plank nearly gives way under a worker, but they step off in time onto a secure platform.
- A worker's safety harness is found to be defective during a pre-work inspection, preventing a potential fall.
- A ladder starts to slide sideways, but another worker stabilises it before anyone falls.
- During roof work, a worker nearly steps backwards off the edge but is called out by a coworker just in time.
- A tool is dropped from a height but doesn't hit anyone.
- On a construction site, a temporary guardrail is dislodged but noticed and fixed before anyone leans against it and potentially falls.
Chemical Handling and Storage
- A chemical spill occurs in a lab, but is quickly contained and cleaned up before anyone is exposed.
- Two incompatible chemicals are nearly mixed, but a double-check of the labels prevents a dangerous reaction.
- A leaking gas cylinder is discovered in a storage area before it can cause health issues or explosions.
- An employee nearly uses the wrong protective equipment when handling a corrosive substance, but a supervisor intervenes.
- During routine inventory, a bottle of highly reactive substance is found stored above recommended temperature limits, but is promptly moved to a proper storage environment.
- A laboratory reaction starts to overheat, but the situation is quickly controlled with emergency cooling measures, preventing a potential explosion or release of toxic fumes.
Signage and Communication Failures
- Two forklifts almost collide at a warehouse intersection due to missing traffic flow signs.
- A temporary electrical hazard is not immediately signed, leading to a close call with an unaware employee.
- A worker nearly activates a machine while it is still undergoing maintenance because the 'under maintenance' sign was not displayed prominently.
- A failure to communicate overhead work leads to a near miss when materials are dropped close to where employees are walking.
- A newly installed piece of equipment lacks the appropriate hazard signage, leading to a near miss when an employee unknowingly operates it without the required safety precautions.
Risky Behaviour and Horseplay
- An employee decides to jump from the tailgate of a delivery truck instead of using the step, risking injury from the impact on landing.
- Attempting to retrieve items from a high shelf without a ladder, a staff member climbs the shelving unit, risking a fall.
- Ignoring signs of fatigue and dizziness, an employee continues working at a height, nearly leading to a loss of balance.
- Light-hearted shoving between two colleagues in a workshop almost results in one being pushed into a piece of active machinery.
Why is it Important to Report Near Misses?
Though near misses may not lead to immediate injury or destruction like accidents do, they are key indicators of possible safety risks in the workplace.
It is vital to treat every near miss seriously and ensure they are reported accurately, not just to internal management but also in line with legal obligations.
In the UK, organisations are legally obliged to report certain types of near misses under RIDDOR.
This legislation mandates that employers, the self-employed, and those in control of work premises report specified workplace incidents, including near misses that could have led to serious injury or ill health.
However, a systematic, proactive approach to near miss reporting can help organisations in various ways outside of any legal responsibilities:
- Prevents near misses from escalating into severe incidents in the future.
- Better identifies patterns and enhances risk control measures.
- Helps employees feel safe to report incidents (near miss incidents often go unreported because employees fear blame or don't want to deal with complex processes).
Ultimately, every near miss report is a stepping stone toward a safer workplace and ensures every potential hazard is documented and addressed.
How to Prevent Future Incidents
Learning from near misses is integral to maintaining a safe and productive workplace.
Understanding near miss incidents is crucial for recognising and preventing potential workplace accidents.
By addressing the root causes of these near misses before they escalate into incidents, organisations can protect their employees and resources.
Training and Education
Investing in proper training and education programs is crucial for empowering employees with the knowledge and skills they need to identify potential hazards and avoid accidents.
Regular training sessions should cover:
- Recognition of Hazards: Teach employees how to identify potential safety risks in their daily tasks and the broader work environment.
- Safety Protocols: Ensure that all employees are familiar with the company’s safety procedures, including the use of personal protective equipment (PPE), emergency response actions, and safe operation of machinery and equipment.
- Near Miss Awareness: Educate employees on what constitutes a near miss and the importance of reporting these incidents to prevent future accidents.
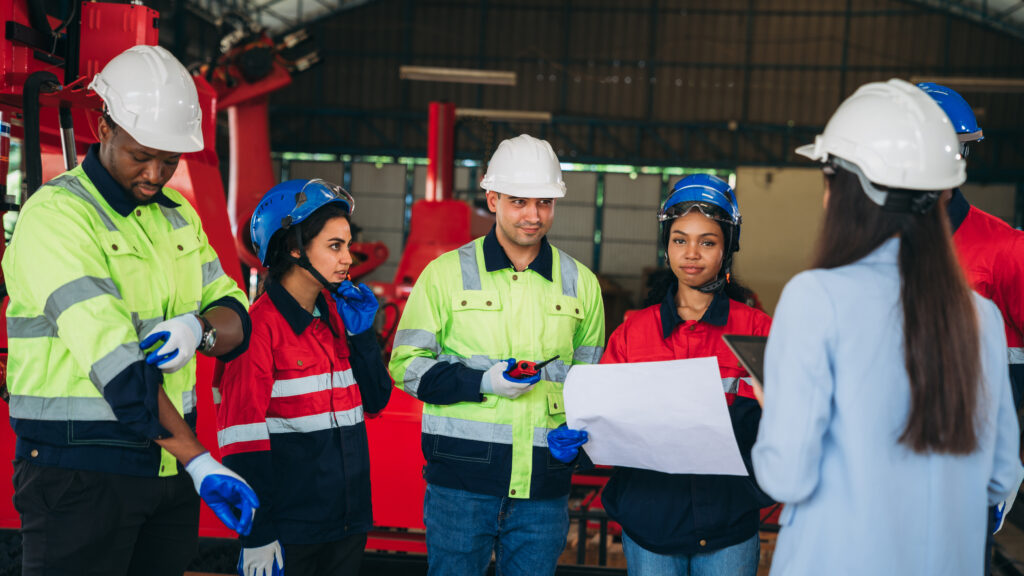
Interactive training methods, such as workshops, simulations, and safety drills, can enhance learning and retention, making safety a continuous conversation.
Open Communication
Open communication is pivotal in preventing future incidents. It involves creating an environment of trust and transparency, where employees feel comfortable and encouraged to share their observations, concerns, and suggestions related to workplace safety without fear of judgment or reprisal.
This open dialogue helps in identifying and addressing safety issues before they escalate while promoting a culture of collective responsibility for safety.
Feedback loops are also established. Employees are informed about the outcomes of their reports and the measures taken to address the reported near misses.
This recognition can reinforce the value of their contribution to workplace safety.
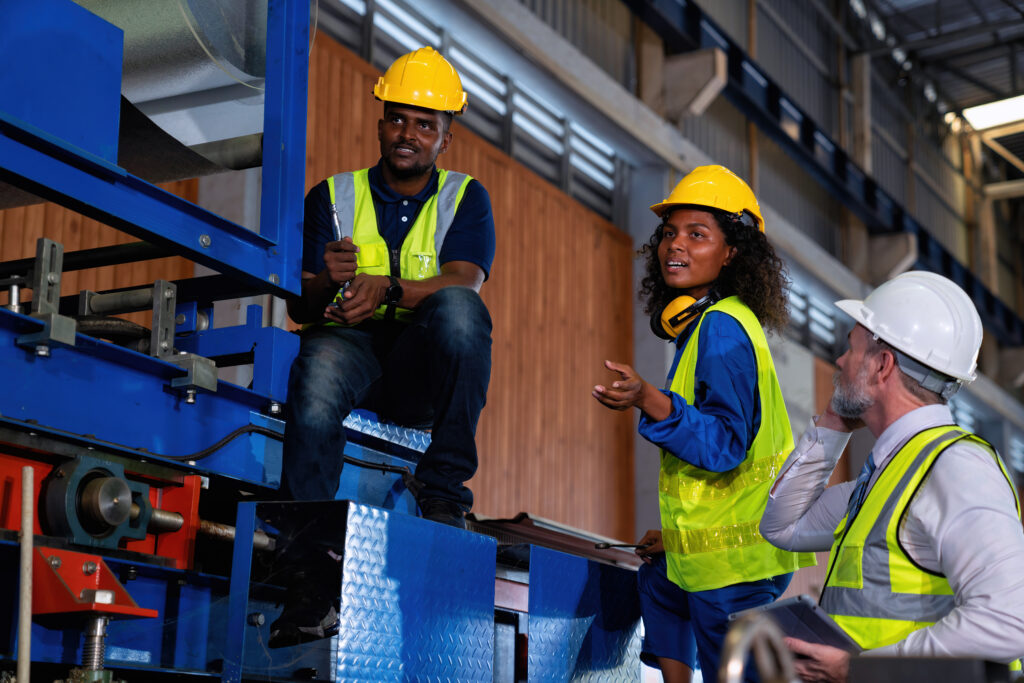
Regular Safety Audits
Conducting regular safety audits is an essential practice in the ongoing effort to prevent workplace incidents.
These audits involve systematic examinations of all operational aspects, including processes, equipment, and the work environment, to uncover potential safety hazards that might not be immediately obvious.
Through these audits, potential areas for improvement are identified, allowing for timely intervention and fostering a culture of continuous enhancement in safety practices.
Identifying non-conformance with safety standards and reporting unsafe conditions or hazards that could lead to near misses is a crucial outcome of these audits.
Audits and inspections software simplifies and streamlines the process, ensuring workplace hazards are quickly identified and addressed.
Streamlined Near Miss Reporting Processes
Implementing an efficient near miss reporting system accessible to all employees is the backbone of a proactive safety culture.
It plays a key role in identifying potential hazards early on, which fosters a culture of safety awareness that significantly contributes to preventing future incidents.
Vatix's near miss reporting platform simplifies the learning process from near miss incidents. It offers customisable analytics dashboards that provide valuable insights into root causes and trends, which guide strategic improvements to prevent future accidents.
Additionally, users can assign and track preventive and corrective actions, centralising all related communications and follow-up actions in a single location to ensure nothing slips through the cracks.
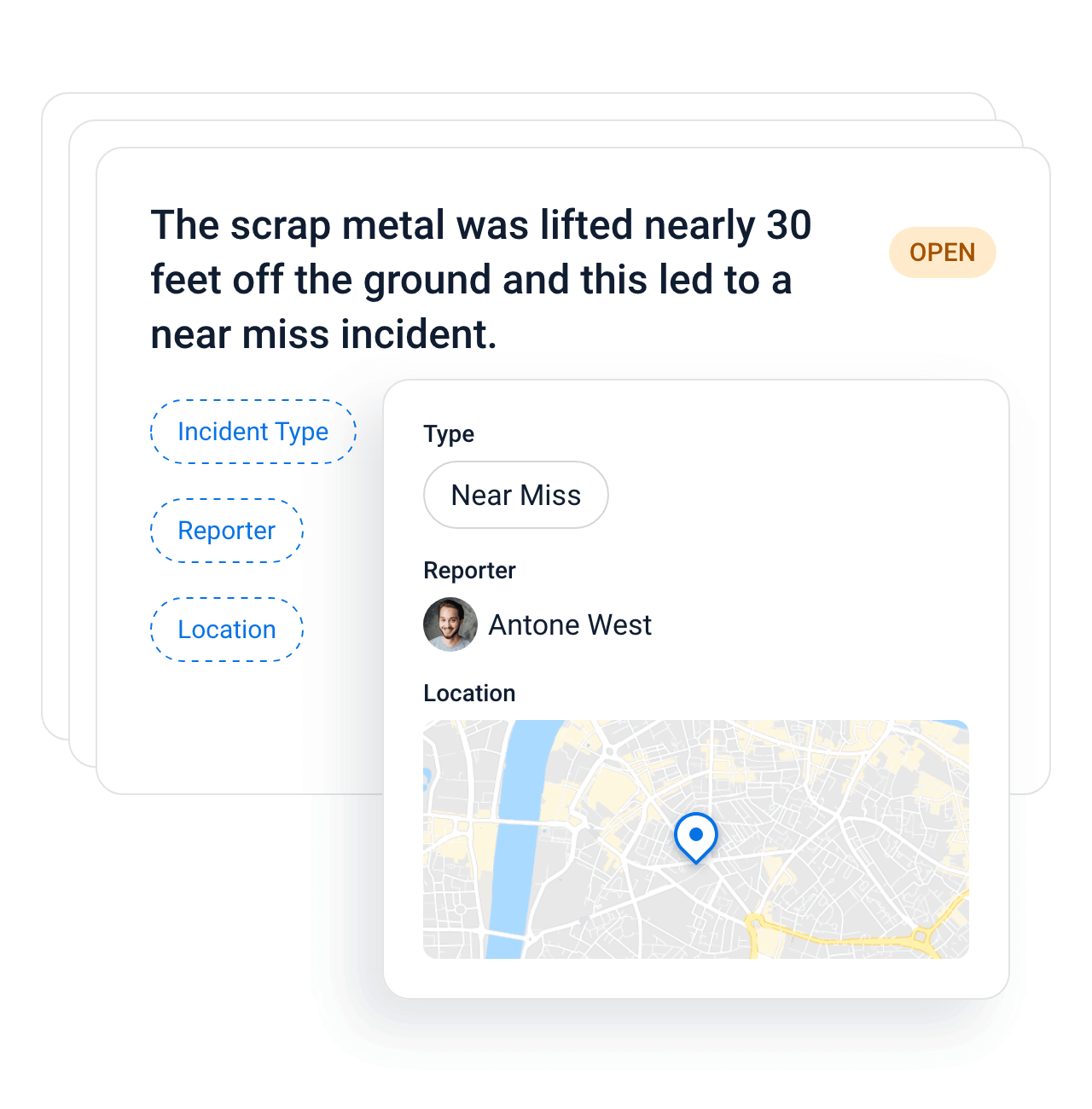
Summary
A near miss is not just a lucky escape—it’s an opportunity for learning and improvement.
By understanding what a near miss is and the importance of reporting them, we can recognise potential workplace hazards and mitigate risks.
Implementing best practices for prevention, choosing the right tools for reporting, and encouraging open communication are crucial steps toward a safer workplace.
Every near miss report is a chance to prevent future accidents, and by fostering a culture that values safety, we can transform these close calls into a driving force for good.
To discover how our platform can streamline your organisation's near miss reporting, talk to our sales team here. Plus we've got a handy checklist for you to download below that will help get you started with near miss reporting.
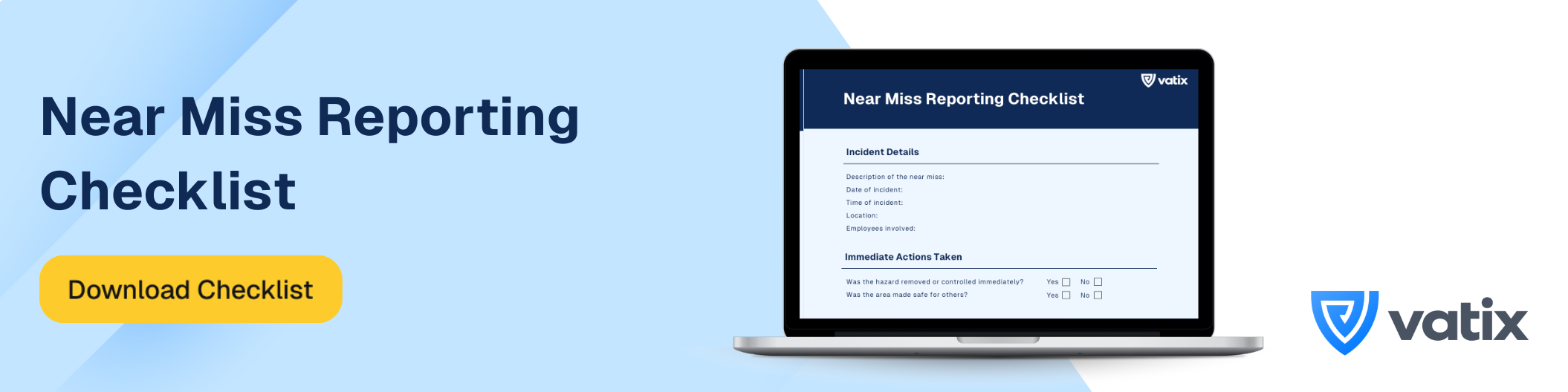